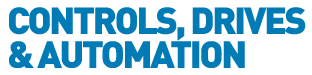
![]() |
Charlotte Stonestreet
Managing Editor |
Taking control of the daily grind
30 April 2013
Featuring complete integration of machine functions, an Omron-based control system is helping machine tool company Halifax Numerical Controls (HNC) to build roll grinders for rubber-coated rollers
Rubber-coated rollers are used extensively in the printing and coating industries and must be accurately ground with a profile to suit their ultimate application. For some applications, the profiles are parallel, but for the majority a precise convex or concave profile is needed. Designing a machine that will consistently and accurately grind these profiles is no easy task, especially when end users typically expect the machines to handle rollers up to 5m long, 600mm in diameter and weighing up to a quarter of a tonne.
When Halifax Numerical Controls started development on its new RG300 machine, engineers concluded that using a CNC system may not offer the most flexible and customisable platform for their machine. They needed to easily tailor the control system to suit the specific application. They set about designing a radically new, fully customisable control system. Omron could supply all of the major control items needed, including Ethernet connectivity to third-party equipment.
The control for the new RG300 roll grinder includes a four-axis machine controller, of which only two axes are currently used; two 600W servo axes with absolute encoders; two inverter drives, one for the workhead drive, the other for the grinding wheel drive; a colour touchscreen operator interface panel (HMI); a safety relay and a safety locking switch. All of these components are from the Omron range, and all of the major items are linked by EtherCAT, an Ethernet-based networking system specifically developed for use in high speed, real time control applications.
Simplified wiring
Using EtherCAT in this project delivered several important advantages. For example, the control wiring was greatly simplified. This cut wiring time, saved space in the control panel and greatly reduced the risk of wiring errors, which meant that testing and commissioning were faster and easier.
In addition, the EtherCAT network allows direct access to the key operating parameters for all of the inverters and servo drives, which means that they can all be set up and controlled from the HMI panel. In fact, the HMI panel can also be accessed via the network, allowing the operation of the machine to be visualised remotely using the in-built web browser functionality of the HMI.
Using EtherCAT in this project delivered several important advantages
The Ethernet support offered by the Omron NJ machine automation controller made it possible to connect a third-party wheel balancer direct to the control system via the controller’s built-in Ethernet/IP port. As a result, the wheel balancer can be monitored and controlled from the machine’s main HMI panel, eliminating a separate user interface.
The NJ301 machine controller used in the project also features a fast, powerful Intel processor, and full advantage was taken of this by using it to run specially written algorithms for calculating the cam profiles needed for specific types of roller. Whereas the calculations had previously taken as long as ten seconds for each profile, the NJ301 controller executes them almost instantaneously.
For configuring and programming the control system, HNC made extensive use of Omron’s Sysmac Studio Integrated Motion and Logic programming platform, for developing complex control programs. With the new control system, profiles for each type of roller are prepared off-line, and are loaded into the control system with the aid of a standard SD memory card. The operator then simply chooses the required recipe via a hand-held barcode scanner. The selected product is confirmed on the HMI’s display, and the control system does the rest. This arrangement is very straightforward, which means the risk of costly errors is almost eliminated, and it also requires no CNC experience on the part of the operator.
In addition, the graphical display minimises the amount of text used in the operator interface, making it readily adaptable to international markets. HNC has programmed the interface so that the small amount of text it was essential to use can be displayed in any one of 16 languages, with instant switching between languages. In addition, the operator interface can be easily and inexpensively customised to suit specific user requirements.
Key Points
- Control for the new RG300 roll grinder includes a four-axis machine controller
- The EtherCAT network allows direct access to the key operating parameters for all of the inverters and servo drives
- The NJ301 machine controller used in the project features a fast, powerful Intel processor
- Food for thought
- High speed vision
- OMRON in Top 100 Global Innovators
- OMRON's new M1 inverter transforms tile manufacturing
- Sensing where safety is paramount
- Condition monitoring devices
- Omron's solutions support TheOpenVentilator
- Pressure sensors for industrial control and safety applications
- Compact push buttons
- Seamless Integration
- No related articles listed