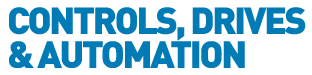
![]() |
Charlotte Stonestreet
Managing Editor |
Home> | AUTOMATION | >Encoders | >Encoder challenges rotary order |
Encoder challenges rotary order
03 July 2013
Turck has unveiled a contactless encoder in which almost every part of a traditional rotary encoder has been replaced with state-of-the-art, fully encapsulated electronics. Importantly there are no moving parts inside the encoder.
In the Turck RI-QR24 contactless encoder, there is – as the name implies - no contact between the passive positioning element fixed to the rotating machine shaft and the encoder. The device utilises a 32 bit microprocessor, is sealed to IP69K and has over 18 bit resolution.
In eliminating the moving parts within the encoder, one of the major problems for the encoder stockist is also eliminated: a traditional encoder has a glass or plastic disc printed with a pattern of transparent and opaque areas. Every variant of encoder resolution, output type etc., requires a different disc. Manufacturers have warehouses full of these different discs, yet relatively few fully assembled and finished products, simply because the economics don’t allow it. The majority of orders have to be built to order, thereby extending delivery times.
Conversely, this new encoder has no disc, and most parameters are programmable, resulting in very low requirements for stock or spares.
Fully potted electronics
The device is based on an inductive resonance coupling circuit, utilising emitter and receiver coils manufactured as printed circuit boards with exceptional precision. The resonant circuit measuring principle makes it possible to design a fully potted sensor housing without seals, separate from the positioning element. This therefore fully excludes dust or water penetrating into the electronics. The contactless measuring principle of the encoder enables it to compensate for vibration and offset up to 4mm.
Magnetic fields cannot anyway disturb the measuring process since the positioning element is not based on a magnet but on an inductive coil system, through which the sensor and the positioning element (resonator) can form an oscillation circuit.
Electronics and coil geometry
The geometry of the receiver coils is designed so that different voltages are induced in the coils depending on the position of the positioning element, and thus determine the sensor signal supplied. The sensor is provided with a low-precision and a high-precision receiver coil system in order to increase its flexibility and measuring speed. The low-precision receiver coil system locates the positioning element firstly with less accuracy, whilst the high-precision system carries out the fine position measuring.
A special coil arrangement ensures that a stable resonance coupling is implemented in a defined distance range, and that the sensor signal does not change if there is any lateral movement or a change in distance. The signals are evaluated in the internal 32-bit processor and are presented at the output with an exceptionally high resolution.
The electronics are implemented on two board levels: the PCB on which the sensor element is positioned is located directly under the active face; the electronic circuit for the signal evaluation on the other hand, is housed one level below it.
The housing of the inductive encoder is made of metal, with plastic on the active face. The sensor can be mounted easily from both sides. The positioning element is adapted to the shaft in place by means of a shaft ring supplied. This is available in various diameters from 6 to 20 mm, and 1/8in and 3/8in. The positioning element can also be screwed frontally to the shaft and then covered with the supplied blanking plug.
Accessories for fieldbus connections
The encoders are often required to be connected directly to the fieldbus that communicates with the higher-level controller. This enables the position feedback signals of the sensor to be transferred directly to the fieldbus system (eg to PROFIBUS-DP, DeviceNet, CANopen or to Ethernet-based protocols) - this consequently eliminates the need for analog input modules. If the remote I/O systems are too large, Turck's space saving Piconet fieldbus system and BLcompact systems can be deployed with highly rugged modules for direct field installation.- Flexibility for dry contact applications
- RFID solution as a service
- Visual factory comes into focus
- Immune to magnetic fields
- LED or Laser? Choosing a photosensor
- Pick-to-light technology
- Distributor turns manufacturer
- Centralised or decentralised Automation?
- Control on a roll!
- Sustainability and savings go hand in hand
- REGULATE FLOW
- Laser Distance Measurement
- ACCURATE 2D & BARCODING
- Greater Flexibility In Heavy-Duty Applications
- Heidenhain Ltd
- Angle Encoder Range Widened
- Multi-turn absolute encoder with EtherCAT
- Absolute encoder now more robust
- True-absolute optical encoder
- TR-Electronic presents SIL3-/PLe-Certified absolute rotary encoders – now available on ProfiNET