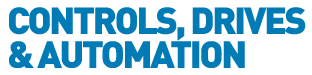
![]() |
Charlotte Stonestreet
Managing Editor |
Home> | AUTOMATION | >Handling & Logistics | >Rethinking contingency with automation |
Rethinking contingency with automation
01 February 2023
AS COMPANIES look to new ways to add resiliency and agility into supply chains, including a shift towards local sourcing, Wouter Satijn explains the importance of automated loading and unloading as part of a seamless production environment.

Recent supply chain disruptions and product shortages have called into question the feasibility of just-in-time (JIT) inventory practices. With ongoing disruption likely, adopting a just-in-case (JIC) approach of bigger stockpiles can help ensure continuity. But with a recession looming, the high upfront expenditure of just-in-case is not without its risks either. This is especially true within the automotive industry, given its sheer pace of change.
Rather than adding risk and cost, companies need a way to optimise existing space, equipment, and people. Yet while many production processes are automated, the continued reliance on manual processes for loading and unloading components is undermining the true JIT vision. The addition of automated loading and unloading systems supports the reliable and fast deliveries necessary for JIT practices, while also streamlining operations, minimising the risk of damage to high-value inventory, and utilising scarce resources.
Automotive innovation challenge
The pace of product design innovation in many industries continues to outstrip innovation within the manufacturing process. The automotive industry is a prime example: producing the latest generation of electric vehicles (EVs) has put a tremendous strain on 20th Century manufacturing facilities. The need to add or expand production lines to support battery installation, the latest self-driving safety features or ever more complex entertainment systems places significant space pressure on an already fully deployed plant.
In addition, the impact of global supply chain disruption has added another layer of complexity and challenge to any industry that has embraced JIT inventory practices. Delays in shipping key components over the past 30 months (especially from China), combined with inflationary pressures, have encouraged many businesses to consider new strategies, including adding contingency stock into the mix. Yet, with limited capacity to store additional stock, this is easier said than done.
Just in case debate
Where is the additional stock to be located? Is warehouse space available, and is it supported by the required warehouse management system (WMS)? How easily can this additional stock be moved back into the supply chain? What is the overall cost? With signs of economic slow-down globally, is now the time to be adding contingency stock to make products that may not be required? Given the pace of product design innovation, there is a very real risk of stockpiling components that could quickly go out of date.
JIT has transformed operations over the past few decades, allowing companies to eradicate waste and minimise the cost of holding and storing stock. But while supply chain disruption creates clear challenges for tightly integrated assembly processes, problems are not solely linked to glitches in supply and transport. Production lines are incredibly efficient, but pockets of manual operation remain hugely risky. Why, for example, are so many OEMs still relying on manual loading processes, with the attendant need for forklifts and operators, when the impact of component damage is devastating to the bottom line?
For automotive manufacturers, many new components that are now required are extremely expensive and more difficult to handle. Take rechargeable Lithium-Ion batteries, which are heavy and can be dangerous, or state-of-the-art touchscreen dashboards, which are highly vulnerable to damage, as they cannot be stacked on top of each other. This creates new challenges when unloading from the manufacturing facility into the assembly line. Many new components also require special protective racking that takes up additional space. Throw JIC into the mix, and a production manager would need to be a magician to seamlessly include these new demands within an ageing plant that is already space constrained.
End-to-end automation
While few industries have been able to create manufacture and assembly processes that keep pace with product design innovation, new market challengers are building greenfield sites with end-to-end automation. This is delivering a completely new level of efficiency. The new mega-factories built by challenger EV providers automate every stage, including unloading and loading, to further streamline the JIT assembly process.
Automated loading can eradicate damage caused by human error to parts such as bumpers or touchscreen dashboards, removing the risk of a vehicle being produced without all of its components. Likewise, with automation, there is no chance of the entire line being stopped while a replacement component is sourced – something that can cost the company £10,000s every minute. These new production facilities are not only far more efficient and cost-effective, but they are also lower risk and higher quality.
And that’s not all. Challenger companies are replacing outdated standards of operation with other novel approaches that radically improve efficiency and agility. For example, the traditional ‘one wheel at a time’ system used to unload wheels into a factory requires up to two hours to unload one lorry. In contrast, a recently installed automated wheel unloading system completes the entire process in less than three minutes. That means fewer HGV drivers for the same number of loads, minimal demand for scarce forklift drivers, and far more certainty over delivery timelines, supporting greater confidence in JIT processes.
Supply chains depend on close-knit, reliable partnerships, and with the growing shift towards local sourcing, the way these companies interact must be ever more agile. Every organisation needs confidence in how inventory is managed both internally and by partners to support JIT operations. Gaining certainty in the quality, efficiency, and timeliness of unloading and loading processes will become increasingly important as companies reconsider process optimisation in the face of changing demand and supply.
Wouter Satijn is sales director at Joloda Hydraroll
- £53 million funding for UK manufacturers
- Extra set of arms for surgeons
- First consumer testbed for 5G technology
- Pack it up, pack it in
- Alternative to furlough urged for engineers
- ARE YOU READY FOR…THE INTERNET OF THINGS?
- Chancellor backs 4IR at parliamentary group launch
- Call for urgent action to decarbonise
- Ultra-compact IoT solution for edge & automation
- ZX Spectrum relaunched as gaming console