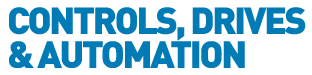
![]() |
Charlotte Stonestreet
Managing Editor |
Home> | INDUSTRY FOCUSES | >Automotive | >Automotive Manufacturing Shifts Up A Gear |
Automotive Manufacturing Shifts Up A Gear
17 January 2013
Like any industry sector, automotive manufacturing presents its own challenges, particularly when it comes to arduous environments
Although today’s car production plants might be almost unrecognisable to someone from the 1970s, they are still challenging environments when it comes to implementing new and existing technologies.
Increasingly, car manufacturers – particularly those at the higher end of the market catering for specific customer preferences such as optional equipment, colour ways and trim – are tracking each individual vehicle right the way through the production process. Tracking each vehicle to deliver exactly the right customer choices means knowing, in real time, the exact specification of each individual vehicle and the stage it has reached in the production process. And, for car manufacturers who are compelled by marketing pressure to offer many choices to attract customers, it can be months or years before the same combination is requested again, so a wrongly kitted-out car could be an expensive mistake.
Attaching a unique identifier early in manufacture is therefore essential to avoid identification mix-ups. It enables the vehicle to be recognised throughout production to final assembly and completion. RFID systems, with transponders on the work piece and read/write interrogators at the appropriate points in the product flow offer many advantages in complex manufacture and assembly. The transponders are capable of holding large amounts of information which can be added at each stage.
The information stored provides traceability and quality assurance data, details the exact processes undergone and the components added to meet the required final specification. The data can remain attached and accessible throughout the vehicle’s lifetime for full accessibility, even aiding eventual recycling.
But, according to Tim Stokes, Auto-Ident product specialist at Sick UK the ‘Achilles heel’ of RFID has traditionally been its tendency to become inaccurate in locations with extensive metal surfaces and mass, or volumes of fluids, which may distort and reflect the radio signal. One customer of Sick, a prestige automotive manufacturer at a production plant in Germany, was experiencing difficulties with consistency of operation through the paint shop.
The ‘Achilles heel’ of RFID has traditionally been its tendency to become inaccurate in locations with extensive metal surfaces
Use of standard RFID had resulted in frequent line downtime from null reads, as well as some specification errors when the wrong car was selected. There had even been collisions where a car body became ‘invisible’. As a result, some cars had to be rejected. Paper label identification did not survive the paintshop drying process, and attempts to use RFID after the paint shop, combined with additional barcoding, had also not delivered the accuracy needed for efficient manufacturing operations.
The Sick engineering team was called in and recommended new Sick RFU630 UHF read/write interrogators, which were installed at 24 points in the paint shop. These rugged and compact devices were required to operate under very unfriendly conditions including metal walls, ceiling and floor, heavy metal machinery such as the conveyor, other car bodies and a temperature of up to 180˚C.
Reader location was important. For instance, by ensuring that the actual reading point was located where the car body stopped briefly before it entered the drying kiln, optimum transmission conditions were obtained. To match the RFID device, a rugged and long-life UHF transponder tag developed by Sick especially for the automotive industry was attached to each car body, designed to withstand conditions inside the kilns of 230˚C.
Despite the ‘high noise’ metal environment, the RFID system was found to operate with better than 99.98% accuracy over approximately 350,000 scans a day.
Following the paint drying, the bodies are loaded in any order onto a skid conveyor section for the next processing stages, such as seam sealing by robot. As these processes proceeded down three parallel lines and on to the complexities of engine and interior fit out, accuracy of the individual on-vehicle records is crucial. With the transponder, the on-car records are always available to the manufacturer, at any stage of the vehicle’s life.
The RFU630 is able to accommodate up to three external aerials, and has a reading range of between 0.4 and 1.2m, delivering excellent coverage. Operating on the Sick IDpro platform, it is easily integrated with a wide range of SCADA/Ethernet systems, as well operating easily with other Sick ident technologies such as 1D/2D barcodes for a factory- wide automated ident system. Configuration is very simple using the Sick SOPAS tool with its auto-ID function, and as well as application specific software, freely definable outputs, for example operating actuators, can be incorporated.
Flexible architecture
Tapping into what is now the world’s largest vehicle market - China – the Changan Ford Mazda Nanjing Company was established by Ford & Mazda in 2004. The plant is based on the Mazda "Triangle Control” concept and produces multiple models, meaning a high degree of flexibility is required.
The Triangle Control concept is a hierarchical principle intended to address plant control at all levels, from model data at the top to actuators and sensors at the bottom. The overall aim is to keep things simple and standardised. As a hierarchical system, networks play a key role, and the network Mazda chose was CC-Link. The plant was a significant project for Mitsubishi Electric, whose systems are used extensively throughout it.
A particular example of how the architecture allows flexibility is in the body shop where the line must be able to cope with the production of various different models. The body framing system currently allows the production of six different well known models; Ford’s Fiesta (sedan and wagon), Mazda’s 2 (sedan and wagon) and 3 (old and new versions), as well as reserving capacity for two additional future models. The entire shop is automated using Mitsubishi controllers and CC-Link networks. The system divides into 24 stations, with each having multiple controllers in charge of three to four welding robots, making almost 100 robots total. A further 10 stations handle the under body operations. CC-Link helps maintain operational flexibility by allowing production engineers to conveniently reserve future configurations. When actual production machinery is added, it’s a simple matter to enable the new parts of the network. This leads to a ‘plug and play’ style of network configuration, significantly reducing project lead time.
