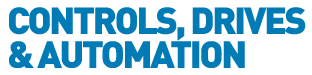
![]() |
Charlotte Stonestreet
Managing Editor |
Home> | POWER TRANSMISSION | >Drives | >MOTOR MANAGEMENT |
MOTOR MANAGEMENT
26 September 2012
Poorly specified, installed and maintained belt drives can operate well below optimum efficiency – but the message from the ERIKS Drives and Power Transmissions ore Competence Centre is that by following a few simple steps you can maximise the performance of your drives
Despite the fact that belt drives are found in approximately one third of applications in the industrial and commercial sectors, these devices are often inefficiently run. Perhaps the fact that these are familiar components in parts such as fans, pumps, blowers and conveyors has led to a lack of attention when it comes to system design, installation and maintenance but,
whatever the cause of this inefficiency, engineers can optimise their drives by understanding why these devices fail and how to avoid a few common problems. First, let’s look at installation. The most common causes of ineffectiveness in belt drives are creep, hysteresis, friction energy loss, pulley misalignment, pulley groove wear and incorrect tensioning. Let’s be clear about the meaning of each of these terms. The first, creep, describes the change in length between the tight and slack sides of the belt as its surface moves across a pulley, a condition that occurs as torque tension in the belt changes when the drive is set in motion. Hysteresis and frictional energy loss can be described together, since measurements of both these factors are calculated where energy has been converted into heat. As the belt bends and straightens, in particular where the belt enters or exits a pulley groove, hysteresis energy is converted into heat owing to the finite damping energy ratio of the materials from which the belts are made.
PULLEY MISALIGNMENT
Pulley misalignment is selfexplanatory but pulley groove wear is not always fully understood. Pulley groove wear results from incorrect tensioning, which allows friction belt drives to slip; the resulting friction results in heat build-up and a secondary curing process of the belt. As the parent rubber material becomes extremely hard, the belt wears the vee groove form out of shape. This means that, even if the worn belt is then replaced, the new belt sits in a groove that is essentially "U” shaped and, since the belt now has only point of contact with the groove, the drive does not transmit its rated power at its full efficiency. As a result of these potential problems, a series of solutions have been devised to provide long-lasting, efficient, resilient performance in typical applications. Among the solutions are wedge belts, Cogged Raw Edge (CRE) belts and Synchronous belt drives. A wedge belt offers an efficiency of around 93% at installation, while Cogged Raw Edge (CRE) belts offer 94%. Synchronous belt drives such as the Fenner Torque Drive Plus 3 (TDP3) can deliver 96% efficiency maintained over a wide load range.
The high tooth shear resistance and exceptional tensile strength of the Synchrochain synchronous drive belt delivers reliable power transmission even when dealing with high-power requirements, where high speeds can be reached under high dynamic load at up to 40m/sec with a peak efficiency of 96%. Aside from installation and replacement solutions, engineers can also make changes to their maintenance regime that will make a marked improvement to drive efficiency. For example, incorrect tensioning can be avoided via the use of a belt tension gauge, while pulley groove gauges and drive alignment lasers can ensure accurate alignment, improving performance and minimising maintenance and repair costs.
ENERGY SAVINGS
Finally, a word on energy.
There are inherent losses with all belt drives, whether friction or synchronous,
and energy can only truly be saved by switching plant off or by slowing it
down. Even with the most well specified, installed and maintained equipment, real
savings can only be achieved by using a belt drive in conjunction with a
variable speed drive. This will have the added benefit of reducing shock
loading on belts with features such as ‘soft start’, minimising both
maintenance and operating costs as well as saving on energy.
Key Points
- The most common causes of ineffectiveness in belt drives are creep, hysteresis, friction energy loss, pulley misalignment, pulley groove wear and incorrect tensioning
- Energy savings can be achieved by using a belt drive in conjunction with a variable speed drive
- ERIKS appointed certified SKF gearbox rebuilder
- Reduced belt elongation
- Eriks and Festo celebrate 25 years
- Digital replenishment App
- Controlling the Pitch and Yaw of the gearbox landscape
- Conditioning monitoring tactics risk hampering industry warning
- ERIKS welcomes first apprentices
- Guide to enhancing MRO efficiency
- UK 'badly underprepared' for Industry 4.0
- Engineering stores efficiency survey
- Schaefler Brakes World Record
- HTQ DRIVE TECHNOLOGY
- Laser Distance Measurement
- EXTERNAL COOLING & LUBRICATION SYSTEM
- As Long As The Wind Blows
- Back-Up Drive Equipment
- Updated Installation Guide
- Rossi Gear Motors Ltd drive towards automation
- Servo Drive KEB COMBIVERT F5 Multi
- Perfect mounting on both sides