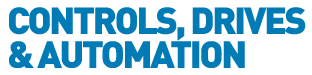
![]() |
Charlotte Stonestreet
Managing Editor |
Conditioning monitoring tactics risk hampering industry warning
22 June 2016
An overreliance on condition monitoring data could be hampering maintenance teams in their quest to improve plant operational efficiency, warns industrial service provider, ERIKS UK.
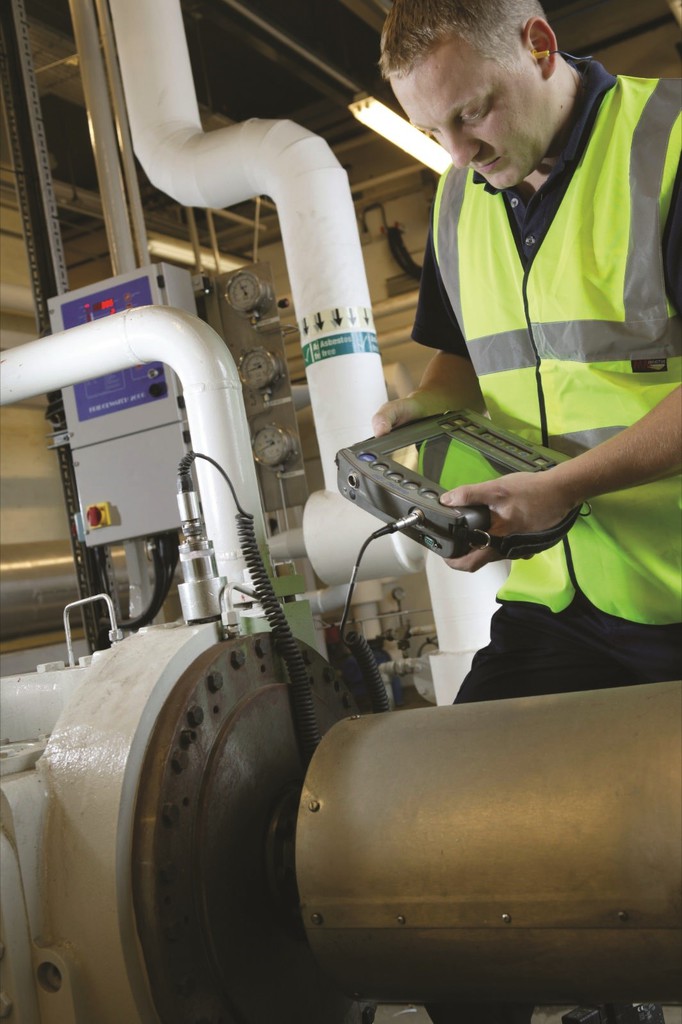
Recent technological innovations have enabled maintenance engineers and facilities managers to measure and monitor the performance of their plant more than ever before. However, UK industry risks making vital mistakes if first-hand diagnostic work is phased out in favour of extensive data analysis, according to David Manning-Ohren, an expert in condition monitoring at ERIKS UK.
“Our ability to capture vital data has really advanced the potential of condition monitoring in recent years, yet we now find ourselves in a position where we’re almost overloaded with it. Given the increase in available information, some in the industry may be guilty of data-grabbing, and trying to let computers undertake the diagnostics rather than a trained engineer,” comments Mr Manning-Oren.
Condition monitoring has been around for hundreds of years, and stems from operators who oiled and greased the mechanical parts within a specific application, being close enough to the application day-in, day-out to notice if something was amiss.
Mr Manning-Ohren continues: “If you don’t have the diagnostic capabilities of an engineer equipped with extensive thermodynamic, vibration analysis or flow technology knowledge, then the data you’ve gathered will be redundant. For example, an inverter can add on noise to a motor that could easily be misconstrued as a bearing defect. Until you understand vibration signatures and evaluate these with respect to electrical noise versus mechanical noise, you wouldn’t necessarily know the difference between the two.
“Ultimately, the devil’s in the detail not the data when it comes to condition monitoring,” concludes Mr Manning-Ohren. “Whilst the level of data we can gather as part of the condition monitoring process will undoubtedly pave the way for much greater insight into improving overall process performance, without an expert on hand to undertake the diagnostic and follow-up remedial work, the data itself is redundant.”
- Prevention is better than cure
- Education key to unlocking I4.0
- SKF UK announces ERIKS UK and Ireland as its first Maintenance Partner for the UK
- Servicing the invisible customer
- UK 'badly underprepared' for Industry 4.0
- Top tips to keep your belts in business
- HEALTH & RECOVERY
- ERIKS is first SKF maintenance partner for UK
- MOTOR MANAGEMENT
- Guide to enhancing MRO efficiency
- No related articles listed