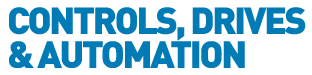
![]() |
Charlotte Stonestreet
Managing Editor |
Home> | AUTOMATION | >Condition Monitoring | >As Long As The Wind Blows |
Home> | POWER TRANSMISSION | >Drives | >As Long As The Wind Blows |
Home> | POWER TRANSMISSION | >Gear Drives | >As Long As The Wind Blows |
Editor's Pick
As Long As The Wind Blows
02 November 2012
Renewable energy – energy which comes from natural resources – contributes around 16% of global final energy consumption. New renewables (small hydro, modern biomass, wind, solar, geothermal, and biofuels) account for just 3%, though are growing very rapidly
According to a 2011 projection by the International Energy Agency, solar power generators may produce most of the world’s electricity within 50 years, dramatically reducing the emissions of greenhouse gases that harm the environment. But at present, wind power is increasing at an annual rate of 20%, with a worldwide installed capacity of 238,000MW at the end of 2011.
In October, the CBI director general John Cridland commented on the gas energy debate and the UK’s future energy needs: "A diverse energy mix, combined with market certainty, will be crucial if the UK is to have a secure and affordable energy supply in the future. An over-reliance on new gas would leave us exposed to global price and supply fluctuations and jeopardise our carbon targets, so we need to build more of everything, including renewables, nuclear and CCS.” The Department of Energy and Climate Change (DECC) and the Technology Strategy Board are to invest up to £11.2m in technical feasibility studies to stimulate innovation in the UK offshore wind sector and to strengthen the supply chain. The competition for feasibility studies opens on 5 November 2012. Details on https://connect.innovateuk.org/web /9214127/overview
LIQUID AIR – THE FUTURE RENEWABLE?
There is more than enough wind and solar energy available to power the world. We just need to harness it and store it so that we can use it when and where we need it, instead of only when the sun is shining or the wind is blowing.
The technology could make wind turbines more viable, by storing excess production at high wind speeds, releasing it again in calm weather, according to Dr Tim Fox, of the Institution of Mechanical Engineers. "Liquid air is important because it represents an opportunity for renewables to come online in significant volumes. It’s really about wrong time energy, or capturing the intermittent generation of offshore wind at times when there is no demand for electricity,” says Fox. "Storage is one of four tools we have to balance supply and demand, including thermal flexing (switching on and off gas-fired power stations); interconnections, and demand-side management. Ultimately it will be down to economics.” The technology was originally developed by Peter Dearman, a garage inventor in Hertfordshire to power vehicles. For the past several years, UK high-tech firm Highview Power Storage has been working to transfer Dearman's innovation to a system that can store energy for power grids. It has built a pilot plant next to a power station in Slough to prove the technology works.
At times of low demand for electricity, the plant uses the excess energy from the power station to suck air through refrigerator-style compressors turning it into a liquid, which it then stores in an insulated tank.
When consumer demand spikes, the energy is returned to the national grid. The tank, which stores 60 tonnes of liquid air, can power 6000 homes for one hour.
In the process, ‘wrong-time electricity’ is used to take in air and remove the carbon dioxide and water vapour (these would freeze otherwise). The remaining air, mostly nitrogen, is chilled to -190˚C and turns to liquid, the process which stores the energy. The liquid air is held in a giant vacuum flask until it is needed.
When demand for power rises, the liquid is warmed to ambient temperature. As it vaporises, it drives a turbine to produce electricity - no combustion is involved. Fox says this process is currently only 25% efficient, but it could be massively improved by cositing the cryo-generator next to an industrial plant or power station producing low-grade heat that is currently vented and being released into the atmosphere. The heat can be used to boost the thermal expansion of the liquid air.
More energy is saved by taking the waste cool air when the air has finished chilling, and passing it through three tanks containing gravel. The chilled gravel stores the coolness until it is needed to restart the air-chilling process.
Highview believes that, produced at scale, their kits could be up to 70% efficient. Chief executive officer, Gareth Brett believes that the technology is far cheaper than storing energy in batteries.
"Batteries are best suited to small applications like your laptop,” he says. "The national grid requires very large amounts of electricity to be stored. There are relatively few ways of doing that and we think with liquid air we have found one of the few technologies that is truly scalable to grid scale usage.” "Batteries can get 80% efficiency so this isn't as good in that respect,” explains Dr Fox. "But we do not have a battery industry in the UK and we do have plenty of respected engineers to produce a technology like this. What’s more, it uses standard industrial components – which reduces commercial risk. It will last for decades and it can be fixed with a spanner.” Research by Imperial College suggests energy storage could reduce the number of power stations and national grid infrastructure needed, saving £10 billion.
MEDIUM SPEED DRIVE SYSTEMS
The majority of wind turbines use high-speed geared drive trains. There is a strong perception across the industry that gearboxes are unreliable and prone to failure, despite statistics on turbine and drive-system performance showing that gearbox failure is no longer a major issue.
Fuelled by high rare earth metal prices and market volatility, turbine drive systems comprising a twostage gearbox and medium-speed permanent-magnet generator (PMG) are now enjoying increasing interest across the wind industry, for both onshore and offshore.ABB, which offers high-speed geared, medium and low-speed geared, and direct drive systems, indicates that the relative magnet mass of direct drive generators is a factor of 10 higher than a highspeed geared system, both rated at 3MW.
