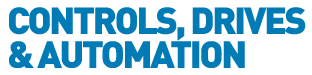
![]() |
Charlotte Stonestreet
Managing Editor |
Editor's Pick
ARTICLE
Compressor energy recovery kit
18 March 2015
Atlas Copco is aiming to rapidly increase the adoption of compressor energy recovery with the launch of an all-in-one kit that simplifies integration with a building’s central heating and hot water system.
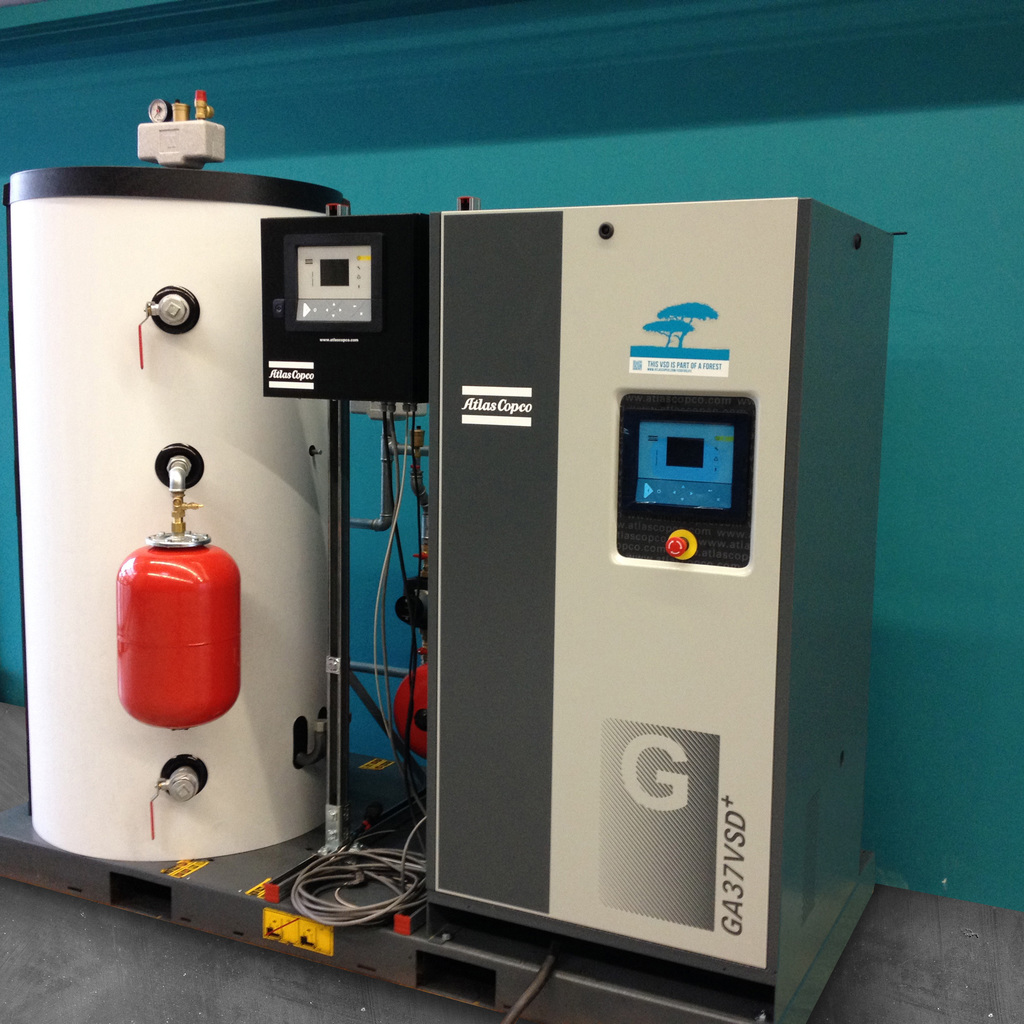
The Thermo Kit is a complete package of energy recovery components that can be installed quickly and easily to provide the user with a highly efficient source of supplementary hot water at no additional cost.
Thermo Kit has been developed to overcome the installation challenges that have hampered widespread uptake of compressed air energy recovery. It enables users to convert excess heat from a compressor that is fitted with an energy recovery (ER) unit into hot water, which is stored in a buffer vessel connected to a typical domestic or office central heating system. Using this system, a typical Atlas Copco GA45+ compressor could achieve savings of £2,331 on a user’s annual gas bill, for example.As much as 94% of the electrical energy used by an industrial air compressor is converted into heat and lost through radiation in the compression process. Therefore, a properly designed heat recovery unit can recover from 50% to 94% of this available thermal energy as low-grade heat, which can be used to heat water.
Ken Revell, Sales Manager for Atlas Copco’s Industrial Air division (South), said: "The potential of compressor energy recovery, whereby excess heat produced by an active air compressor is captured in the form of hot water, is well proven and in a period of high energy prices and environmental concern, this cannot be underestimated. Many businesses are benefitting from energy recovery today but installation has traditionally presented challenges since there is no universal template for connecting the compressor and central heating system. We wanted to bridge that gap and that’s why Thermo Kit heralds such a transformation in the way energy recovery is implemented. With joined-up thinking, we have made the process faster and simpler than ever before, so that more plants can take advantage of energy recovery.”
Thermo Kit is intended to be as simple to install as a system of solar panels. Only a limited amount of engineering work is required and installation is usually swift and seamless.
Thermo Kit comprises a choice of two buffer tank sizes, connections, circulation pump and control unit. The 400-litre buffer tank, which has a 50kW heat exchanger, is designed to work alongside Atlas Copco’s 11kW to 45kW compressors, while the 800-litre buffer tank, which has a 90kW heat exchanger, can be connected to 55kW to 90kW compressors.
The buffer vessels, which can store hot water for up to 24 hours, offer full isolation to meet stringent safety standards and comply fully with the latest ErP 2015 regulation.
As the brain of the system, the control unit assesses the performance of the system in real-time and displays energy-saving data in order to self-validate the return-on-investment (ROI). Typically, full ROI is achievable in 12 months.
The control unit displays a visual overview of the installation, the status of energy recovery and compressor running information. Using digital communication, it can also collate data on compressor status, compressor oil temperature and temperature in / out for real-time data collection.
MORE FROM THIS COMPANY
- Atlas Copco Turns Its Hand To Vacuum Pumps
- Masters Of Air
- Live compressed air energy efficiency demo
- Compressed air costs cut
- VSD compressors
- Atlas Copco to acquire Edwards
- Compressor range extended
- Capable of halving central vacuum supply energy costs
- Atlas Copco completes acquisition of Edwards Group
- Water-Injected VSD Compressors
RELATED ARTICLES
- No related articles listed
OTHER ARTICLES IN THIS SECTION