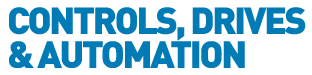
![]() |
Charlotte Stonestreet
Managing Editor |
Industry Associations
Automation: plan to succeed
11 November 2013
The decision to opt for any form of automated handling solution requires careful analysis and detailed planning. Dave Berridge, Secretary of the Automated Material Handling Systems Association (AMHSA), presents a 12-point plan to a successful project.
In this era of fast-paced market change and general globalisation, there is no doubt that all industrial sectors are having to face up to the challenges of controlling inventory, optimising material movements and eliminating errors in the supply chain. Companies can generate crucial competitive advantage by knowing what goods can be produced and delivered – when, where, how many, of which quality and at what cost. The economic problems that have gripped the world in recent years have made the pursuit of efficiency not merely important but critical.
Trends such as SKU proliferation, multi-format retailing, the need for store-friendly deliveries, the increasing cost of transport, the demand for greater traceability and a focus on health and safety have helped to strengthen the case for automation in the warehouse. But, if the benefits of logistics automation are to be realised, the process of designing and implementing an automated material handling system requires careful management at every stage. The process can be broken down into four distinct phases – the material handling study; outline design and specification; project implementation; and support services.
Phase one – the material handling study – consists of planning and analysis, at the end of which you should be in a position to make a decision on whether to proceed with the automation project. The key advice here is:
1 Plan early…start planning as early as possible for automation projects. This allows you to time to consider growth, service and staff levels in detail. Procrastination over planning due to fear of technology, high capital costs, change of culture or possible service level reductions will only serve to aggravate the situation later on.
2 Prioritise…having defined a business need to automate, your system priorities must be set in terms of the three key factors of cost, quality and flexibility.
3 Analyse data…you will need to provide a comprehensive analysis of relevant data, with verification sessions at intervals during the design and implementation process, as well as at intervals after the system has gone live.
Phase two – the outline design and specification – may or may not be executed by the same company that undertook phase one. On completion of this phase, you will be have a good understanding of the proposed solution, as well as the expected total cost of the project.
4 Allow for growth…agree and document the expected growth factor that will influence the design throughout the system’s life.
5 Understand functionality…ensure that there is full understanding of the functionality of the Warehouse Management System (WMS) and the Warehouse Control System (WCS).
6 Simulate…agree the scope of any simulation required, together with specified ‘what if?’ scenarios.
7 Design for downtime…include in your design exception routines that come into play in the case of critical equipment downtime.
8 Construct a critical path analysis…as well as bar chart planning, build a critical path analysis showing the effect of planning data from all parties involved – such as civil works, services, functionality testing etc – with drop-dead dates shown and reviewed at intervals during the lifetime of the project.
9 Set realistic targets…planning should contain realistic targets for design, build and implementation. Sufficient time should be allocated for commissioning, acceptance testing, operator training and so on.
Phase three comprises the project implementation:
10 Choose suppliers wisely…select only respected subcontractors to form a team that is capable of supplying equipment that will meet the contractual responsibilities of the main contractor.
11 Create partnerships…foster a partnership approach to your project, encompassing all parties involved in its successful delivery. Arrange team-building events and celebrate the achievement of key milestones.
12 Allow for migration…you should allow for migration from an existing system of working (maybe manual or semi-mechanized) to a new set of procedures for the automated system.
Phase four comprises support services; the supply and implementation of a new system into your business requires a commitment to provide all necessary support services to ensure its efficient operation. Whether supplied in-house or outsourced, these support services should be available for the planned lifetime of the system.
- Robotics & Automation 2013
- Automation on the upswing
- Amendment to Commission Regulation (EC) No 640/2009
- Confidence returning to UK manufacturing technologies
- A national success story
- EPTDA expands in the Middle East & Africa
- Innovating for the recovery, innovating for the future
- A system-oriented approach to assessing energy efficiency
- tGARD IN ACTION
- 110 YEARS OF INNOVATION