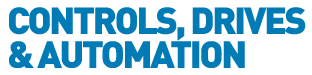
![]() |
Charlotte Stonestreet
Managing Editor |
Home> | POWER TRANSMISSION | >Belts | >SECRETS OF THE DRIVE BELT |
SECRETS OF THE DRIVE BELT
06 November 2012
Phil Burge, communication manager for SKF, outlines the common causes of drive inefficiency and reveals the innovations in modern drive belt technology that are overcoming these obstacles.
Many industrial drive units are required to provide reliable service day after day, sometimes around the clock, and often in contaminated environments. Facing such challenges as these, you could be forgiven for thinking that regular belt failure and replacement is an unavoidable fact of life in the engineering industry but the truth is that drive belts of all varieties have been significantly enhanced over recent years, and these advancements in belt technology can not only maximise efficiency but also significantly cut maintenance costs.
To achieve these advancements, the beneficial properties of several different materials have been carefully considered, selected and successfully applied, in tandem with enhanced component design.
As a result, failures caused by such common issues as incorrect fitting, tensioning and pulley alignment can be significantly minimised.
MATERIALS & DESIGN
A look at recent developments in the construction of the V belt, or wedge belt, illustrates how improvements in the materials and component design employed in the construction of belts can overcome common causes of failure and inefficiency. For example, the problems of elongation and incorrect tensioning have been addressed by belts with exception - ally strong polyester-coated internal tension members. Similarly, pulley groove wear has been reduced by the addition of abrasion-resistant cover fabric, which helps protect belts from friction heat if they slip out of position. Pulley groove wear occurs when a slipped V belt heats, hardens and wears the pulley groove into a U shape; a replacement V belt cannot transmit power effectively because there is now little contact between the Vshaped belt and the U-shaped pulley, and this leads to premature replacements of both components.
MULTI-LAYER
However, there are now belts available that can resist the elongation and friction heat that results in pulley groove wear. SKF Xtra Power wedge belts feature a multi-layer construction, with a tough polyester tension cord being embedded between layers of polychloroprene over a rubber base, and encapsulated in a longlife fabric coating. This advanced construction enables the belt to accommodate heavy tension loads with minimal elongation, resulting in the delivery of up to 40% more power than traditional standard wrapped belts, with an energy efficiency capability of up to 97% and increased operating life. When Belgian zinc recycler Rezinal discovered that the belts needed to drive the fans in the plant were being replaced approximately every two months, we specified SKF Xtra Power Belts, which offered a lifespan more than ten times that of the previous component to deliver two years’ service. The upgrade cut both environmental waste and plant costs, while Rezinal enjoyed the additional benefits of increased performance, reliability, safety and efficiency.
THE BENEFICIAL PROPERTIES OF SEVERAL DIFFERENT MATERIALS HAVE BEEN
APPLIED IN TANDEM WITH ENHANCED COMPONENT DESIGN
Developments in timing belts, or synchronous belts, have also been extremely beneficial when it comes to enhancing efficiency and minimising maintenance. Timing belts can deliver even greater levels of efficiency than V belts and are now available in highly resilient polyurethane with steel cords.
These examples offer just some of the reasons why it pays to review the performance of your belts.
Rather than writing off regular belt replacement costs as a necessary evil, you could make some significant savings.
Key Points
• Drive belts of all varieties have been significantly enhanced over recent years
• Failures caused by common issues such as incorrect fitting, tensioning and pulley alignment can be significantly minimised
• There are belts available that can resist the elongation and friction heat that results in pulley groove wear
- Automation changes the face of maintenance
- SKF's 1000th S2M put into operation
- Seamless engineering
- Tool to help address carbon emissions
- When the going gets tough
- Bearing analysis streamlined
- SKF joins Mission 0
- Maximising marine efficiency
- Bearing rating life model
- From bearing management to the big picture
- V-BELTS SAVE ENERGY & REDUCE MAINTENANCE
- Environmentally Friendly High Performance V-Belt
- NO RE-TENSIONING REQUIRED
- Low Elongation
- Optimise Drive Power & Efficiency
- Complete drive systems
- Brammer awarded Tata Steel Europe contractor of the year
- V-Belts – spoilt for choice
- HPC V-belts
- Belt drive agreement