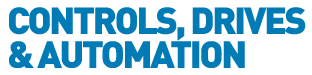
![]() |
Charlotte Stonestreet
Managing Editor |
Intelligent use of automation crucial to successful implementation of ErP Directive
25 April 2014
Even without legislation, energy efficiency is high on corporate agendas. Over recent years, driven by political, economic and social pressures businesses have made every endeavor to save energy in production systems and reduce CO2 emissions within the industrial sector. Here Controls, Drives & Automation discusses the issues with Stuart Greenwood, product marketing manager - Industrial Control and Automation at Eaton
In Europe the issue of energy efficiency is currently a major concern for the majority of producing companies. With the introduction of ErP Directive 2009/125/EC by the European Union, these companies are faced with the challenge of further reducing their energy consumption and thus also the CO2 emissions within the industry.
The UK’s 2008 Climate Change Act established the world’s first legally binding climate change target. The aim was to reduce the UK’s greenhouse gas emissions by at least 80 per cent, from 1990 levels, by 2050. By far the largest culprit is generating the electricity required to power the UK. In 2012 that was responsible for 1.78Mt of CO2. Within this structure the ErP directive is a framework for the design of products that use energy.
Since 2011 the minimum efficiency of asynchronous motors has been IE2. However there are two deadlines, both fast approaching, covered by the directive that are aimed at further increasing the efficiency of motors and widening its scope. Those deadlines fall on 1st January 2015 and 1st January 2017. The first deadline is for motors in the range 7.5kW to 315kW, a fairly wide spread of motors. The second deadline increases the range to bring in motors from 0.75kW, which covers the vast majority of motors sold around the world.
Broadening scope
The directive is a key driver to increase the efficiency of devices and systems, but taken in isolation is not the entire answer. As the scope of the directive broadens over the next three years the landscape becomes muddied. What was initially a simply matter of selecting an energy efficient motor is now made more intricate, compounded by the need to select further controls. But whilst challenging, that widening of the directive will hopefully allow users to change their perspective from the traditional device level view to one that considers the entire system.
Greenwood believes that it will be necessary for users to adopt a different mind-set when grappling with ErP compliance. "Users need to think about what they are trying to achieve as much as follow the directive itself if they are to realise the efficiencies on offer,” he explains. "Simply selecting the components is not enough, the whole system must be considered.”
What the directive says is that, for new installations the minimum motor efficiency standard will be IE3, or IE2 in used in conjunction with a variable speed drive. "That then raises the question of how does the user decide what is the correct control method to maximise the efficiency of the motor?” Greenwood adds. "Selecting an energy efficient motor is only the start of the process, using the motor effectively is the key. It can be the difference between extra saving or extra spending.”
There are two key effective methods for optimally leveraging energy savings potential in electrical drive engineering: motor starters or variable speed drives. In both cases, the components only yield the desired results if they are correctly deployed.
When dealing with applications with fixed speed and low switching frequency, motor starters are the most energy efficient solution. However if there is a requirement to change the speed or if there is a strong alternating load then the better solution is a variable speed drive.
According to the directive the minimum standard motor efficiency is IE3 or IE2 fitted with a VSD. However, the most efficient solution for a fixed speed installation is a motor starter (the power electronics components in a VSD introduce additional losses and inefficiencies into the equation). So whilst the directive permits it as an alternative, an IE2 motor +VSD is clearly not equivalent to a IE3 motor fitted with a motor starter in terms of efficiency. In order to find the most efficient solution it’s necessary to consider the speed and load requirements of the application.
Holistic approach
Greenwood believes that you need to step back and look at the system holistically. "Just selecting energy efficient components is not enough,” he says. "A whole system and application analysis is required.”
This requires an entirely new perspective. A change from the component level thinking to one that considers the entire system. Delivering energy efficiency should always be seen as a sum of all components and not focused on a single device. "The use of more energy efficient components is a good idea in itself, but not enough to maximise the efficiency of the overall system,” adds Greenwood. That is why a comprehensive energy consumption analysis of the entire system is first required to identify the best solution – variable frequency drive or motor starter – for increasing the energy efficiency in the user’s application. Only then can the automation solution which best increases the efficiency of the overall system, and the extent of the savings potential, be established with certainty.
Greenwood points to a simple example of a fan blower to highlight why a systems approach is required. "Imagine we were to select an IE3 motor for the application. This would meet the directive” he explains. "We can start it with a conventional motor starter, a good, low cost, efficient solution. But if we then put a mechanical dampener on the output of the fan the entire system would be less efficient because we are reducing the speed of the air by blocking it, wasting energy as heat noise in the process. The more efficient solution would be to vary the speed of the motor with a VSD instead of the starter.”
This brings us on to a final thought when considering energy efficiency, moving from short-term to long-term thinking. With that in mind it is certainly worth investing in energy efficient technologies such as IE3 motors. Even if modernising a system initially appears expensive, the use of drive components such as frequency inverters and soft starters often quickly pays in terms of savings made.
If the total costs over the entire lifetime of a device are considered, the investment is generally repaid after a relatively short period of time. Although it is not yet specified in law, it is worth investing in IE3 technology in combination with inverters or motor starters because it improves compatibility with future modifications to the system.
"Unlike other directives,” Greenwood concludes, "in order to successfully implement it you have to look at the complete system not just the components being used. That way you’ll see the benefits and the directive will have its intended outcome."
Key Points
- From 1st Jan 2015 the minimum efficiency class for electric motors in the range 7.5kW to 315kW rises from IE2 to IE3, or IE2 in used in conjunction with a VSD
- As the scope of the directive broadens users will need to moves from a traditional device level view to one that considers the entire system
- Investing in IE3 technology in combination with inverters or motor starters now will improve compatibility with future modifications