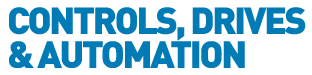
![]() |
Charlotte Stonestreet
Managing Editor |
Home> | INDUSTRY FOCUSES | >Automotive | >Beyond the manufacturing plant |
Beyond the manufacturing plant
05 May 2015
While the typical image of the automotive industry may be of huge manufacturing facilities, the sector has a far wider remit than the production line
Located near Lyon, France, GreenMot specialises in testing internal combustion engines, propulsion systems and energy systems, in particular in the field of automotive, heavy goods vehicles, railways and industrial equipment.
According to Stéphane Londos, company president and founder: "We adapt our instrumentation to the products to be tested, not vice versa. By carrying out non-intrusive tests, we obtain far more reliable results. Another of the strengths of our company is being able to define the tests to be carried out according to the results required and analyzing the results obtained. We can therefore make suggestions to our clients for improvements to be made in their products in order to improve their performance."

This strategy exploits to the full the experience gained by Londos over some fifteen years with leading car manufacturers and suppliers. It also has implications for the instrumentation used by the company and HBM has became GreenMot’s preferred partner in this area.
As well as carrying out out large numbers of torque measurements, GreenMot utilises an embedded acquisition system which is able to collect data from a wide variety of measurements (torque, deformation, rotational speed, temperature, pressure, humidity, air flow rate, etc.). With its modular QuantumX system, HBM has the solution to all these requirements.
Londos, again: "We work in the field of applied research which is far more demanding in terms of the measurement quality. The HBM products meet the metrological requirements here, whether in terms of measurement uncertainty, repeatability, synchronization of the measurements.
"HBM is able to produce ‘tailor-made’ sensors that we need for installation of the instruments on the structures and for carrying out non-intrusive measurements. We have therefore gone over to regularly co-developing together with the German company."

In order to carry out these non-intrusive measurements and design customised sensors, GreenMot bases its development on the arithmetic model of the equipment to be tested. This means that even before having access to the real equipment, the company is able to prepare the tests, the positioning of the sensors, the routing of the cables, etc., and study the design of the sensors. This results in enormous time savings.
For GreenMot, tests on motors used in hybrid cars present a new challenge when it comes to measurement because the electric power supply comes in the form of a stream of electric pulses of several hundred volts with complex form at a frequency of 1 to 25 kHz. This pulse train comprises several very rapid transients with variable intensity which have to be recorded reliably in order to be able to analyse the performance of the motor, and to understand the influence of the power supplies on the speed and torque delivered by the motor.
Since QuantumX is not suitable for this type of application, GreenMot examined systems, even testing a high-tech system specially developed for analysing disturbances on the power grid. However, this system did not allow long-term data acquisition while recording all the details of the signal and, once again, HBM appeared to be the best choice.

"We decided in favour of the GEN2i system from the Genesis HighSpeed series which is capable of recording high-voltage signals and of operating at sampling frequencies of up to 100 MS/s – more than enough to allow the details of the signals to be analyzed,” says Londos.
GEN2i (just like QuantumX) is used as an acquisition front-end. The digitised measurements are transferred via an optical GigabitEthernet link to a workstation where they are visualised, stored and analysed. The optical link permits perfect insulation between the supply voltage to the motors (up to 700 V) and the workstation. The data processing is assured by thePerception software package developed by HBM for high-speed data acquisition which is capable of visualising 10 GB of data in 10 seconds.
Software support
Employing over 15,000 people, Volkswagen’s primary transmission site at Kassel supplies almost four million manual and automatic transmissions every year, and includes Europe’s largest light-alloy foundry to produce aluminium and magnesium housing components. The Kassel plant also reconditions old engines and gearboxes, and manufactures 3.5 million exhaust systems each year.
"We’ve used RomaxDESIGNER for more than four years,” says Juri Kniss, calculations engineer at Volkswagen. "As a factory site, our focus is not to design gear sets, it’s to ensure the gearboxes we manufacture are consistently of the required quality.
"With RomaxDESIGNER we can assess the effects of gear manufacturing variability within a fast and accurate simulation.”
Engineers at Kassel use RomaxDESIGNER to analyse existing designs and assess how the tolerance variability of gear microgeometry will impact on the NVH of the finished gearbox. "Romax allows us to do this by integrating rapid modelling and analysis of gears, shafts, bearings and housings within a single gearbox model to predict how components interact with each other.

