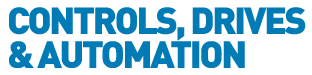
![]() |
Charlotte Stonestreet
Managing Editor |
Home> | IIot & Smart Technology | >Big Data | >Unlocking asset data to meet net zero |
Unlocking asset data to meet net zero
16 October 2023
RS INDUSTRIA, an innovative cloud-based service and part of the RS Group, has helped global food giant Kerry work towards its net zero goals through a modular approach to condition monitoring and asset data analysis, which has led to the firm driving down energy and water consumption, maintaining environmental compliance and achieving significant cost savings.

RS Industria’s ‘start simple, grow smart’ modular solution helps manufacturers liberate, collect and analyse data from legacy assets in real-time, and was employed by taste and nutrition business Kerry to address three key areas of concern: waste water, energy monitoring and boiler efficiency.
The RS Industria team worked with Kerry engineers to design a plant monitoring system to create a single point of asset insight to address the lack of operational visibility that Kerry had of its waste water plant. The plant had been expanded over many years to meet its Tenbury site’s growing demands, and its independently operated patchwork of pumps, meters and control systems made automation difficult. Remotely located treatment tanks also made mandatory daily meter readings and condition monitoring challenging.
RS Industria connected the legacy meters and pump control systems to its web platform to give greater visibility and real-time monitoring of key parameters like effluent quality and pH and COD levels, to meet environmental compliance. Daily plant performance can be viewed on the compliance dashboard on the Industria network, and a real-time alerts system via SMS and email lets engineers know if chemicals need correcting.
Tangible benefits of the waste water project include the saving of 100,000 litres of fresh water per day, and associated disposal costs. As a direct result of the insight, Kerry’s team carried out immediate improvement activities to reduce freshwater consumption and put in place better effluent treatment control. Valuable engineer time has been increased due to the removal of time-consuming, manual practices, which can be a real source of team frustration. This has all been replaced with digital insight.
Ben Botwright, engineering manager for Kerry, said: “Our effluent plant is fundamental to the continued operation of the site. However, the plant is ageing and there was limited control and automation, as investment has been tight in recent years. The data that RS Industria has helped us to access has enabled us to significantly reduce the amount of water being used to dilute high-strength or out-of-consent effluent, as we have been able to investigate where the spikes are coming from and stop them at the source. Effluent issues have since gone from being our biggest headache to one of the site’s best performers.”
In addition to the waste water issues, Kerry Group’s commitment to achieving Net Zero before 2050 and an emissions reduction across its operations by 2030 meant the Tenbury Wells site was challenged to make meaningful energy savings. But with little insight into how and where energy was being used, energy efficiency projects were difficult to implement.
RS Industria helped the Kerry team to understand how and where energy was being used on-site, and how consumption could be reduced without affecting production volumes. By connecting the existing sub-meters and installing new ones in other key locations and production lines, consumption data from them was collated on a network to provide a clear picture of where energy was being used in real-time.
By breaking down energy consumption by asset, process, location, and time, detailed insight revealed high areas of waste that could be immediately rectified, such as equipment left on standby over weekends or when not in use. Moving maintenance work to weekday night shifts to reduce consumption of heat and lighting at weekends significantly reduced energy consumption and generated more savings than the cost of the nightshift labour.
The availability of data on energy usage of individual lines, and the insight into site-wide consumption, has created an energy-saving culture among staff who have since made further changes to operating procedures to maximise energy savings. The result was a 14% reduction in energy usage within weeks – around 60t of CO2 per year – representing a huge step toward corporate sustainability goals.
The efficiency of the firm’s two boilers was also a concern: there was limited understanding of system efficiency as it had no integrated instrumentation, and no steam output metering, only bulk metering of fuel oil consumption. RS Industria used data to review the steam demand of the system and changed it from continuous to an on/off feed control, further reducing electricity consumption for duty and standby boilers as a result. So far, the reduction in usage is around 75%, equating to a £12,000 per year cost saving and 11,000 tonnes of CO2 negated. The duty boiler is also now more reliable because of the condition monitoring implemented.
Botwright added: “The RS Industria platform has enabled us to connect all of our existing meters – and additional new ones – relatively easily, and very quickly, we were able to get a comprehensive view of how we’re using our electricity by hour, by minute, by second, across the site. Having data to be able to influence behaviours and make improvements is fantastic, and the benefit of the Industria system is that you can see the impact of any changes very quickly.
“Often, we’ve had to respond very reactively to issues, which resulted in downtime, out-of-specification results, and huge frustration within the team. Real-time data reinforces new behaviours and enables a step-change in how we work and operate, giving us instant improvements. With RS Industria by our side we’ve built a really strong foundation, and I know that they’re a team I can depend on as we move forward, develop, and roll out the solution to different environments on site,” he concluded.
Richard Jeffers, MD of RS Industria, said: “The work we have done with Kerry clearly demonstrates the case for a modular approach which allows you to start with one asset, and then continue to build once results emerge. The fast results not only prove excellent ROI but help foster an organisation-wide culture to use data to problem solve, and stakeholder buy-in to assist future capital expenditure.
“Monitoring one asset at a time allows customers to demonstrate savings before asking for more budget, and once the data is accessible, the RS Industria solution allows you to pull data for any factory asset,” he added.
- Desktop 3D printer
- Supporting open source digital design
- Visitor experience showcases cutting edge technology
- Connected approach
- Microcontrollers & development kits for IoT
- RS joins 5% Club
- A celebration for the inspired
- DesignSpark Mechanical
- AM goes mainstream
- RS releases 2024 Maintenance Engineering Report
- Secure data handling
- Trelleborg joins Smart Data Innovation Lab
- Scalable analytics for IIoT
- Maintenance sector digitalisation
- ROI as a goal in the smart factory
- Intelligence-driven analytics
- Boulting joins MindSphere
- TDC gateway system
- Cutting edge i4.0 Cloud data analytics
- Virtual Engineering Centre awarded nuclear research contract