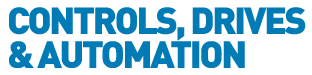
![]() |
Charlotte Stonestreet
Managing Editor |
Home> | DRIVES & MOTORS | >Variable Speed Drives | >ENERGY SAVING: AN OLD MESSAGE WITH NEW PROMISE |
ARTICLE
ENERGY SAVING: AN OLD MESSAGE WITH NEW PROMISE
31 October 2012
Many businesses are still not taking advantage of the production benefits of Variable Speed Drive compressors. Paul Clark, industrial air manager for Atlas Copco Compressors, argues that large strides are on the horizon for energy savers.
For so many years has the message been preached about the energy savings obtainable with variable speed drives (VSDs), that the term "VSD Fatigue” has been coined! VSD technology has been available since the 1990s and has particularly benefitted the compressed air sector, where the technology is especially suited to the unpredictable demands of modern manufacturing. In fact, 10% of all electricity used in industry is attributable to compressed air applications.
Yet recent research carried out by the Carbon Trust has found that UK businesses could make significant savings of over £630m every year simply by using more efficient electric motors and variable speed drives (VSDs).
VSDs are well suited to compressed air applications, particularly for their ability to boost compressor performance by matching air supply to air demand.
Air demand in 80% of all compressed air installations shows fluctuations, which can prove costly if compressors are constantly operating at high capacity. The key feature of a VSD compressor is its inclusion of an integrated frequency converter that varies the speed of the drive motor to exactly match changes in compressed air demand. As a result, VSD compressors use the minimum amount of energy required and can cut the cost of compressed air energy by up to 35% compared to conventional compressors.
Top of the list of barriers to adoption is perceived lack of access to funding. However, when it comes to energy saving projects, there are several different funding schemes available. One such scheme is the Enhanced Capital Allowances (ECA) program, which is managed by the Carbon Trust on behalf of the government and encourages businesses to invest in energy-saving technologies and equipment as specified on the Energy Technology List (ETL).
Another, more recent, development is the Energy Efficiency Financing Scheme. This is providing £550m over the next three years for investment in energy efficient technology, includ - ing compressed air equipment. The number of available schemes clearly demonstrates that funding is available for UK businesses wishing to optimise production and save on energy costs through investing in energy efficient equipment, such as VSD compressors.
Finally, in July 2011, Atlas Copco launched a 0% finance scheme to encourage investment in the latest compressed air technology, including its full range of energy efficient VSD compressors, most of which use Siemens or ABB VSDs, matched to motors from the same supplier. Another factor which has historically impeded take-up of energy saving opportunities has been that it has been the province of the overloaded plant manager.
Yet recent research carried out by the Carbon Trust has found that UK businesses could make significant savings of over £630m every year simply by using more efficient electric motors and variable speed drives (VSDs).
VSDs are well suited to compressed air applications, particularly for their ability to boost compressor performance by matching air supply to air demand.
Air demand in 80% of all compressed air installations shows fluctuations, which can prove costly if compressors are constantly operating at high capacity. The key feature of a VSD compressor is its inclusion of an integrated frequency converter that varies the speed of the drive motor to exactly match changes in compressed air demand. As a result, VSD compressors use the minimum amount of energy required and can cut the cost of compressed air energy by up to 35% compared to conventional compressors.
Top of the list of barriers to adoption is perceived lack of access to funding. However, when it comes to energy saving projects, there are several different funding schemes available. One such scheme is the Enhanced Capital Allowances (ECA) program, which is managed by the Carbon Trust on behalf of the government and encourages businesses to invest in energy-saving technologies and equipment as specified on the Energy Technology List (ETL).
Another, more recent, development is the Energy Efficiency Financing Scheme. This is providing £550m over the next three years for investment in energy efficient technology, includ - ing compressed air equipment. The number of available schemes clearly demonstrates that funding is available for UK businesses wishing to optimise production and save on energy costs through investing in energy efficient equipment, such as VSD compressors.
Finally, in July 2011, Atlas Copco launched a 0% finance scheme to encourage investment in the latest compressed air technology, including its full range of energy efficient VSD compressors, most of which use Siemens or ABB VSDs, matched to motors from the same supplier. Another factor which has historically impeded take-up of energy saving opportunities has been that it has been the province of the overloaded plant manager.
While some, typically larger, manufacturing companies are now employing energy managers, in the SME space, it is still relatively rare to have a dedicated energy manager.
Key Points
TIPS FOR AN EFFICIENT COMPRESSED AIR SYSTEM
- Ensure the compressor is the correct size
The size of a compressor should be based, not on the total air using equipment, but on the usage factor at any given time. - Use air audits to provide a clearer picture
To ensure that energy is not being wasted it is advisable to carry out a compressed air audit. This will give a highly accurate picture of how much compressed air is being used on site, as well as showing how much energy is being wasted in producing it. Atlas Copco engineers use iTrak data loggers to establish a true picture of a system’s air use without any interruption in air supply or production. - Keep compressors in top condition at all times
Regular compressor maintenance not only keeps the production facility operating at top efficiency, but it is also an opportunity to reduce running costs. - Match air supply to air demand
In 80% of all installations, air demand shows important fluctuations. In 70% of installations, load cycle lies between 40 and 80% meaning that there is potential for an average of 35% energy savings if VSD compressors are used.
MORE FROM THIS COMPANY
- Live compressed air energy efficiency demo
- 'VSD for Life' campaign
- Monitor Your Compressor Installation With Mobile App
- Compressor range extended
- Secure compressed air energy savings
- VSD compressors
- Compressor energy recovery kit
- Water-Injected VSD Compressors
- Energy savings of up to 50%
- Vacuum pump brings massive potential for energy savings
RELATED ARTICLES
- PUMPED UP PERFORMANCE
- SOFT STARTER OR VARIABLE SPEED DRIVE?
- Jeans With Less Energy
- Enhanced to Withstand Tough Environments
- Savings From Improved Torque Ratio & Efficiency
- Modular VSD
- Updated installation guide for power drive systems
- UK drives manufacturer seals global automation deal
- WEG motors & drives power high-efficiency air blowers
- Powerful Savings
OTHER ARTICLES IN THIS SECTION