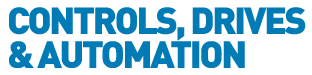
![]() |
Charlotte Stonestreet
Managing Editor |
Home> | INDUSTRY FOCUSES | >Water | >All about efficiency |
All about efficiency
02 March 2015
Plant floor equipment is gradually becoming more digitised and connected, able to perform high value asset and process monitoring and diagnostics. This can all be available in real time across operations, facilities and even the supply chain. Nowhere is this more true than in the water and utilities sector.
Gathering reliable, real-time data from all areas of the National Grid is critical to identifying problems early and preventing power disruptions.
National Grid UK has adopted a platform based on the National Instruments (NI) CompactRIO system. It can provide more measurements and also adapt with the evolving grid. This interconnected network includes 136 systems, with 110 permanently installed in substations throughout England and Wales and 26 portable units that provide on-the-go spot coverage as needed. The software application running on both versions is identical.
"National Grid selected the NI platform to develop a flexible, powerful, and connected measurement system capable of gathering and analysing large amounts of data to better detect grid-wide trends," says Peter Haigh, National Grid UK. "Compared to its existing infrastructure, implementing a smarter, more connected system allows us to manage change, optimise energy sources, and plan for the future grid."
Sustainable housing
500 tonnes of CO2 per year is expected to be saved at Kingston Heights, a new sustainable housing development in south west London, thanks to its pioneering use of water from the River Thames to supply heating, hot water and cooling. Compared to a combustion-based system, and is expected to reduce energy bills on the development by around 16% per annum.
Kingston Heights is a £70 million development in Kingston-Upon-Thames that will comprise 137 residential units, including 81 private apartments, 56 affordable homes and a 142 bedroom hotel. When completed, this estate will be heated and cooled by a pioneering open water heat pump system, with virtually no on-site carbon emissions. Automation provider Electraspec has specified four WEG CFW11 variable speed drives within the control panel to operate the heat pumps.

Electraspec designed a bespoke pumping system control panel, equipped with two 18.5kW and two 30kW CFW11 drives. The system works by recovering the solar energy which is naturally stored in the Thames, with up to 150 l/s of water being extracted after passing through a two-stage filtration process. The water then passes through heat exchangers to harvest the low grade heat before being returned to the river with a temperature change of no more than +/-3˚C.
Using multi-pump control, the CFW11 controls up to five pumps and maintains constant pressure, regardless of flow fluctuations. The VSD also monitors suction pressure and tank levels, alternating the pumps according to their operating time, and ensuring uniform wear and tear for motors and pumps.
A SoftPLC function with the inverter can be operated remotely. "We are able to control the system from our laptops and are immediately alerted if there is a problem,” comments Eric Knight of Electraspec. "For example, this function enables us to operate speed and run commands without having to be physically on site”.
Reclaiming heat
In an anaerobic digestion (AD) biogas plant, not utilising the heat naturally generated as part of the process could be costing thousands of pounds a year, particularly if heat is being added elsewhere, such as drying or concentrating digestate (the organic biofertiliser output from the AD process).
Optimal AD plant performance can be achieved by fine-tuning the feedstock mixture and retention times to maximise biogas production, as well as regularly servicing the CHP engine to maintain electricity generation. But some aspects are overlooked, such as the waste heat from the engine.

There are four main areas of the AD process where heat, which is available and may otherwise be wasted, can be utilised: feedstock pre-heating, digester heating, pasteurisation and evaporation. One solution is to capture and transfer this wasted heat with heat exchangers. Despite their widespread use in industries such as food manufacturing and the chemical sector, they are under-utilised in the AD industry.
According to Matt Hale, International Sales Manager, HRS Heat Exchangers, using heat exchangers in the pasteurisation system is more efficient than using tanks with heating jackets as they have a much lower heat requirement - up to half of that of some systems. This is because tank systems have lower heat transfer efficiency and usually dump the hot water after use, rather than reclaiming it.
Cornish waste-to-energy plant
Strict European regulations are in force on landfill disposal of waste materials, so many waste-to-energy plants are being built. Yokogawa France is supplying control and safety instrumented systems to Vinci Environment UK for a waste-to-energy facility that is being built for SITA Cornwall.

The Cornwall Energy Recovery Centre is being built in St Dennis, Cornwall. Scheduled to start operation in 2016, it will be capable of handling 240,000 tonnes of residual waste per year, and will generate sufficient electricity to power around 21,000 homes.
The Cornwall project draws on experience gleaned at Vernea, an innovative waste treatment facility built in central France for SITA (Suez Environnement Group). For boiler control and auxiliary functions, the Centum VP integrated production control system and the Prosafe-RS safety instrumented system are specified.
Released in February 2015, Centum VP R6.01 is an enhanced version of Yokogawa's integrated production control system. This first R6-level release acknowledges the most stringent industry requirements for safe and reliable plant operations and environmental protection and introduces crucial new control system components. Its intuitive engineering environment can dramatically reduce the time required to configure and install a control system. The system features the FieldMate Validator N-IO loop commissioning software, a software tool that is used to verify the wiring and relevant operations for any newly installed field instrument or field I/O device.

