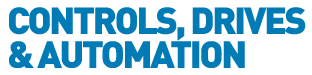
![]() |
Charlotte Stonestreet
Managing Editor |
Home> | INDUSTRY FOCUSES | >Medical & Pharmaceutical | >Does pharma have productivity cure? |
Does pharma have productivity cure?
04 April 2017
As well as bringing life-saving and life-enhancing medicines to patient, the pharmaceutical sector is a major contributor to the UK economy and represents a huge success story when it comes to productivity – something which is sorely lacking many other UK industry sectors. Charlotte Stonestreet looks at some of the sector issues and developments
Indeed, a recent PwC report report, commissioned by the Association of the British Pharmaceutical Industry (ABPI) highlighted that the industry had the highest productivity of any high technology sector (over £330,000 GVA per employee), in addition to achieving exports worth £30bn. It also has more research and development spending in the UK than any other sector at £4bn per annum.
While there are concerns over Brexit – in addition to uncertainties over leaving a trading bloc that accounts for nearly half the country's exports, the pharmaceutical sector is particularly susceptible to issues concerning regulations – as a rule the sector tends to be able to weather the storm of changing monetary and political conditions because, after all, people still need medicines no matter what the economic climate.
As you might expect from such a healthy industry, advanced manufacturing techniques and adoption of automated processes are to be seen right across the pharmaceutical sector. However, as is often the case, there is still room for further development. Indeed, Robert Harrison, pharmaceutical industry manager of industrial software expert COPA-DATA identifies a somewhat cautious approach to new technologies, particularly in some of the less mature subsectors, including biopharmaceuticals.
The entire pharmaceutical industry - including biopharma - is under constant pressure to deliver cost effective new drugs. On the one hand, manufacturers need to develop small batches of personalised medicine very quickly, while on the other hand, the industry has to provide low cost and high volume production of common products like insulin or malaria vaccines.
However, biopharma is less mature than conventional pharmaceutical production and few companies in this sector have in-house manufacturing capabilities. This pushes cutting-edge process innovation and operational efficiency to the CMO (Contract Manufacturing Organization), supporting the trend of smaller, more agile facilities concentrating on flexibility, cost efficiency and speed.
Process technologies have advanced over recent years, breaking down production facilities to evolve the modular concept of standardised functional process modules, which help manufacturers simplify, verify and re-use designs. This flexibility means additional functionalities can be added or replaced in a seamless fashion.
Delivering cost-effective treatments places pressure on manufacturing to get the most out of its people and equipment. Improving agility and effective use of equipment, tries to balance biopharma’s long process duration times and expensive raw materials. Where possible, pushing down manufacturing costs can be achieved through optimisation, reduced material usage and energy consumption.
Harrison identifies newly evolving drugs and treatments, changes in industry standards and rising energy prices as some of the main reasons why biopharmaceutical manufacturing requires more flexible processes and production lines.
Industrial automation plays a key role in making manufacturing lines suitable for several products. However, hardware is of little use without a communication system and software package that offers a holistic view and coordinates different stages, from research and development to the shop floor production systems, storage and transport.
The industrial automation software needs to be intuitive and easily configurable. This eliminates the lengthy and complex process of writing and validating programmed code. By using parameterisation, automation software becomes easy to implement in pharmaceutical manufacturing environments, therefore increasing process flexibility.
Continuous manufacturing
Many of the most successful companies in the pharmaceutical sector have recognised that one of the main factors when comes to competitiveness is the continuous utilisation of production capacity. In practise, this means that active ingredients are produced in compact, closed units, with a higher degree of automation and fewer manual interventions. Optimal Industrial Automation has been particularly involved in the shift from batch to continuous production, enabled by advanced Process Analytical Technologies (PAT), that this process requires.
"In oral solid dose manufacturing, conventional batch production may require 30 hours of manufacturing and quality control activity," explains Optimal managing director Martin Gadsby. "But waiting time between quality checks means that this activity may take 30 days to complete."
PAT aims to address those delays by bringing offline quality checks online, typically through the use of spectroscopy techniques combined with multivariate prediction engines, these verifying that the material is within specification in real time. It is then possible to introduce closed loop control based on product quality attributes, thus ensuring optimal product quality at all times. "PAT allows companies to bring that 30 day period back down to 30 hours, and even to as little as 90 minutes if you move to continuous production," Gadsby adds.
These new manufacturing approaches offer a host of other benefits to manufacturers too, including dramatic reductions in scale up time, high-value in-process inventories and rejected material, smaller manufacturing plants and lower energy consumption. They also help manufacturers maintain consistent quality despite inevitable variations in the raw materials, this in turn allowing the use of potentially lower cost ingredients.
The benefits may be compelling, but PAT and continuous production can be extremely challenging to implement. Part of the challenge is meeting the needs of the regulators. The FDA for example explicitly supports the implementation of PAT in its latest Good Manufacturing Practice (GMP) guidelines, but manufacturers must be able validate that their systems are capable of performing as they should.
The challenges don't stop once PAT systems are up and running either. "If your manufacturing system relies on instrumentation, you have to demonstrate that these instruments are properly referenced, with full calibration records," says Gadsby. "You also need to accommodate regular re-referencing in production, with the use of redundant or surrogate methods applied while those instruments are offline."
And then there's the challenge of storing and managing the terabytes of data generated by production lines every week. To help its customers with these issues, Optimal has developed a software platform – synTQ, which acts as both as a high speed data collection tool and central, regulatory complaint repository for all the models, PAT Methods, configuration parameters, calibration information and process data associated with production.
