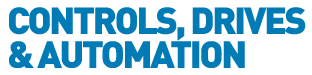
![]() |
Charlotte Stonestreet
Managing Editor |
Home> | AUTOMATION | >Networks | >Automation In The Utilities - Not Big Data, But Better Information |
Home> | INDUSTRY FOCUSES | >Water | >Automation In The Utilities - Not Big Data, But Better Information |
MORE FROM THIS COMPANY
- Are you ready for the changes to EU Authorised Representatives?
- Out-of-the-box robotic sanding tool
- All-new mobile browser with complete data encryption
- AMR wireless charging system voted Industrial Production Product of the Year
- Call to action to upskill on offshore wind robotics
- AMR revolution in cold chain logistics
- UK manufacturers turn to automation to boost domestic capacity amid trade uncertainty
- Survey shows net zero skills gap
- High-performance integrated motion control
- ABB & IBM to bolster cybersecurity for industrial operations
RELATED ARTICLES
- ONE-WIRE DIGITAL AV NETWORK
- Now With Digital Interface
- CC-LINK STARTER KITS
- FOOD & BEVERAGE ACCOLADE
- TOP-LEVEL SECURITY
- Networking Options Extended
- ARE YOU READY FOR…THE INTERNET OF THINGS?
- Community Growth
- Yokogawa joins Friends of the Supergrid
- BACnet support for building services applications as standard
OTHER ARTICLES IN THIS SECTION