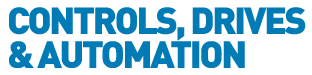
![]() |
Charlotte Stonestreet
Managing Editor |
Home> | INDUSTRY FOCUSES | >Automotive | >DRIVING TECHNOLOGY FORWARD |
DRIVING TECHNOLOGY FORWARD
29 October 2012
Hard hit during the last recession, the British automotive industry continues to make a healthy recovery, attracting investment and generating new jobs. Controls, Drives & Automation looks at some of the technologies behind the headlines
Key Points
Brammer, has joined forces with SKF to help deliver a turnkey solution for an automotive application for Expert Tooling
- MacDonald Humfrey and Exmac Automation have joined forces to help automotive engineering specialist Ricardo create near cleanroom production environment
- Autodesk design and visualisation software has been key to the successful design of Volvo’s latest concept car
- Initial tests on a Stop-Start automotive supercapacitor module developed by CAP-XX show battery life increased by over two times
Although the automotive industry in Britain can be seen as a mere shadow of its former self in terms of who actually owns the volume car manufacturing companies, with all of the big players now in overseas hands, few can doubt that the sector is at the forefront of the drive to revive British manufacturing.
Long gone are the days of inefficient production lines resulting in dubious quality vehicles that had little appeal outside the domestic market, and the UK is now home to some of Europe’s most productive and flexible vehicle manufacturing facilities, as well as being a global leader for low carbon technologies.
With an industry-wide desire to source more components and manufacturing solutions locally, as well as a worldwide drive to increase efficiency across the board, the automotive industry is a hotbed of new developments and ingenious use of technology.
TURNKEY SOLUTION In one example, maintenance, repair and overhaul (MRO) product and services supplier, Brammer, has joined forces with bearings and lubrication specialist SKF to help deliver a turnkey solution for an automotive application at the Tyne & Wear operation of Expert Tooling. The major assembly tooling supplier initially contacted SKF for assistance with the development of a lubrication system for a new piece of tooling to insert bushes into position on a car suspension subframe.
Phil Gazeley of Expert Tooling commented: "This application had been previously undertaken manually and while the vehicle assembly plant wished to automate it, it was not possible to use robots on this occasion. Consequently there was a need to design and implement a system which delivered consistent lubrication before automatically loading the bushes into the subframe at the correct pressure.
"The input from Brammer and SKF was vital in developing the basic design of the system which has been adapted to cope with bushes of different sizes and has brought major efficiencies to the end user.” Trevor Wooding of Brammer’s Sunderland Sales & Service Centre added: "This is an excellent example of how Brammer can add significant value by working with expert partners to develop innovative, bespoke solutions and then supply all the components needed to implement those recommendations. On this occasion our collaboration with SKF has created a system which is reducing process times and manual handling of lubricants for a major automotive manufacturer.” In line with ever increasing demands for productivity, manufacturing facilities found in the automotive industry, at all tiers, are amongst some of most innovative around. MacDonald Humfrey Automation (MHA) and sister company Exmac Automation have joined forces to help automotive engineering specialist Ricardo create a state-of-the-art 600m2 assembly facility to build its first ever high-performance engine at its Technical Centre in West Sussex.
Providing a near cleanroom production environment the facility has the capacity to produce 4000 engines annually across two daily shifts. Its core is a ten-station vertical conveyor mini-line supported by incoming materials inspection and line-side delivery of components. Each station is equipped with a sophisticated MacDonald Humfrey ‘Human Machine Interface’ (HMI) providing guidance to each operator on the precise sequence of operations required at each stage of assembly‘ to ensure No Fault Forward’ (NFF) assembly. Tools at each station are instrumented to provide data directly into a central warranty database for each engine, providing complete finished product traceability.
Each line station is interlocked via its HMI to ensure that all operations and checks have been successfully completed and recorded before the line can be indexed and the engine moved forward to the next station.
Says Ricardo’s Dave Thompson: "Exmac understood our brief, asked the right questions and provided their own engineering ideas to help us achieve our objectives. Because space couldn’t accommodate a continuous loop line, designing the conveying system proved particularly challenging, as did the relatively slow 50-minute Total Average Cycle Time (TACT) required for the low – eight engines per shift – production volume and the ‘nofaults- forward’ culture. And it’s not just in the manufacturing processes that innovation comes to the fore. Key to the successful design of Volvo's Concept You car, which was unveiled at the Frankfurt Motor Show last autumn, Autodesk design and visualisation software enabled the concept modelling team to quickly create digital prototypes from the designer’s initial sketches. The design was quickly honed and tested on screen, helping to save time and maintain the original design integrity behind the concept. As a result, designers were able to get to the best option with the technical surfacing and visualisation of the car as quickly as possible, without having to start from scratch with every iteration.
TIGHT DEADLINES
Although the Volvo team was working under a particularly tight deadline, timescales such as this are becoming typical in such a competitive industry. Cars are becoming increasingly complex and sophisticated with a high technical content, yet manufacturers are under pressure to design them faster, while incurring lower costs. Like Volvo, a growing number of manufacturers are using Autodesk Alias to accelerate the entire design process from concept to class A modelling.
When it comes to product development, the need to reduce vehicle emissions and improve fuel efficiency is a constant influence.
For example, CAP-XX has developed a supercapacitor module for use in automotive Stop- Start applications, which provides significant performance improvements relative to batteryonly systems. This application for CAP-XX’s supercapacitor technology represents an import The module removes the dependence of the Stop-Start system on the vehicle’s lead- acid battery to supply cranking current to start the engine. CAP-XX has shown that in extended testing its module reduces wear on the battery, which is a common failing of existing systems. Batteries in many of the existing systems may have a functional life of as little as 18 months because of the intensive demands made on the battery.
As an additional benefit, the CAP-XX module also provides superior engine starting performance in cold weather, and can be used as an energy store for regenerative braking systems where fitted.
The CAP-XX Stop-Start module is being tested under the New European Drive Cycle standard, and has so far completed 100,000 Stop-Start cycles at room temperature, with minimal wear on battery performance. During the test, the CAP-XX module has maintained the battery voltage above 11.8 volts, providing a very reliable voltage platform for the vehicle electrical systems.
- Fighting labour shortages with cobot deployment
- Nineteen Group acquires Broden Media Limited
- Free app helps assess & control workforce infection risk
- University research to receive major funding boost
- New 7-axis cobots
- The train now standing...
- Can machine learning make it in medical?
- IoT network for wildlife protection
- Loop Technology partners with Robotmaster
- Miniaturisation springs forward in time