Despite the hostile operating environment, the line has run for approximately seven years without experiencing any hardware failure
The welding line is a good demonstration of CC-Link’s high degree of reliability even in adverse conditions. Despite the hostile operating environment, the line has run for approximately seven years without experiencing any hardware failure or network malfunction related downtime. Further enhancing this exemplary record is the easy system maintainability enabled by the network’s diagnostics. There is no need for complicated parameter settings, and the engineering team found it easy to create clear diagnostic displays to allow operators to see network status at a glance. Further, if faults were to occur, CC-Link allows malfunctioning stations to be removed from the network, serviced and then returned to operation without disrupting operation for the rest of the line.
The cost saving benefits of CC-Link were also a key factor in its selection. The use of standard cabling was seen as a major benefit, and the lack of special connectors or other additional hardware also contributed to cost effectiveness. Moreover, compact hardware footprints meant smaller cabinets could be used for network stations, allowing cost savings through smaller cabinets and location flexibility.
Performance was also an important selection factor. Despite large station totals and long distance requirements, CC-Link was able to offer millisecond update times, well within the plant’s requirements for data flow and machine cycle times. "This plant was almost a textbook example of how CC-Link offers benefits to large scale applications such as those in the automotive industry”, commented John Browett, general manager of the CC-Link Partner Association. "CC-Link has an established relationship with Ford and Mazda, beginning with the new Ford Mustang line several years ago in the US. No doubt the benefits obtained in that installation influenced the selection of CC-Link for the Nanjing plant.
"The plant also is further demonstration of CC-Link’s ever increasing success in China. It’s clear to see that large end users such as Ford and Mazda have a huge influence on the OEM community. Hence we expect that the obligation to provide CC-Link solutions in the Chinese market will only continue to grow. Our Gateway to China programme is intended to help European companies leverage this opportunity.”
Robot assembly
It’s not just the car manufacturers that are looking to maximise efficiency. There is a whole raft of specialist companies that play an important role in the automotive sector, supplying manufacturers with vital components.
When it needed to automate the assembly of a moulded plastic spigot, a leading automotive parts manufacturer asked industrial automation expert, ALPHR Technology, to devise a solution that would be cost effective, compact, reliable and easy to maintain. After carefully analysing the application, the ALPHR Technology team concluded that a solution based on an Omron SCARA robot, used in conjunction with a vision system and other automation products from Omron, would be the best way to meet these requirements.
ALPHR Technology decided that a machine using conventional multi-axis pick-and-place technology would be complicated to design and build, inflexible, and ultimately difficult to maintain. The solution based on an Omron SCARA robot would, however, solve all of these problems as well as addressing a requirement for the machine to have the smallest possible footprint.
Careful costing of the machine, taking into account not only the cost of equipment and materials, but also the cost of design and construction, revealed the robotic solution to be significantly more financially attractive.
As built, the spigot assembly machine works on a part that the operator has manually loaded into one of the ‘nests’ in the machine’s rotary assembly table. A pneumatic cylinder pushes the part fully home and then the table indexes. Next, the robot takes the four compression limiters, one at a time, from vibratory feeders and places them into the part.
Two Omron FQ vision sensors confirm that the limiters are all present and correctly positioned, and then the table indexes again, moving the part to a station where the limiters are inserted with Pneumatic cylinders and then a force push out test is carried out by applying a precisely controlled force.
The table indexes once more to bring the part to the final station where it is pressurised and tested for leakage. Depending on the results of the test, the part is transferred either to the pass bin or the fail bin, the latter being kept behind a locked door within the machine to ensure that defective parts can never be accidentally mixed with good products. Passed and failed parts are automatically counted, and the machine notifies the operator when the bins are ready to be emptied.
The new spigot assembly machine has now been working on site for several months, and is fully living up to expectations. While, as planned, the rate of production of the new machine is not substantially different from that of the manual assembly line, the percentage of reject parts is greatly reduced, as the dependable robotic placement of the compression limiters and the 100% inspection by the vision sensors make it virtually impossible for incorrectly assembled parts to go forward to the final testing stage.
Key Points
- Sick RFU630 UHF read/write interrogators have been installed in the paint shop of a prestige automotive manufacturer
- The Changan Ford Mazda Nanjing Company uses a CC-Link network to address plant control at all levels
- An automotive parts manufacturer uses a solution based on an Omron SCARA robot to assemble moulded plastic spigots
- A renewed urgency for energy
- Rare part of early computer discovered
- 3D Hubs launches Online Engineering Summit series
- Linear motion solution selection
- New method of manufacturing micromotor windings
- Making smarter use of shop floor intelligence
- Drive for hostile environment protection
- Scalable automation for greener construction
- Dewatering automation contract
- MARCH awarded place on £50m United Utilities Monitoring and Control Systems Integration framework