Centum VP R6.01 features an expansion of Yokogawa’s range of I/O devices: Yokogawa has signed OEM agreements with Pepperl+Fuchs and MTL Instruments Group.
Resilient infrastucture
Thames Water is continually reinforcing the resilience of its supply network. One new shaft connects the company's Hampton works to the existing Thames Water ring main – the 80km long, 18m diameter pipeline that runs 50m below London.

The major challenge at Hampton was lack of space. A way was needed to install large pumps and medium-voltage equipment without impacting on existing operations. Current water supplies must not be affected as the existing pumps were still in operation – a phased changeover had to be accomplished without any interruption.
The pump units were split into high pressure and low pressure, with the low-pressure changeover being the primary concern - the ones connected directly to consumers - Thames Water had no surface reservoirs in the area to fall back on.
Ten Rockwell Automation Allen-Bradley PowerFlex 7000 medium-voltage drives - some of the first from Rockwell Automation's new production facility in Poland - were coupled to the pumps, each with an Allen-Bradley ControlLogix programmable automation controller (PAC) on board. These were in turn connected to a master controller – another Allen-Bradley ControlLogix PAC – via EtherNet/IP, which itself was connected to the site's SCADA network. Visualisation was provided using Allen-Bradley PanelView HMIs running FactoryTalk View.
An integrated network means that a huge amount of real-time information is available to tap into. Information gathering already covered the process control parameters, but Thames Water wished to include operational conditioning to encompass predictive and planned maintenance.
"Using the new installation and the new connection to the ring main, we can now pump water from the Hampton site to places all over London, ready to step in should any outages occur elsewhere," explains Mark Morrison, Thames Water's Project Manager. "Thanks to the modern motors and the control technology, we are also realising electricity savings greater than £100,000 per year."
Abstraction upgrade
Elsewhere, one of Thames Water’s biggest abstraction facilities is the Littleton Raw Water Pump Station (RWPS) in Surrey. Built between 1923 and 1925, the pump station is responsible for maintaining the water supply to one of the largest raw water reservoirs in the UK, providing fresh water to London and some neighbouring counties. The station was originally fitted with four 900mm discharge horizontal double suction axially split case pumps. In the 1950s, three pumps were modified to electric motor drives and have been operating using this arrangement since.

The Littleton RWPS has not been operating at optimum efficiency; improvements could be made to reduce loss of pump priming, minimise cavitation, simplify start up, maintenance and control procedures and reduce energy usage. In addition, Thames Water wanted to implement an automated system with remote control function, which would allow a faster and more efficient pump start up procedure, while also making monitoring easier. In the existing system, operators had to go to the site and work for three to four hours to start up a pump, making the operation time-consuming and costly.
The final requirement was providing dual electrical power supply from the National Grid and up to 1.5MW of power supply from a photovoltaic (PV) system located in an adjacent field.
The Boulting Group completed an holistic, objective site testing and evaluation process of the entire system, including Front End Engineering and Design (FEED). This resulted in a set of recommendations, including the upgrade of assets like switchgear, motors, drives and control systems.
The original impellers were limited in efficiency to around 80%. A pump upgrade was recommended, including a complete redesign and manufacture of the pump impellers to help improve the net positive suction head (NPSH) characteristic and pump efficiency. The adopted design allows an improvement to 87% pump efficiency and increased reliability during start-up and operation. Another benefit of the new design was the minimisation of cavitation and its damaging effects on the pump components.
To resolve the poor priming, a new and automated priming system uses motive air vacuum ejectors and continuous water level monitoring. Old packed glands are replaced with mechanical seals. This reduces leakage to virtually zero.

In the new installation, the pumps, motors, drives and channel level are automatically controlled to optimise the Specific Energy Consumption (SEC) of the system. Each component is controlled individually and automated, using Boulting PSOp (Pump System Optimisation), installed within SCADA managed Programmable Logic Controllers (PLCs).
The PSOp software continuously monitors and analyses the pump system, taking into account the known characteristics of each component in terms of performance. The system automatically identifies the speed the pump needs to operate at to achieve optimum efficiency, and how many pumps need to be running at any given time to ensure the lowest specific energy consumption.
Key Points
- National Grid UK deploys advanced, upgradable grid measurement system to provide better operational data for the condition of the UK grid
- Electraspec specifies four WEG CFW11 variable speed drives within control panel to operate the heat pumps
- Yokogawa France is supplies control and safety instrumented systems to Vinci Environment UK for a waste-to-energy facility for SITA Cornwall
- Modern motors and control technology realise electricity savings greater than £100,000 per year for Thames Water
- IET announces new chief executive and secretary
- Mercedes-Benz acquires YASA
- Partnership to optimise warehouse worker & robot collaboration
- SECTOR SUPPORTED BY INJECTION OF ENGINEERING
- Productivity-boosting digitalisation
- Automation suite helps to program multi-axis projects
- Ford recruits robot test drivers
- BBC to give all year 7 pupils free pocket-sized computer
- Things ain't wot they used to be
- In the frame
- Automation In The Utilities - Not Big Data, But Better Information
- Improved life cycle costs
- Water works with WEG
- Smart methods to securing supplies
- Smarter water management
- Smarter working in utilities & water
- Smart power enablers
- Servitization strategy for electric valve actuators
- Two pumps prove better than four
- White paper highlights need for digitalisation in water utlilities