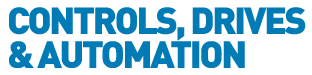
![]() |
Charlotte Stonestreet
Managing Editor |
Getting started with smart devices
21 October 2019
The conversation of introducing Industry 4.0 and IIoT, from smart devices up to AI in the factory floor is gaining momentum. Even more so with the volume of accessible amounts of data, along with increased computing power. Smart sensors with IoT features have further accelerated implementation plans
Manufacturing companies are continually seeking ways to increase overall equipment effectiveness (OEE). The combination of smart sensors and machine controllers equipped, with adaptive algorithms, has offered enormous potential. This has led to further developments such as predictive maintenance and efficient production, that are necessary within the framework of Industry 4.0. This again has led manufacturing companies to not only understand the opportunities to increase overall equipment effectiveness (OEE), but to also reduce costs and increase productivity.
Gartner predicts that by 2022, more than 80% of enterprise IoT projects will include an AI component, up from only 10% today. The Internet of Things is all about connected devices responding to circumstances based on the data that they collect. After all, without an efficient way to interpret the data and to define actions, the sensors are just collecting information that can’t be used.
When implementing smart sensors for IIoT or Industry 4.0, many manufacturers face a situation where they are restricted by their existing infrastructure of legacy machinery and plant, lacking standardisation of system architecture. So, defining a process or starting point for implementation can be challenging. Here are 5 tips to help you get started.
1. Understand and outline the problems needing to be solved
One of the biggest challenges that manufacturers face is that they don’t know what problem they want to solve. But how can you define the problem without data? The solution is to start collecting and cleaning data first. You can then start obtaining information from the data, visualise it and see where the areas of improvement are.
2. Explore the optimum uses of your data
The machines within a factory are a potential source of valuable data. But how can users access and analyse the data that a machine could provide? How can a manufacturing plant then make the most effective possible use of this data? Ask yourself, do I have enough data, and which data is the most relevant and how will it be used? And how much will the infrastructure cost?
3. The implementation of systems to monitor machinery or plant effectiveness
One of the first steps we recommend to manufacturers that are beginning their Industry 4.0 journey, is to deploy a system that enables them to monitor machinery or plant effectiveness. These types of solutions can be used to monitor productivity and downtime. Whilst being relatively simple and cost effective to deploy, systems like these provide valuable line level information, and permit more informed decisions about possible areas of additional investment.
4. Reliable and instantaneous communication between devices
Getting the right data from the 'grass-root' level of the manufacturing process is essential when creating the factory of the future. Real-time communication to and from field level devices, for example, open vendor protocols like IO-Link, allows sensors and actuators to exchange data with the machine controller. Bidirectional communication is established so parameters can be transferred from the controller to the devices and the status can be read. Sensors and actuators can communicate more than simple on/off signals or analogue ranges. They can provide advanced status and diagnostics information communicating with the controller about how they are performing. Furthermore, the controller can also change the sensor’s parameters, creating the ultimate in flexible manufacturing.
5. Utilising the full potential of your smart sensors and the wonders of AI
It is of prime importance that instantaneous communication is set up between devices. Once this is established, devices in the field can be examined and modified before leading to a line stoppage, due to an unforeseen complication. For example, if a photoelectric sensor’s lens is building up dirt, the sensor can trigger an alarm via IO-Link and alert the operator to clean it before the sensor stops working. By continually monitoring each sensor, corrective actions can be taken before the device malfunctions. In addition, corrective action can also be planned for quiet periods to minimise their impact on productivity.
AI at the Edge allows companies to gather data, analyse it and react in real-time, this is another option for predictive maintenance. In this approach, the machine is collecting all the data. Although the scope of the data remains relatively large, organizations need less resources in terms of hardware, communication infrastructure or processing capabilities at enterprise levels.
- OMRON adds EtherCAT models to i4L SCARA robot series
- Feature Rich & Cost Effective
- Connect with confidence
- Heavy payload cobot
- Sensing where safety is paramount
- Extreme temperatures no problem for new power supplies
- Machine cell control
- Complete solution for IO-Link
- Omron's solutions support TheOpenVentilator
- Mobile robot fleet management software
- No related articles listed