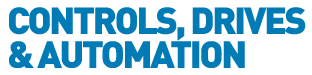
![]() |
Charlotte Stonestreet
Managing Editor |
Home> | INDUSTRY FOCUSES | >Medical & Pharmaceutical | >Technological remedies |
Technological remedies
26 August 2014
With issues such as falsified medicines, product contamination, stringent hygiene standards and the need for absolute accuracy high on the agenda, the pharmaceutical industry more than many sectors relies on the latest technology
One of the biggest issues currently facing the pharmaceutical sector is that of falsified medicines. As falsifications become more sophisticated, the threat to public health and safety becomes more acute and the need for a comprehensive international strategy increases.
Addressing the issue, EU regulators are ushering in a new era of pharmaceutical manufacturing and distribution compliance aimed at tightening up safety within the supply chain and eliminating falsified medicines. Automation socialist, Omron is highlighting the importance of machine vision in adhering to these regulations, which is the only way to read and verify the four key data elements proposed by the European Stakeholder Model (ESM) if they are to meet the 2017 deadline.
ESM – a partnership of organisations involved in the pharmaceutical supply chain – has developed an end-to-end medicine verification solution, consisting of four key data elements, to combat the entry of falsified medicine. This verification system plays a pivotal role in aiding manufacturers to adhere to the 2011 EU Falsified Medicines Directive (FMD) which requires manufacturers to apply safety features to verify the authenticity and identity of individual packs of medication, which will be mandatory by 2017.
To drive implementation of the FMD, a consultation has been undertaken to define the characteristics and specifications of a unique authentic pack identifier. While these findings, which will come under a Delegated Act, are not anticipated until later in 2014, it is highly predicted that it will include the adoption of a DataMatrix barcode. The verification system proposed by the ESM features a DataMatrix code carrying four key data elements which will also be required in a human readable format (manufacturer product code, randomised unique serial number, expiry date, and batch number).

Traditionally human readable code and data encoded within barcodes has remained fixed between batch runs of pharmaceutical products. The challenge arising from the proposed ESM concerns data management of the randomised unique serial number and the synchronisation of data between the printing device and verification solution. Omron’s flexible vision solutions are built on IPC technology, providing the flexibility to cope with a wide range of data management requirements and allowing interfacing with 3rd party devices such as printers. Omron’s vision solutions can interface with high level production management software to request the data required to verify the unique serial number, whether through database integration or simple manipulation of .csv data files.
Vision systems
Vision systems also play an important role in production processes in the pharmaceutical sector, enabling the implementation of evermore automated systems and contributing to a reduction in the risk of human error.
At GlaxoSmithKline's site in Evreux, France, 130 million boxes of inhaled forms (aerosols, inhaled products) are produced each year including the Diskus, a multidose powder inhaler that delivers a metered dose of medication. The marking of each Diskus is checked using a three-camera XG vision system. The first camera uses OCR to check an in-house code that is engraved with a YAG laser. The second checks the placement and diameter of the label; this inspects it for tears and makes sure that the legal notices printed on it are legible. The label is printed on a white background at a rate of 110 to 150 strokes per minute. The last camera is used to check a special label with a black background used for the Japanese market.

"We were looking for a vision system that did not require any direct operator intervention and thus would eliminate the risk of incorrect adjustments," explains Christophe Fourcin of GlaxoSmithKline. "Operators simply enter the code of the product to be inspected into the PLC controlling the vision system. That way they don't have to deal with the complex matter of programming the thirty or so sizes used.
"The very nature of the detection performed means that we have to routinely make changes to the vision system. That's one of the reasons why we chose Keyence's XG vision system. We wanted to have a tool that was ours and that we could modify as needed. With competing brands, reprogramming takes time and money. With the XG, we're in control and can even contact Keyence for assistance."
Metal detection
It's not just vision systems that play a pivotal inspection role in pharmaceutical production. Lock Inspection Systems has recently introduced a new, refined version of its flagship INSIGHT pharmaceutical metal detector. Designed to help manufacturers maintain product integrity, whilst also accommodating different elevations of tablet press out-feeds, it has enhanced stability, which counteracts out any surrounding noise pollution that can cause false contaminant readings and increase product wastage. Hygienic according to FDA standards, the frame is now height adjustable and has a new clamping sleeve, making it easier and faster for operators to move the metal detector between production lines.

Pharmaceuticals, biopharmaceuticals, vaccines and anti-virals must be manufactured and packaged with the utmost caution and attention to detail. Strict quality and safety standards, such as the Good Manufacturing Practice (GMP), means inspection accuracy is now mandatory. INSIGHT PH provides users with fully documented IQ (Installation Qualification), OQ (Operational Qualification), and PQ (Performance Qualification) validations. This gives manufacturers all of the documented evidence needed to verify that processes and procedures meet FDA, GAMP and GMP specifications.
Every tablet counts
The pharmaceutical sector is also a rich area for OEMs such as Pharma Packaging Systems, a specialist in the design and manufacture of electronic tablet/capsule counting machines. The company is deploying the latest PRT2 precision rings and GV3 linear slides from HepcoMotion for a new counting machine with tare gross weighing system. The HepcoMotion products were selected for their "accuracy and performance”, factors well proven at Pharma Packaging – the company has been a HepcoMotion customer for over 10 years.
The demand for the new PC180 counting machine with tare gross weighing system arrived at Pharma Packaging via an application based on substitute narcotic tablets for a pharmaceutical customer in the USA.
"The system had to be quick, hence the configuration allows three containers to be filled with tablets, counted, weighed and checked simultaneously,” explains technical director, Ian Barnes. "However, the overriding priority is accuracy as we are dealing with a very important pharmaceutical application.”
The PC180 system indexes empty containers three at a time, weighs them and records the weight (tare). The containers are then indexed again and filled with a counted number of tablets. A final index sees the containers being weighed once more. Finally, the tare weight is subtracted from the product weight and the system identifies containers that either comply with the target weight, or fail. Good product advances to an out-feed conveyer, while failing product is diverted down a chute to a reject area.

