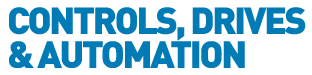
![]() |
Charlotte Stonestreet
Managing Editor |
Modern approaches to industrial maintenance
09 October 2018
As part of the Smarter Futures' focus on Maintec, Andy Pye looks at how some leading industries are adjusting their maintenance regimes to improve effectiveness and take advantage of state-of-the-art techniques
Traditionally, maintenance has been done on a fixed schedule, replacing items at constant intervals. Although the intervals are usually based on established knowledge, that is only part of the story - as we all know, parts wear out at different rates for all kinds of reasons. Constant intervals do not take into consideration the unique and varying circumstances of a machine being maintained. So although general purpose schedules are easy to manage by arranging for spares to be delivered in a predictable manner, they risk wasting money by replacing parts that are still operational.
On the other hand, predictive maintenance is about getting the most life out of equipment while minimising the risk of failure. It ensures that parts are used to the end of their natural life, but risks downtime due to delays in delivery of replacements or additional costs due to higher stock levels. The ideal combination is predictive maintenance with just-in-time supply chains.
Instruments for condition monitoring will look for variances in acoustics, vibrations, thermal output, motor current signatures and other areas, which help determine maintenance schedules and reactive steps needed to keep machinery running optimally.
Video use is also accelerating in data collection. Video cameras are already used in many test and measurement applications throughout industry. “There is no longer any question that recording video data in parallel to tactile sensors or digital bus signals is becoming more and more attractive to users," says Christof Salcher, Product Manager Instrumentation at HBM. "Video supports traditional sensor data and is becoming a valuable source of additional information, making the room for interpretation even narrower in testing.”
Using wireless condition monitoring in the rail sector
The rail industry’s prevailing maintenance regime is to service trains on a time or mileage basis. Though it has been used successfully for many years, it does not take account of whether parts do actually need replacing. Nor is it effective at preventing breakdowns.
The railway sector has been slow to adopt condition-based monitoring (CBM) – due in part to a number of safety regulations that govern it, but also because suitable technology has not been available.
SKF has developed a wireless CBM system – SKF Insight – that consists of retrofitting a small sensor onto the wheelset axle-box assembly of the train, to detect bearing damage. The sensor picks up tiny inconsistencies in the vibration of a bearing as it begins to fail – despite it being in an environment wracked by noise and other vibrations. Sophisticated signal processing and algorithms separate the signal from the noise, ensuring that each sensor produces accurate data for further analysis.
Each of the wireless sensor nodes has an array of different sensors included and can take several different measurements pertaining to bearing health. Acceleration Enveloping is a long-established vibration measurement which is proven to give early indications of bearing damage. A standard acceleration vibration measurement is band-pass filtered rectified and finally enveloped. Advanced processing and trending of the resulting signal is then performed using software. It is possible not just to detect the presence of damage but also to determine what bearing component is damaged. The inclusion of the temperature data is complimentary to the vibration data. The whole system uses wireless reporting.
Collecting and sending the data is one thing – but acting on it is something else. Rail operators do not want to plough through mountains of data and interpret it. Instead, they want clear recommendations for action. So an automatic alarm will trigger whether action is needed. Experts then check the output and produce a report – such as recommending a planned replacement of the bearing.
What does maintenance mean for aerospace
Aircraft maintenance is highly regulated, because the smallest slip can have dire consequences. The maintenance personnel must be licensed for the tasks they carry out. The International Civil Aviation Organization (ICAO) sets global standards which are then implemented by national and regional bodies around the world. Maintenance includes tasks such as ensuring compliance with Airworthiness Directives or Service Bulletins.
Automated aircraft inspection systems have the potential to make aircraft maintenance safer and more reliable, using collaborative mobile robots and unmanned aerial vehicles. Airbus has indicated that data diagnostics could put an end to aircraft unscheduled grounding for fault repairs around 2025, supported by big data and operational experience. In principle, the approach can tell that some parts do not need a scheduled check, but a full transition to this model will need much greater experience.
According to Geoff Turner, business consultant at product lifecycle management (PLM) company Design Rule, the use of VR throughout the aerospace manufacturing sector can also save millions in development costs by eliminating the need for full-scale prototypes.
By designing aircraft in virtual space, designers can explore a virtual mock-up of the entire aircraft and can work to eliminate issues faster than normal. For example, should a vital gauge or access point be blocked by panelling, it can be easily adapted in a VR design in a space of hours, instead of taking weeks with prototyping and testing processes.
It’s not just the maintenance and engineering elements of the aircraft that are being designed in virtual spaces. According to Airbus engineer, Dieter Kasch, "You can install a seat, calibrate it with the interiors theme, and then sit in the aisle or window seat and see different views of your cabin from these varying positions. Changes at a late stage cost time and money, so it helps us deliver our aircraft on time and on budget.”
Keep making the tablets
German connector manufacturer Harting recently challenged postgraduate students from the Centre for Doctoral Training in Embedded Intelligence at Loughborough University to investigate practical application solutions where MICA - the company’s open platform based ruggedised industrial edge computing device - could be applied to the benefit of UK manufacturing.
One such proposal was suggested for pharmaceutical companies manufacturing tablets using automated presses and punch tools.
Data from these machines can be collected using passive UHF RFID “on metal” transponders which can be retrofitted to existing tablet press machines and mounted on the actual press-die/punch tools. The RFID read and write tags can record the pressing process - the number of operations performed by a press die, plus any other critical operating sensor-monitored conditions. The system can then review that data against expected normal end-of-life projected limits set for that die.
Such data can be managed and processed through MICA, which can then automatically alert the machine operator that maintenance needs to take place to replace a die-set before it creates a catastrophic tool failure condition and breakdown in the production line - which unfortunately is still quite a common occurrence.
MICA is easy to use, with a touch-optimised interface for end users and administrators implemented entirely in HTML5 and JavaScript. It provides an open system software environment that allows developers from both the production and IT worlds to quickly implement and customise projects without any special tools.
- Future technologies receive government cash boost
- Expanding electrical engineering talent
- Wind sector O&M costs fall with Covid-19 induced work practices
- Cyber threats to industrial control systems
- Training robots to solve problems like a human
- Unlocking smarter manufacturing
- Paving the way to the integrated smart factory
- Western Business Exhibitions adds Maintec & Facilities Management events to portfolio
- Emerson roadshow hits the UK
- Demand going sky-high
- No related articles listed