Due to their compactness and favourable mass, integrated and semi- integrated medium-speed drive systems offer significant potential for reducing head mass compared to similarly rated classic non-integrated, high-speed drive trains. However, several wind experts independently point out the real potential for substantial head mass saving is with a completely new approach to turbine nacelle design. Simply adapting existing designs for accommodating a usually shorter integrated or semiintegrated medium-speed drive system might by contrast require additional measures.
Drive experts at German gear maker Winergy argue that compared to direct drives their latest medium-speed HybridDrive gearbox-generator system needs only around 20% of the quantity of magnets.
UK-based Condor Wind Energy’s planned 5MW turbine is one of the few medium-speed models planned for offshore use that comes with an eight-pole induction generator enabling 700rpm generator speed – roughly half that of 4-pole machines.
BLADE MONITORING
The wind power industry faces enormous challenges in monitoring the condition of wind turbine blades. Bosch Rexroth offers an innovative solution to the problem of how to ensure that turbines remain operational for long periods in often harsh climatic conditions.
Monitoring systems have to be able to react very quickly to swiftly shut down the rotor blades if required. If blades that are ice covered are not stopped ice can be hurled around, and can cause structural damage due to overloading.
Rexroth’s BLADEcontrol is a system that continuously monitors the condition of the rotor blades on wind turbines and immediately signals to the operator and/or the machine control of problems such as structural blade damage, ice build-up or lightning damage. It can keep track of the history of the blades condition to offer an ongoing forensic trail of wind turbine performance.
The Bosch Rexroth system works via accelerometer sensors (multidimensional piezo-electric accelerator sensors), which are glued directly into the rotor blades.
A data collector in the hub converts the analogue, measured oscillations into digital values and transmits these from the hub into the nacelle via WLAN. The digital data is then interpreted by the BLADEcontrol embedded processing unit.
SAFETY TECHNOLOGY
B&R is focussing on integrated safety technology for wind turbines. It centres around the SafeLOGIC safety controller, which can be seamlessly integrated into standard controller systems and offers not just digital inputs and outputs, but also analogue and temperature interfaces and safe speed measurement that meets both SIL3 and Performance Level e requirements.
The robust design of the X20 controller system is ideal for mastering the extreme conditions associated with offshore wind turbines. This system can handle the measurement and monitoring of key parameters such as voltage, frequency and phasing of the power mains while also calculating the amount of energy output by the wind turbine. In addition, B&R’s intelligent condition monitoring solution is easy to use and makes it possible to coordinate maintenance more effectively and avoid machine downtime.
Automatic code generation for MATLAB/Simulink makes it possible to transfer sophisticated control algorithms to B&R systems that maximize energy yield while minimising the load on machine components.
SLEW DRIVE GEAR SYSTEMS
Brevini has over a decade’s experience in the wind power industry where its lightweight, and compact slew drive gear systems are used to deliver high reduction ratios and torque ratings. In the UK and across the rest of the world it has been responsible for the installation of more than 70,000 pitch and yaw drives, each of which has been geared to provide continuous and reliable service for the life of the turbine.
Nacelle rotation is controlled by a planetary gear unit with an electric brake motor. Each turbine can have between two and eight gear units depending on its size.
SOLAR POWER BALANCE OF SYSTEM
Eaton’s Electrical Sector has extended its presence in the solar energy sector by supplying and installing complete BoS (balance of system) solutions for three major new solar energy parks (developed and owned by Lightsource Renewable Energy). The largest of the new parks, at Chittering in Cambridgeshire, has an installed capacity of 5MWp. Great Knowle Farm and Eastacombe Farm in Devon, have capacities of 2.5MWp and 3.5MWp respectively.
For each of the new solar energy farms, Eaton designed, supplied and constructed the electricity substations that provide the link between the photovoltaic panels and the national grid. At the Chittering and Eastacombe sites, three substations were installed while, for the smaller system at Great Knowle, only two substations were needed.

As Long As The Wind Blows
Each substation is equipped with Eaton DC junction boxes to provide connections for the incoming supplies from the PV panels, and multiple SolarMax TSSV 330kW inverters, which achieve maximum power point (MPP) efficiencies of 99%. The low-voltage AC supplies from the inverters feed Eaton Memform low-voltage switchboards rated at 3200A, which offer Form 4 separation and the high fault current capacity needed to ensure safe operation.
The substations also incorporate 280V to 11kV transformers and Eaton Xiria 11kV ring main units with integral G59 protection. These versatile units use vacuum switching technology to minimise maintenance requirements and environmental impact.
Key Points
- Firms are examining the feasibility of using normal air to store energy by cooling it to -190˚C
- Integrated and semi-integrated medium-speed drive systems offer significant potential for reducing head mass in wind turbines
- Brevini compact slew drive gear systems are used to deliver high reduction ratios and torque ratings in the wind power industry
- Hitachi completes acquisition of JR Automation
- Automation suite helps to program multi-axis projects
- All about efficiency
- Funding secured for Silverstone based Digital Manufacturing Centre
- The Power of AI in manufacturing
- Robotic investment helps deliver sales
- Emerson to buy Aventics
- Mesh network of sensors guides vehicles autonomously
- GM Group to make MACH debut
- More live demos than ever
- Schaefler Brakes World Record
- Parvalux Gives Mechanical Sculpture Drive
- HTQ DRIVE TECHNOLOGY
- VALVE ACTUATION SUPPORTS OFFSHORE WIND FARM
- MOTOR MANAGEMENT
- MAKING WAVES WITH TOUCHLESS TECHNOLOGY
- Laser Distance Measurement
- EXTERNAL COOLING & LUBRICATION SYSTEM
- IO-LInk Now Included
- RACK-AND-PINION REDESIGN CUTS GEAR SIZES