The PRT2 precision ring system is based on HepcoMotion's V guide technology and features an integral rack and pinion drive, which facilitates the precise indexing mechanism thanks to its friction-free, zero-play motion.
"We’ve found HepcoMotion's PRT2 system with integral rack to be quite unique, at least we haven’t seen it anywhere else,” says Barnes. "It’s very easy to design around. In particular, it has allowed us to do away with the centre bearing mounting. This means we can run the conveyor through the centre – it doesn’t need to be offset – thus enhancing accuracy - because containers that are not at 90° to the centreline can sometimes be a problem. We also like the fact that the PRT2 can run dry, without any need for lubrication, which is very important for pharmaceutical applications.”
Elsewhere in the same machine, HepcoMotion's GV3 linear motion V guide and actuator systems are used for two different applications: in a vertical configuration to raise and lower the filling nozzles, thus accommodating different container sizes; and in a horizontal configuration to guide pneumatic cylinders which actuate gates that allow tablets through before closing-off for the next batch.
High hygiene
Like all aspects of the pharmaceutical industry, packing facilities have to meet high standards in respect of hygiene, quality and performance. Space is also often at a premium in production plants – Robotronic AG specialises in robot-aided handling systems that meet these strict size requirements. The Swiss company works with a modular robot cell developed in house, termed Modular Robot Technology or MRT for short. Only Mitsubishi Electric robots are used in this system.
Robotronic has developed a handling module for supplying ready-to-use syringes to the final packing facility of an international pharmaceutical company in Germany. The space available was extremely tight at roughly three square metres, and a supply rate of 400 syringes per minute was stipulated. The solution also had to permit switching between different syringe carriers and syringe formats ranging from 0.5 to 10ml.
By applying the modular principle, Robotronic is able to combine any Mitsubishi Electric robots in a cell with other elements such as conveyor belts, camera systems or linear axes. Two type MELFA RV-4FL robots from Mitsubishi Electric are used in the syringe handling solution. These are compact overhead articulated-arm robots with six axes. No other mechanical elements such as lifting or rotating components are required.
Part of the solution is a supply system for the tubs, i.e. the thermoformed plastic containers in which the combs or nests are transported. Conveyor belts are normally used for this, but they take up a comparatively large area. Robotronic, on the other hand, uses a rotary turret that it has developed and that sits on the same basic framework as the robot cell to which it is connected. The turret is loaded manually on the outside with up to ten full tubs before rotating 180 degrees and being emptied by robot.

Incorporated into the custom solution are two MELFA robots of type RV-4FLM-Q1-S15, the related CPUs Q172DRCPU and a PLC CPU, type Q03UDECPU. The rotary turret is driven by a Mitsubishi Electric MR-J4 servo motor with motion CPU Q172DCPU. All CPUs form part of the iQ Platform, a multi-CPU platform from Mitsubishi Electric. The special feature of this solution is that the robots are not only suspended overhead but also work in pairs in the minimum of space.
The current MRT model can achieve a cycle rate of 400 syringes per minute into the emptying rail, but the solution can process up to 600 units per minute. To do this, a further axis is added to the system, driven by a Mitsubishi Electric servo motor MR-J4.
PLC, motion control, drive as one unit: A complete solution for PG ExpressIMA PG offers a complete range of packaging solutions that includes machines for applications such as cartoning, rotary vacuum forming, rotary sealing, flat sealing and tube-filling besides of end-of-line packaging.
Key Points
- The issue of falsified medicines is being addressed with an end-to-end medicine verification solution
- Accuracy and performance are behind Pharma Packaging Systems' use of PRT2 precision rings and GV3 linear slides from HepcoMotion
- Mitsubishi Electric robots are used by Robotronic in a handling module for ready-to-use syringes
- INEOS to build hand sanitiser plant in 10 days
- New robotics strategy
- Carter bearings goes face-to-face
- New technologies to transform farming
- Digital adoption critical for an enterprise-led recovery
- IoT device security advanced to thwart evolving threats
- Productivity-boosting digitalisation
- Pump up the savings
- Jeremy Hadall appointed Visiting Professor at Cranfield University
- New method of manufacturing micromotor windings
- ROBOT FOR DELICATE ASSEMBLY
- maxon motor Benefits Compounding Pharmaceuticals Market
- The new maxon motor magazine is here.
- Prescription for production
- Medical machine evolution
- Axis Modules DC 061 and DC 062
- Pharmaceutical focus
- Waterproof motor & drive solutions
- Does pharma have productivity cure?
- UK MedTech suffering from market uncertainty