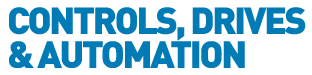
![]() |
Charlotte Stonestreet
Managing Editor |
A system-oriented approach to assessing energy efficiency
15 November 2013
The global demand for increased energy efficiency has led to the introduction of the Ecodesign Directive for electric drive solutions within the EU. As a result, systems are to be analysed in their entirety when it comes to assessing the operational efficiency of an electric drive solution. CAPIEL (European Coordinating Committee of Manufacturers of Electrical Switchgear and Controlgear) recommends that IE3 motors should be established as the minimum standard
While the industrial revolution of the 19th century mainly focused on the technical implementation of automatic production processes, the focus in the 21st century additionally lies on further aspects such as quality and environmental management and, since recently, energy management as well. While the first two aspects have long since been established, the subject of energy management is still in the early stages of reaching a significant development.
The DIN EN ISO 50001:2011, which replaces the previous DIN EN 16001:2009, represents an important standard in this context. Philippe Sauer, President of the European Coordinating Committee of Manufacturers of Electrical Switchgear and Controlgear (CAPIEL), and Michael Reichle, Vice President of CAPIEL, emphasise: "Saving energy should be an objective for each and every one of us and the assurance of a significant increase in energy efficiency is a fundamental obligation of all companies worldwide."
The Ecodesign Directive (EC) No. 640/2009, which was proposed by the European Commission for electric motors and which subsequently came into effect on June 16, 2011, is just one contextual example of measures being undertaken. The Directive specifies that manufacturers may no longer place IE1 motors on the market in Europe. Drives must deliver least the efficiency levels of the IE2 classification. This applies to three-phase asynchronous motors in the power range between 0.75 and 375kW with 2, 4 or 6 poles in S1 operation.
Further tightening
The Ecodesign Directive will be tightened effective January 1, 2015. This will be followed by a further tightening on January 1, 2017. Machine and system manufacturers would therefore be well advised to give thought to their compliance with the future regulations already today. "The decisive factor is having a system-oriented, product-wide approach to assessing energy efficiency", states Michael Reichle. By definition, the affected electric motors with a nominal output power between 7.5 kW to 375 kW must to reach efficiency level IE3 by 2015. As of 2017, this power range will be extended down to 0.75 kW. Alternatively, IE2 motors can be operated in combination with a frequency converter.
"This is exactly where the energy saving concept pursued by the EC 640/2009 Directive could unintentionally cave in", explains Sauer. The reason is that instead of further increasing the product-related energy efficiency from IE2 to IE3, this could, in some cases, even lead to higher energy consumption due to the way that certain systems are configured, as compared to speed-controlled three-phase asynchronous motors, applications consume less energy when motors are directly operated on the grid. In practice, this means that electric motors automatically operate at almost maximum efficiency above loads of roughly 30 percent of the nominal motor load when these motors are operated via motor starters such as contactors or soft starters. With fixed-speed applications, load changes are automatically compensated by the electric motor's self-regulating characteristics.
Pump drives, agitator units, conveyors and ventilation systems represent typical examples of such contactor- or soft-starter-controlled fixed-speed applications. Yet, constantly operated electric motors are also widely employed for the air-conditioning of buildings, for water supply and for many further applications. "A system comparison very clearly shows the significance of selecting the suitable overall system for the respective application from an energy saving point of view," emphasises Reichle.
Conveyor technology
A conveyor system for bulk goods handling, as is for instance often employed in mining applications, is driven by a 37 kW motor at a constant speed for 3,600 hours per year. The load profile shows a downtime of approximately 20 percent: For 10 percent of the time, the motor runs with 20 percent of the load, for 30 percent of the time, it runs with 40 percent of the load and for 40 percent of the time, it runs with 80 percent of the load. With this profile, the control solution with contactor and motor proves particularly energy-efficient as it has a total demand of 65.7 MWh per year. In contrast, a solution consisting of frequency converter and electric motor would entail an energy consumption of 70 MWh. Conclusion: Direct operation on the grid offers energy savings of 6.1 percent. Even without a standby phase, the energy savings still amount to 5.5 percent.
Sauer comments: "Even though the application of a frequency converter with an IE2 motor would be in line with the Ecodesign Directive as of 2015 or 2017, it would be counter-productive in many cases when it comes to energy savings." Michael Reichle adds: "When taking into account that energy costs account for more than 80 percent of the lifecycle costs of electric motors, a system-oriented approach proves extremely advantageous and economical. All this shows that every application has to be accurately analysed to determine the maximum energy efficiency attainable."
In many cases, the use of IE3 motors is preferable to IE2-classified products despite the higher costs. Experts estimate that the higher purchase costs of IE3 motors are redeemed with utilization periods above approximately 800 hours per year. "In addition to ensuring proper system selection, the motors' correct dimensioning should also be taken into account when selecting a product," advises Reichle.
Important for exports
A further aspect should also be considered: Manufacturers who adjust their machines and systems to the future energy assessment changes should not only comply with the tightening of the European Directive, but should also pay attention to global requirements. These requirements are, in some cases, already far stricter and call for highly efficient IE3 motors. Sauer reports: "Since 2010, for example, only motors with the particularly high efficiency rating NEMA (National Electrical Manufacturers Association) Premium, which corresponds to the IE3 standard, may be delivered to the USA. Since 2011, this also applies to Canada."
The decision in favor of IE3 motors within the selected drive concept not only offers advantages in terms of energy efficiency and cost savings, but also entails a whole range of additional benefits. For instance, these motors support the free choice between fixed and variable speeds without motor replacement. Moreover, the resulting minimized variance of employed motors entails positive effects for purchasing, logistics, spare parts supply and service. Furthermore, the design need not be adjusted when the European Ecodesign Directive is tightened in 2015 and again in 2017. Philippe Sauer and Michael Reichle agree: "Attaining maximum energy efficiency levels for electric motors should form the basis of responsible machine and system engineering, after all, energy savings benefit the world as a whole."
- No related articles listed
- Robotics & Automation 2013
- Automation on the upswing
- Amendment to Commission Regulation (EC) No 640/2009
- Confidence returning to UK manufacturing technologies
- A national success story
- Automation: plan to succeed
- EPTDA expands in the Middle East & Africa
- Innovating for the recovery, innovating for the future
- tGARD IN ACTION
- 110 YEARS OF INNOVATION