"Continuous production and PAT techniques have progressed fastest in oral solid dose manufacturing," says Gadsby. "But now there is increasing interest in its application in API production, biopharmaceuticals and process chemistry."
Blister filling
Compactness and dexterity were two important features of the anthropomorphic FANUC LR Mate 200iD robot selected by FlexLink for a cutting-edge medical assembly line located in Italy. Combined with a FANUC M-1iA delta robot and an integrated iRVision system, FlexLink completely re-engineered the blister packing operation, automating an intricate and time-intensive job that previously performed manually.
Increasing productivity enables the FlexLink system to consistently produce 60 blister packs per minute, the M-1iA delta robot starts by undertaking the first selection task. With a work diameter of 280mm, this specific model was designed by FANUC to deliver accurate movements and handling of small objects at high speeds, so suits the application perfectly.
Presented in bulk quantities on the conveyor belt, the delta robot picks up and using FANUC iRVision, quality checks each product component. “Integrating the visual system eliminates the need to orientate objects as the robot finds them. It meant we didn’t need further conveyors and devices that would have made the conveyor system more complex and cumbersome,” explains FlexLink’s engineering manager Davide Zuffa. Imperfect pieces are rejected at this phase of the process, remaining on the conveyor to be discarded.
With the quality inspection complete, the delta robot then places each product piece onto a middle conveyor for presentation to the blister-packing robot. This FANUC robot - the LR Mate 200iD – which undertakes the blister pack packing task was customised with a double gripper (EOAT). This enables it to handle and load two product pieces simultaneously resulting in an increased output.
But the unique positioning of the medical pieces means that they can’t simply be loaded into the blister packs and sealed. Instead, the robot is programmed to carefully manipulate and fold each medical device before delicately pushing into the blister pack. At this stage the vision system checks for correct insertion of the assembled medical device to ensure it is seated correctly within the blister pack. This guarantees a good seal and eliminates any rework.
Intelligent motion & control
Parker Hannifin has secured new business for its servo motors and drives with Italian packaging machine specialist Marchesini, which uses its experience, knowledge and expertise to design and build complete lines to handle the whole production process for pharmaceutical and cosmetic applications. The company’s products provide automated solutions for challenging tasks such as handling drugs dispensed in vials, ampoules and blisters. It also makes machines to take care of final packaging in forms such as bundles, boxes and pallets.
Marchesini has worked closely with Parker Hannifin on many machines over many years. The relationship and collaboration between the two companies has led to a large degree of continuity in the drive and control solutions adopted from one platform to another with the benefits in reliability and performance that brings.
In this particular latest application, Parker provided close technical support from the early design stages to develop a motion and control solution for the company’s Integra 520V Robotised Blister Line. The machine, which is composed of two sections and integrates both blister forming and packaging into a carton, is the fastest and most advanced line of its type produced by Marchesini. It has a throughput of up to 520 blisters and 500 carton per minute.
Parker’s SMH series, low inertia brushless servo motors and SLVDN single-axis servo drives are used extensively throughout the Integra 520V including to control the automatic reel unwinder, for accurate positioning in the pre-heating and forming section, in the coding, cutting, perforation and outfeed area, and finally to drive an unwinding roller which transfers the blisters to the cutting station.
Serialisation solution
Mandated serialisation standards across markets require pharmaceutical and medical device manufacturers to adopt specified standards to track and trace products across their supply chains. The newly updated serialisation solution from Rockwell Automation is helping these manufacturers and OEMs think beyond compliance and capitalise on major business benefits, such as long-term profitability, with a comprehensive, scalable, end-to-end supply-chain platform.
Built on the latest Rockwell Software PharmaSuite manufacturing execution system (MES) software, the new serialisation solution v4.1 is more scalable to adapt to a wide variety of packaging-line technologies and production-management systems. Easy integration across control and enterprise levels means the solution provides a centralised platform for managing serialisation data and facilitates product traceability across the entire supply chain.
A new Logix-based unit controller with FactoryTalk View HMIs from Rockwell Automation enables scalability, allowing the company to apply this solution to a variety of delivery models – from full, turnkey solutions to retrofit and OEM solutions – to meet the needs of virtually any customer. The unit controller acts as the connection point between each production line and various system devices. Beyond providing serialisation, the solution helps manufacturers improve troubleshooting and proactive maintenance by providing direct visibility into the full, end-to-end process – production through distribution.
Key Points
- Evolving new drugs and treatments, changes in industry standards and rising energy prices mean biopharmaceutical manufacturing requires more flexible processes and production lines
- Continuous utilisation of production capacity this means active ingredients are produced in compact, closed units, with a higher degree of automation and fewer manual interventions
- Mandated serialisation standards across markets require pharmaceutical and medical device manufacturers to adopt specified standards to track and trace products across their supply chains
- RAG can deliver successful AI integration for manufacturers
- Businesses given more time to apply new product safety marking
- AI model generation service
- ZX Spectrum relaunched as gaming console
- Shaping the future of spare parts production
- Sellafield and AtkinsRéalis operate Spot robotic dog
- Fighting labour shortages with cobot deployment
- Routeco announces virtual exhibition stand
- Technological remedies
- IP rights vs. AI training needs
- ROBOT FOR DELICATE ASSEMBLY
- maxon motor Benefits Compounding Pharmaceuticals Market
- The new maxon motor magazine is here.
- Prescription for production
- Technological remedies
- Medical machine evolution
- Axis Modules DC 061 and DC 062
- Pharmaceutical focus
- Waterproof motor & drive solutions
- UK MedTech suffering from market uncertainty