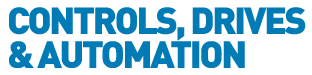
![]() |
Charlotte Stonestreet
Managing Editor |
Widening the scope of rack-and-pinion
01 May 2014
Rack-and-pinion drives use a rotational motor to affect linear motion via a rack-and-pinion combination. They are used frequently in long-travel applications, such as machine tool table positioning, that require high stiffness and accuracy
Stober's product range includes four distinct types: ZR, ZTR, ZTRS, and the newest member of the "Zeries", the ZV. The "ZV" rack-and-pinion system is an economy design which uses a shaft-mounted pinion without support bearings. This system is suitable for applications that don't require high accuracy gearbox shafts. An optional adjustment plate can be used for easy installation. The ZV is available for multiple gearbox styles and has an optional self-contained lubrication system.
ZV rack-and-pinion drives are DIN quality 7 and come in Modules 2, 3 and 4. The maximum feed forces have a range from 1.1 to 17kN, depending on the unit and the pinion. The linear backlash goes as low as 20 microns. Since they are shaft-mounted, the ZV pinions can mount to Stober's inline P and PE or its right-angle, K, KL or KS gearbox shafts. The units are also offered with an adjustment plate, allowing for easy installation and meshing of the pinion to the rack. The adjustment plate allows the gear unit and pinion to be raised or lowered between full tooth engagement and no tooth engagement.
Pinions & options
For the gear units in the P/PA/PK/PKX/PE/KS/K/KL series, the pinions on the rack-and-pinion drives are supplied in a backlash-free shaft-hub connection (shrinkfit and keyed). For accurate mounting and for lubrication of the rack-and-pinion system optional accessories are available:
Setting plates - There are specific setting plates for mounting and positioning of the different rack-and-pinion drives. Positioning can be made easier by an optional adjustment device;
Lubrication - A felt gear (with mounting kit) is used to lubricate the pinion or alternatively the rack. The grease can be supplied either decentrally via an automated lubricator or via a central lubricant supply;
Clamping set - For the gear unit models P5, P7, PE5, K2, K3 and K4, it is possible to attach the pinion with a clamping set.
Older cousins
Of the more established versions, the "ZR" features a design with a large helical gear mating directly to the rotating flange. It is ideal for high speed applications.
The "ZTR" rack-and-pinion system uses a flanged pinion without support bearings, and is suitable where the support housing has an interference. The pinion gear can easily be changed or removed. The mass moment of inertia ratios may be optimally adapted by varying the gear ratios and/or the number of pinion teeth.
Finally, the "ZTRS", as reported in CDA in the Oct/Nov 2012 issue, and shown in the picture, arises from a collaboration of Stober and Atlanta, a premier manufacturer of gear racks. It is a premium product aimed at very high torque, torsional stiffness, and tilting moment requirements. This design consists of a support housing with a flanged pinion, optional felt gear for lubrication, and a PH or PA gear.
The most immediately striking feature of the new HighForce ZTRS-PH(A) rack-and-pinion drive is the integral output bearing housing, a highly stiff supporting assembly for the rack pinion which relieves the load on the flange-mounted planetary gear unit bearings. The reduced tilting moment of this construction makes it possible to base the drive design on the torque actually required and on the feed force.
As a rule this means that the gear unit can be a size smaller than normally used in the past. Due to the comparatively small pinions, a higher output speed is necessary to obtain the required feed rate. Which means that the gear ratio is lower and in many cases a single-stage planetary gear unit can be used instead of a two-stage.
This gives the outstanding power density that should encourage many designers to use redesigned rack-and-pinion drives.
Rack-and-pinion
A rack-and-pinion is a type of linear actuator that comprises a pair of gears which convert rotational motion into linear motion. A circular gear called "the pinion" engages teeth on a linear "gear" bar called "the rack"; rotational motion applied to the pinion causes the rack to move, thereby translating the rotational motion of the pinion into the linear motion of the rack.
For example, in a rack railway, such as in the Snowdonia National Park (North Wales), the rotation of a pinion mounted on a locomotive or a railcar engages a rack between the rails and forces a train up a steep slope. Lock gate controls on a canal often use rack-and-pinion combinations, where the rotation of a shaft powered by hand or by a motor is converted to linear motion.
The rack carries the full load of the actuator directly and so the driving pinion is usually small, so that the gear ratio reduces the torque required. This force, thus torque, may still be substantial and so it is common for there to be a reduction gear immediately before this by either a gear or worm gear reduction. Rack gears have a higher ratio, thus require a greater driving torque, than screw actuators.
A rack-and-pinion is commonly found in the steering mechanism of cars and other wheeled, steered vehicles. Rack-and-pinion provides a less efficient mechanical advantage than other mechanisms such as recirculating ball, but less backlash and greater feedback, or steering "feel". Nowadays, the mechanism is normally power-assisted, usually by hydraulic or electrical means.
Key Points
- Rack-and-pinion drives are used frequently in long-travel applications that require high stiffness and accuracy
- Stober's ZV rack-and-pinion system is an economy design which uses a shaft-mounted pinion without support bearings
- It is available for multiple gearbox styles and has an optional self-contained lubrication system
- New economy planetary gearunit
- STOBER recognised for enhancing customer value
- Motor removal on the vertical axis
- RACK-AND-PINION REDESIGN CUTS GEAR SIZES
- High power supply for multi-axis drive systems
- New Winding Technology
- STOBER strengthens global presence
- More processing power
- Live motion control demonstrations
- More efficient planetary gear unit design
- No related articles listed