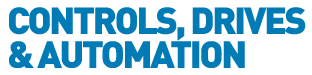
![]() |
Charlotte Stonestreet
Managing Editor |
Home> | POWER TRANSMISSION | >Gear Drives | >RACK-AND-PINION REDESIGN CUTS GEAR SIZES |
RACK-AND-PINION REDESIGN CUTS GEAR SIZES
02 November 2012
Drives manufacturer Stober has joined forces with New Jersey-based rack specialist, Atlanta, to develop a compact, efficient rack-and-pinion drive system with a built-in output bearing housing
However, the overhung load on the gear unit from the rack and pinion combination is then so high that it may determine the size of the drive. Looked at another way, utilisation of the gear unit's actual torque would normally be only in the 40 to 60% range.
Drives manufacturer Stober has joined forces with the rack specialist Atlanta, a gear rack manufacturer based in Farmingdale, New Jersey, to develop a compact, efficient rackand- pinion drive system with a built-in output bearing housing – a stiff supporting assembly for the pinion which relieves the load on the flange-mounted planetary gear bearings.
The internal contour of the cast supporting bearing cover is designed with stiffening ribs to provide a highly stiff supporting assembly for the gear rack pinion.Pinion and cover are bolted to the housing and shaft flange of the PH(A) series. At the same time, the cover serves as a protective housing and is used for mounting the optional lubrication device, comprising a felt lubricating pinion running in parallel.
Due to the special shape of the pinion with integral flange, the number of teeth can be determined independently of the flange shaft on the gear unit. The smaller pinion generates less torque. The shorter lever reduces linear backlash. The pinion concentricity can be set at less than 10 microns.
The reduced tilting moment of this construction makes it possible to design the drive based on the torque that is actually needed, as well as the feed force. This will often mean that smaller gears can be used than in the past. And because of the comparatively small pinions, a higher output speed is needed to obtain the required feed rate. This means that the gear ratio is lower and, in many cases, a single-stage planetary gear system can be used instead of a two-stage.
This gives the HighForce ZTRSPH( A) rack-and-pinion drive, which based on Stober's PH and PHA precision planetary gear units, an extremely high power density and could enable machine builders to redesign their machines. The ratios range from 4-121 :1 and are available in rightangle versions and with built-on motors. But if desired, the ZTRS can be attached directly to any servomotor. The HighForce ZTRSPH( A) rack and pinion drive is now available in sizes 7, 8 and 9, modules 2 to 6 and gearing quality 5.
Because the pinions in the new design do not have to be flangemounted directly onto the gear flange shaft’s bolt circle, linear stiffness is also improved.
SERVO BALLSCREW MOTOR RANGE
Stober has unveiled a range of servo ballscrew motors that drive rotating spindles or spindle nuts directly. The dynamic, high-torque motors are based on the new PipeDrive hollow shaft geared motors featuring an extremely compact design of the motor and gears.
One version (type EZS) is designed to drive screw drives with a rotating screw shaft. The screw nut will usually be connected to a linear slide, which it drives. The screw is fixed by inserting it into the motor’s blind-hole hollow-shaft, and connecting it to a clamping set.
Screws with four diameters from 20 to 40mm can be used, depending on the frame size. To absorb the high axial thrust, the EZS motors are fitted with special axial angular contact ball bearings. The second version (type EZM) is aimed at screw drives with driven nuts. Its large flanged hollow shaft can drive flanged spindle nuts directly.
The motors achieve their short lengths by using an orthocyclic tooth winding system with a high copper fill factor, producing about 80% more power than a conventional winding. Both types are available in two sizes, three lengths and four spindle pitches (10 to 32mm). They can also be supplied as brake motors and with liquid cooling. Forced-cooling fans are available as an option for the EZS models.
Key Points
Stober’s efficient rack-and-pinion drive system has a built-in output bearing housing
- Due to the special shape of the pinion with integral flange, the number of teeth can be determined independently of the flange shaft on the gear unit
- A shorter lever reduces linear backlash
- Precision racks have twice the holes
- Drive system combination
- Compact & versatile planetary gear units
- New Winding Technology
- Motor removal on the vertical axis
- Automated drive for heavyweight loading
- Online drive solution configurator
- Live motion control demonstrations
- Enhanced predictive maintenance
- Compact drives for depowdering system
- Parvalux Gives Mechanical Sculpture Drive
- As Long As The Wind Blows
- Renold Synergy
- Smaller Models
- ZTRS Precision rack and pinion drives
- Drive Design Can Be Based On Torque Required
- Deck Machinery & Planetary Gearboxes
- Chip Of The Old Nordbloc
- Larger shaft diameters
- Experience proves standard geared motors are the correct option