"We have also recently used RomaxDESIGNER to predict bearing preloads required for a new EV gearbox, which we achieved by calculating the interaction between three shafts, and to look at which rings to mount in the factory,” and the electric motor,” Kniss explains.
"The housing hasn’t a great degree of stiffness, leading to complex interactions. So we want to change the bearing preloads and see the effects, to identify the correct settings to use when manufacturing the gearbox. To validate the methodology we set up a test rig to compare results and were able to see that Romax provided a good validation.”
As part of the same project, RomaxDESIGNER was also used to analyse the fit between the motor stator and the gearbox housing, to predict any housing deformations and the resulting effects on the gears and bearings.
During the gearbox assembly the stator is fitted into the housing. This results in an interference fit and a degree of deformation of the housing, which causes some displacement of the gearbox bearings. The interference fit was modelled externally and the bearing displacements then applied as preloads to the Romax model.
"In this case, we had a highly detailed model that we could apply to all of the bearings, to examine the effects of the interference fit with different shaft misalignment predictions being evident along with different contact patterns for most of the gear sets.”
Tank testing
Leader in the production of fluid systems, moulding parts and thermo systems for the automotive industry, Veritas is using a Moog electric simulation table with tilt to test the behaviour of fluid in in automotive fuel and fluid tank systems, a test application that requires large angular motions. Veritas ordered the system to perform tests on automotive SCR (Selective Catalytic Reduction) fluid tanks that are used to inject liquid-reducing agents in catalytic converters for the reduction of harmful emissions.
The electric simulation table with tilt is designed to perform dynamic liquid sloshing tests, and has the ability to simulate real-world road conditions. This new technology development has already been adopted by Fiat Group Automobiles (FGA) for testing fuel tank systems. The behaviour of the liquid and components of the tank system can be tested and evaluated in a confidential laboratory setting, as opposed to a test track. The test results will allow Veritas to make the right choices when developing new fluid tanks. The company chose the Moog system because it is specially designed for this application, uses plug and play electric actuation technology and is easy to use and maintain.

The Moog test system comprises an electric simulation table with an innovative additional tilt table on top for increased pitch and roll motion. The electric simulation table is used to reproduce the higher frequency road profiles, where the tilt table can simulate the cornering and acceleration behaviour of the vehicle. This enables Veritas to include various conditions during driving that lead to extreme fluid-sloshing effects, such as instant braking or very sharp cornering manoeuvres. In addition, the Moog Replication test software module will enable Veritas to replicate and play out time history drive files that were recorded at the test track.
Racing simulator
Linear actuators from Warner Linear, part of Altra Industrial Motion, have been specified for use on a new racing simulator which has been designed to give the driver the most realistic high speed experience possible. The actuators are used to create movement in the seat which simulates pitch and roll with braking, acceleration and cornering G-forces. The Warner Linear K2x models were specified due to their exceptional response time and load carrying capacity.

Using a combination of 3D screens, surround sound and advanced gaming software, the racing simulator allows drivers to experience the exhilaration of motorsport first hand. However, the final touch that really adds to the authenticity is the motion controlled chair that allows the driver to feel all of the forces that would be exerted upon them if they were in a real car. The movement is controlled by motion outputs as part of the racing software and delivered through the two Warner linear actuators attached to the underside of the racing seat.
The K2x linear actuators are from Warner's B-track range. They have been designed for use in tough, high-load applications where they will be in frequent use. With a load of 270kg (max. load 1,270kg) the actuators are able to travel at 25mm/second with a 200mm stroke (50mm-600mm available) and respond instantly thanks to their high performance electric motor. It was this precision performance that made them ideal for the application – perfectly translating every movement the car makes from the screen to the driver's seat.
The ball screw actuators are designed to provide years of trouble-free service in harsh industrial environments. They feature integral o-ring seals, heavy wall rod and extension tubes, bi-directional holding brake and Nitrotec treated end fittings for superior strength and corrosion resistance. Models also feature heavy-duty, sealed double ball bearing motors and a mechanical torque limiter for end of stroke and overload protection. High performance synthetic lifetime lubrication is used throughout. Unique, patented screw end bearing guides provide smooth extension operation; high side-load capability and aids screw re-lubrication.
Key Points
- GreenMot invests in HBM GEN2i system from the Genesis HighSpeed series to test motor used in hybrid cars
- Engineers at Volkswagen’s primary transmission site at Kassel use RomaxDESIGNER to assess the effects of gear manufacturing variability
- Veritas uses Moog electric simulation table with tilt to test the behaviour of fluid in in automotive fuel and fluid tank systems
- Linear actuators from Warner Linear specified for use on new racing simulator to create movement in the seat
- New technology lets humans & autonomous robots understand each other
- SPS 2022 returns to live format
- £60m boost for floating offshore wind
- Virtual world for offshore wind robotics innovators
- Electric & autonomous lighting the way
- Linear motion solution selection
- New wave in renewables
- Technological remedies
- Fast Payback In High Power Applications
- Covariant launches to bring universal AI to robots