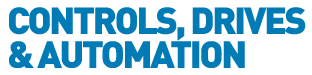
![]() |
Charlotte Stonestreet
Managing Editor |
Home> | AUTOMATION | >Encoders | >Multi-turn magnetic encoder pushes optical encoders |
Multi-turn magnetic encoder pushes optical encoders
18 August 2014
An additional Wiegand sensor is used to convert a standard magnetic encoder into a multi-turn absolute rotary encoder. Stefan Horvatic, of the Pepperl+Fuchs Plant Automation Division elaborates.
Typical positioning tasks in automation require a high degree of accuracy, as well as high resolution and fast response. This, in turn, requires devices that measure rotational movements, angular speeds, or the positions of moving parts. Rotary encoders are used in practically every area of general machine engineering or industrial automation.
Robot manufacturers have traditionally had to choose between sensors that were accurate, compact, or robust. Until recently, magnetic absolute rotary encoders typically offered accuracies of up to 1 to 0.5 degrees, a maximum resolution of 12bit, and cycle times over 600 microseconds. Whilst reasonable, these values are often far exceeded by optical technology. For this reason, applications with more stringent requirements of accuracy and dynamic range have mainly utilised optical rotary encoders. However, tough environmental conditions, such as dirt, vibrations, or extreme temperatures, present major challenges for optical rotary encoders.
Absolute rotary encoders based on a magnetic detection principle were developed specifically for use in harsh environments, such as in offshore wind turbines or in the mobile equipment industry. The key advantage is the non-contact detection principle, which means no mechanical gears to wear or incur maintenance and service costs.
The operating principle is based on a two-axis Hall sensor, which generates a sine or cosine signal via a rotating magnetic field. This signal is processed internally using optical scanning and an internal processor. It enables unique, compact single-turn absolute rotary encoders to be created in small construction volumes.
Redefining boundaries
Now, engineers at Pepperl+Fuchs are developing magnetic rotary encoders to redefine the boundaries. Boasting accuracies of up to 0.1 degrees, a resolution of up to 16 bit, and a cycle time of under 100 microseconds, these encoders can compete with their optical counterparts.
Combined with an additional Wiegand sensor, a single-turn absolute rotary encoder may be converted into a multi-turn absolute rotary encoder: a permanent magnetic field, made to rotate by the Wiegand sensor, generates a change in the direction of the magnetic field in the core of the Wiegand sensor, and in turn an induction voltage in the coil wrapped around the sensor. Energy is therefore always available during a change in the direction of the magnetic field, ie twice per revolution. This energy is used to count the revolutions electronically and to power the electronics. An additional benefit is that an internal battery is not required, so no data is lost and all position values are available after rebooting.
The integrated Wiegand sensor replaces delicate mechanical gears, saving on the space required for these gears. The advanced magnetic field technology of these encoders is accommodated in small housings as small as 36mm.
In a new range of magnetic absolute rotary encoders with accuracies of 1 to 0.1 degrees, Pepperl+Fuchs will in future offer rotary encoder technology that delivers new prospects for general machine engineering scenarios and plant automation. The design virtually eliminates maintenance and service costs, and prolongs the encoder's service life even in dusty, dirty environments and at extreme temperatures. Even in applications where compact housing designs play a role, magnetic absolute rotary encoders are opening up a surprising wealth of new potential uses.
- Positioning with maximum reliability
- Ultrasonic sensor system
- Measuring light grid
- Common Ethernet protocols supported
- Reads even on reflective surfaces
- High-end surge protection
- Sensor varient for US market
- Optical sensors for longer operating distances
- Sensor & positioning innovations
- With optical sensing principle