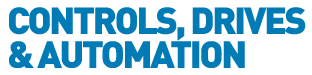
![]() |
Charlotte Stonestreet
Managing Editor |
Home> | DRIVES & MOTORS | >Servo Motors & Drives | >Servo drives help protect castors |
Servo drives help protect castors
06 March 2023
YASKAWA'S SIGMA-7 series servo-drives and a SLIO-series controller have played a key role in the development of an automated system specifically designed to fit protective plastic caps onto office chair castors at Gross+Froelic.

The castors consist of two individual wheels with a protective cap pressed onto each and it’s now a process which can be performed automatically and at considerable speed. Gross+Froelich use a machine made by ARAMIS which can operate with cycle times of just 2.4 seconds, following its re-design using the latest servo technology. Depending on the castor model, it’s now possible to fully apply up to 36,000 protective caps automatically to the castor wheels over 24 hours of operation. This is an increase of around 10,000 caps more than the machine managed, before it’s re-design. So what were the two key factors which helped to achieve shorter cycle times? Firstly the capacity of the rotary indexing table for the plastic caps was increased from four receptacles to eight and secondly, three of the pneumatic drives installed in the machine were replaced with the more dynamic Yaskawa Sigma-7 series electrical servo drives.
It would have been impossible to achieve the higher speeds with pneumatic drives due to the mechanical stresses being excessively high. Furthermore, the levels of compressed air consumption are much lower which has reduced operating costs.
Yaskawa’s Sigma-7 series was the choice for the electric drives having already proven themselves in many similar applications and impressed ARAMIS the machine builder. Features such as rapid commissioning, high production capacity and maximum operational reliability, in addition to the responsiveness of the AC motors, were the key factors for the machine builder. Their extremely compact dimensions and quiet operation were also important.
The machine builder and other key suppliers worked together with Yaskawa’s automation specialists to retrofit the machine for fitting the protective caps. A total of three 400 V servo axes, each with 400 W of power, are now in use in the machine. One drive is responsible for the horizontal movement of the feed while a pneumatic linear unit with a gripper transfers the plastic cap from the separation unit to the nest of the rotary table. An electrical cylinder driven by second servo drive presses the cap against the chair roller, while a compression force sensor detects the surge in force when they engage. Together with the absolute position sensor on the servo motor, it detects whether the pressing process was successful, while a third servo drive controls the horizontal movement. The finished parts are sent down a chute where the wheels, which are now protected by the caps, are transferred to a lattice box so they can be transported for final assembly.
The drives offer high resolution (with an integrated 24-bit absolute encoder) and high dynamics along with vibration suppression, also suppression of machine resonance frequencies and a tuning-less function for simple start-up, all integrated into the compact servo amplifiers.
- Regenerative drives improve energy efficiency
- Yaskawa unveils Signature robot range
- Smaller & more flexible industrial robot
- Yaskawa expands in Europe
- Ensures reliable and accurate part changes
- Speaking the same language
- Up close & personal
- Collaborative robot brings new application possibilities
- Drive gains marine certifications
- Smaller & more flexible industrial robot