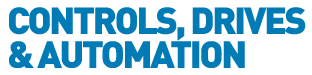
![]() |
Charlotte Stonestreet
Managing Editor |
Home> | MACHINE BUILDING & ENGINEERING | >Machinery Safety | >Minimising machine safety risk |
Minimising machine safety risk
11 October 2023
Darren Hugheston-Roberts looks at the legislation surrounding machine safety

The Supply of Machinery (Safety) Regulations 2008 contain detailed requirements for the design, manufacture and supply of safe new machinery to the UK market, and machinery manufacturers and suppliers must ensure that their product is compliant.
Within the regulations there are Essential Health and Safety Requirements (EHSR) that lay down the minimum conformity criteria. While the use of standards is not mandatory, if a standard is applied correctly conformance with the relevant EHSRs of the regulations may be presumed, they therefore represent the surest way to ensure conformance. However, the end-user must still ensure that the product complies with the regulations and is in fact safe when putting into use for the first time, and remains safe.
The preferred way to comply with EHSRs is by risk assessment and the application of Designated Standards. Risk assessment is therefore a vital step in ensuring compliance and a fundamental starting point for designers of machinery under the Machinery (Safety) Regulations. A risk assessment must therefore be carried out to examine any potential hazards associated with the machinery, this provides information for a risk evaluation, in which a decision is made on the safety of that machinery, so that risks can be reduced where necessary to a reasonably practical level using the hierarchy of risk control.
For machinery owners and those providing machinery for work, the Provision and Use of Work Equipment Regulations 1998 (PUWER) applies to all work equipment regardless of its age, regardless if the equipment carries a CE or UKCA mark, or if it pre-dates this product requirement; It is therefore vital that machinery owners understand their responsibilities.
PUWER describes what an employer needs to do to protect employees in the workplace. It is therefore their responsibility to ensure that all new machinery meets the requirements of The Supply of Machinery (Safety) Regulations 2008 and PUWER 98. Risk assessments are fundamental to any health and safety process and in particular machinery safety. Guidance on carrying out risk assessments can be found in many places. EN ISO 12100 is the main standard for risk assessment for machinery as it sets down the principles for the process. Other guidance can be found within HSG 129, particularly HSE details around ‘key safety measures’ for certain types of workshop machinery.
New machinery
To immediately identify any issues, a thorough and correct risk assessment, and inspection should be completed before any new machinery goes into operation for the first time. Problems can then be rectified with the manufacturer, so that they or the machinery owner no longer runs the risk of a prosecution under the Health and Safety at Work Act 1974, due to noncompliance with the Supply of Machinery (Safety) Regulations or/and PUWER.
Modification
The HSE states that if changes to machinery “are very substantial (e.g. significant new hazards and risks are introduced or new methods of control of the machine replace those previously provided, such as computer control of a previous manual machine) it may amount to being considered a "new" machine (or new assembly), for which you must undertake conformity assessment”.
The HSE goes on to state that even if changes to machinery are not substantial, such as refurbishment, the owner must still ensure that it continues to meet the requirements of PUWER, as well as any other requirements which may also apply to the product.
Risk assessment process
The first step is to identify anything that has the potential to cause harm. Secondly, an assessment must be made of the likelihood of a person coming into contact with these hazards and how much injury it would cause.
Examples of hazards that have the potential to do harm include:
- A manipulating robot
- An automated guided vehicle
- Rotating machinery (lathes, drills, milling machines, etc.)
- A moving conveyor
- A pallet wrapper.
A risk assessment would normally be carried out for each machine; the Preliminary Hazard Analysis (PHA) method uses a Hazard Rating Number system. Referencing a table, the most appropriate phrase that applies to the hazard is chosen, the corresponding score results in a hazard rating number (HRN), which corresponds to the level of risk.
The PHA takes into consideration:
- The likelihood of a person or persons coming into contact with a hazard
- The degree of possible harm that could be caused
- The frequency of exposure
- The number of people at risk at the same time.
Control measures can then be applied to mitigate the risk:
- Design the hazard out
- Remove the need for man-machine interface
- Design-in safeguards
- Reduce the possibility of occurrence
- Reduce the degree of harm
- Warn and inform machine operators (but only if you can achieve adequate safety).
Once the control measures have been implemented, a re-assessment must then be actioned to ensure that they provide an adequate level of safety and to ensure no secondary hazards have been introduced, the process is repeated until an adequate level of safety is achieved.
Consistent compliance
Section 6 of PUWER requires that inspections must be conducted ‘at suitable intervals’ if machines are exposed to conditions that may lead to deterioration. In reality every machine is exposed to conditions that may lead to deterioration, so the requirement effectively means that they must all be regularly inspected at some point. The function of a work equipment risk assessment is to identify those components that could deteriorate and identify how often they should be inspected, how they should be inspected and by whom.
Although, risk assessments must therefore be conducted conscientiously and at appropriate intervals, we still visit sites that simply forget and haven’t taken any action for five years or more.
The answer here is to set up an internal process, overseen by an individual who ensures risk assessments are carried out according to an agreed schedule. Creating an internal procedure in this way successfully integrates risk assessment into the everyday working practices. Taking this simple approach ensures that work equipment risk assessments are swiftly integrated into the everyday working practices of an organisation and are never neglected.
PUWER requires that the persons who determine the nature of the assessments, and carry them out, should be competent to do so. While the exact definition of a competent person is not currently regulated, the HSE definition is: “Someone who has sufficient training and experience or knowledge and other qualities that allow them to assist you properly. The level of competence required will depend on the complexity of the situation and the particular help you need.”
It is a common assumption amongst machinery owners that if their equipment has a CE or UKCA mark then no further action on their part is required to ensure machinery safety. However, it is vital that employers who provide machinery to employees to use understand both their duties and the responsibilities of the machine’s manufacturer, and/or the machines supplier.
The machinery risk assessment process can be complex and once completed, may result in significant changes to the workplace environment. However, the failures we see on site are often due to a lack of appropriate internal expertise or the physical on-site resource to do an in-depth and correct assessment of all machinery. A decision to ‘make do’ or not invest in the appropriate expertise could result in expensive fines, reputational risk or worse still, a fatality to a machinery user or other person on the premises.
Darren Hugheston-Roberts is head of machinery safety at TÜV SÜD
Key Points
- The Provision and Use of Work Equipment Regulations 1998 (PUWER) applies to all work equipment regardless of its age
- Inspections must be conducted ‘at suitable intervals’ if machines are exposed to conditions that may lead to deterioration
- PUWER requires that a competant person determine the nature of the assessments, and carry them out
- Exotec builds 4000th robot
- Motor Driven Systems Conference
- ABB & IBM to bolster cybersecurity for industrial operations
- Cultivating ideas in the digital landscape
- Expanding electrical engineering talent
- Minature pump and control package
- Ask the expert: the fundamentals of motor gearbox selection
- 2024 promising for UK manufacturers looking to automate
- Soft Robotics becomes Oxipital AI
- Siemens UK awarded Cyber Essentials Plus (CE+) certification