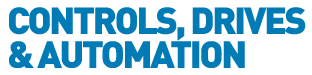
![]() |
Charlotte Stonestreet
Managing Editor |
Home> | AUTOMATION | >Encoders | >Greater Flexibility In Heavy-Duty Applications |
Greater Flexibility In Heavy-Duty Applications
17 January 2013
Providing a viable economic alternative when it comes to large diameter shafts, rotary encoders featuring magnetic measuring principles can function in very little space and can be used in heavy industry areas where the lifespan of optical rotary encoders is limited – despite elaborate protective casing
Rotary encoders are very often used for measuring changes in angles on rotating shafts. A distinction is often made in the field between incremental encoders (investigating rotational speed and direction) and absolute value encoders (determining absolute position).
Optical (photoelectric) scanning is the most widely used measuring principle. A light beam generated by a light source (mostly an infrared ICD) is directed through a(n) (optical) condenser, a grating (material measure) and an aperture (scanning reticle) as well as onto a photo-optical component (generally a photodiode). The light beam is periodically modulated from a LED to a sensor and back again through the rotation of the plate marked by slits. During this process, the sensor generates a sinus-shaped electrical signal.
Casing designs commonly required for optical rotational encoders narrow the range of mounting options
In addition to the photoelectric measuring principle just described, magnetic encoding technology has gained in significance in recent years. Here, the material measure is made up of a hard magnetic carrier (inductor) with an in-built magnetic partition (north/south pole), which is kept protected from external influences. A separate scanning head contains the requisite sensory and electrical technology.
The magnetic encoder’s sensory technology
Different types of sensors are used, depending on the type of measurement and the encoder performance e.g.
- AMR sensors: react to changes in the direction of the magnetic field caused by small fluctuations in electrical resistance ågenerated by a conductor under the influence of a magnetic field. British physicist William Thomson (Baron Kelvin) discovered ordinary magneto resistance in 1867. Today, the principle is used a million times over in hard disks’ read-and-write heads.
- GMR sensors likewise react to changes in the direction of the magnetic field where fluctuations in the electrical conductor’s resistance levels are higher than 50 percent. This secures the sensor’s further application in automotive and automation technology. German physicist Peter Grünberg from the Forschungszentrum Jülich (Jülich Research Centre) discovered giant magneto resistance in 1988.
- Hall sensors react to changes in the strength of magnetic fields. American physicist Edwin Hall discovered the Hall Effect in 1879. The sensors are also put to use in automotive and automation technology.
Encoders using optical measuring processes have been successfully used for decades in numerous devices and automation procedures. They are distinguished by, amongst other factors, their signal’s high degree of precision and the high resolution they can achieve. Incremental rotary encoders with one million impulses per rotation are used for specific measuring purposes, such as stone detection for bucketwheel excavators engaged in coal production. Their purpose is to detect the smallest changes in rotational speed and to switch off the device.
Environmental influences
However, the optical measuring principle is essentially vulnerable to environmental influences such as shock and vibration, grime, temperature shifts and condensation. These weaknesses can be addressed through specifically designed casing. This is shown inter alia by the several thousand optical rotational encoders made by Johannes Huebner Giessen’s that are in use around the world at heavy industrial sites such as steel and rolling mills or in mining devices plus as part of crane and port technology.
That being said, the casing designs commonly required for optical rotational encoders narrow the range of mounting options. Ideally, one end of the shaft is free for attachment to the encoder: either by means of a coupling (solid shaft devices) or by direct placement onto a hollow shaft or an appropriate adaptor shaft (if that is being used). The cost of the encoder’s casing and of the obligatory ball bearings accompanying it increases disproportionately to the overall increase in the size of the shaft diameter. This means that if the shaft diameter is greater than 200 mm, scarcely any economically feasible solutions remain.
Greater design freedom
As a result, rotational encoders with magnetic measuring principles (magnetic encoders) represent an intriguing alternative. Fundamental progress in magnetic sensory technology has broadened this technology’s range of functions in recent years.
Thanks to their lack of vulnerability to shock, vibration, grime, temperatures fluctuations and condensation, magnetic encoders can be put to particularly good use at those sites in heavy industry where, despite costly protective casing, the lifespan of optical encoders is limited (figure three). The magnetic partition of the inductor attached to the rotating shaft is adequately protected by means of a special bandage. All electronic components are incorporated into a scanner head with a high level of protection. If necessary, they can be completely grouted into place. Thanks to the two-part system set up featuring inductor and scanner head, the magnetic encoder can be mounted without resorting to expensive protective casing and additional ball bearings. This represents a practically wear-free solution with an exceptionally long lifespan.
Incremental rotary encoders with one million impulses per rotation are used for specific measuring purposes
Potentially foregoing protective casing and ball bearings leads to a marked increase in the amount of freedom available to designers of magnetic encoder systems. Therefore, it becomes possible to design a variety of different models, each of them optimized to match the required uses the customer wants to put them to.
In addition to its standard system featuring an undivided inductor, Johannes Huebner Giessen has recently developed and will patent an innovative solution featuring a divided inductor. The two halves can be mounted directly onto the installation point in a radial direction. No unattached shaft end is required. This means that the magnetic induction system featuring a divided inductor (MAG-G) is ideally suited for retrofits and upgrades.
Depending on the design constraints, customers can choose from various mounting procedures for the inductors, including assemblage with screws, heat shrinkage, clamping plate or via tolerance sleeves. Sinus-shaped signals, incremental signals and absolute value signals (SSI, EtherCat, other bus interfaces) are among the electrical output signals available for those selecting Johannes Huebner magnetic encoding systems.
Magnetic rotational encoding technology can be seen at work in steel mills on measuring rolls, cylinder and tandem actuators, ship propellers, gas and water turbines (ATEX certified) as well as in pumped storage hydroelectric plants and on mega excavators used for open-cut mining, conveyor belt systems and oil derricks.
Key Points
- Rotary encoders are very often used for measuring changes in angles on rotating shafts.
- In addition to the photoelectric measuring principle, magnetic encoding technology has gained in significance in recent years.
- The optical measuring principle is less vulnerable to environmental influences such as shock and vibration, grime and temperature shifts
- REGULATE FLOW
- Laser Distance Measurement
- ACCURATE 2D & BARCODING
- Heidenhain Ltd
- Angle Encoder Range Widened
- Multi-turn absolute encoder with EtherCAT
- Absolute encoder now more robust
- Encoder challenges rotary order
- True-absolute optical encoder
- TR-Electronic presents SIL3-/PLe-Certified absolute rotary encoders – now available on ProfiNET