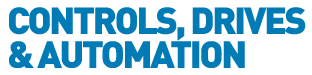
![]() |
Charlotte Stonestreet
Managing Editor |
Home> | POWER TRANSMISSION | >Belts | >V-BELTS SAVE ENERGY & REDUCE MAINTENANCE |
V-BELTS SAVE ENERGY & REDUCE MAINTENANCE
26 September 2012
When drive belts on a waste to energy plant’s ACC (air cooling condenser) fan units were breaking down every four to six weeks

Optibelt was asked to investigate. The problem was identified as premature belt wear caused by pulley misalignment and incorrect belt tension, which was difficult to rectify due to the flexible steel framework on which the drives were mounted and a continuously vibrating environment. To solve the problem, Optibelt recommended converting all three fan unit’s current (timing belt) drives, to Optibelt Vbelts that are proven to be far more forgiving of misalignment.
It was decided that Optiblet Red Power Kraftbands would be fitted, which are not only highly energy efficient and longer wearing, but are also maintenance-free, something that appealed strongly to the plant engineers due to both the significant downtime and health and safety implications of performing belt maintenance on fan units positioned 40ft in the air.
The conversion programme, which was carried out during a planned shut-down, has not only prevented a very expensive and intricate ‘direct drive plant conversion’ job on all three fans, but also reduced the new belt drive running figures, offering a 15% reduction in the current drawn by the motor – a considerable energy saving.