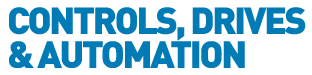
![]() |
Charlotte Stonestreet
Managing Editor |
Home> | POWER TRANSMISSION | >Gearboxes | >Prevention is better than cure |
Prevention is better than cure
09 January 2015
When equipment fails, often the biggest concern is how to get it running again. However, equally as important is discovering the root cause and how it can be prevented in the future. Here, Simon Whitehouse, head of the Gearbox Repair Division at Eriks UK, highlights the key causes of gearbox failure and how they can be avoided
Preventive maintenance is defined as the regular performance of equipment maintenance practices in order to avoid future equipment problems. Therefore, an important first step in any preventive maintenance program is learning to identify the causes of equipment failure.
By providing managers and service technicians with the knowledge to identify key causes of gearbox failure, a crucial link in the power transmission chain, they can establish an effective preventative maintenance program to support their plant / site operations.
Lubrication
Effective lubrication is extremely critical to all gearboxes and will help prevent gear and bearing failures. Many internal gear and bearing failures result from insufficient or interrupted lubrication to the drive train.
Maintaining lubrication to any gearbox includes not only selecting the appropriate solution, but also keeping oil clean and free of foreign materials, whilst maintaining a sufficient supply of lubricant to all of the internal operating components.
When lubrication problems occur, they can cause several gearing issues. Failures, like scoring and spalling, are generally caused by oil film breakdown resulting in metal-to-metal contact, and high temperatures resulting in tooth surface damage and wear. If a gear continues to operate without adequate lubrication, damage will progress until the gear’s tooth profiles are degraded to the point where replacement is the only option available.
Since selecting a lubricant is based on many independent factors including gear type and style, load type, speed, operating temperatures, input power and reduction ratio – choosing a lubricant should be left up to a gear lubrication specialist or the Original Equipment Manufacturer to advise and provide guidance.
This is especially true considering the technical sophistication found in gearing today, along with increased speeds and loads, and the specialised lubricants and additives now available in the market place.
Vibration
Vibration is another key indicator in the diagnosis of gearbox faults. Each fault generates a specific vibration profile, and a single vibration measurement provides information concerning multiple components.
By analysing vibration, engineers are able to determine whether the cause of the machine fault is an imbalance, misalignment, general loss of interference fits or wear, bearing defects, gear defects, or some other unforeseen problem.
Left alone, any of these gearbox faults can do enough damage to necessitate shutting down a piece of process equipment making vibration analysis even more important.
While identifying the cause of gearbox failure can sometimes be as simple as looking closely at the damage, discovering the root cause of such a problem is often considerably more difficult.
Not all companies have the sophisticated equipment needed to identify vibration anomalies or analyse oil samples for foreign materials. Without these resources, how then can they establish a preventive maintenance program?
Outsourcing preventive maintenance functions to an outside service provider, such as ERIKS, is certainly an option. Outsourcing these duties allows companies to focus on their own core competencies, letting specialists with access to both a strong knowledge base and a wide range of necessary equipment, handle maintenance and repair duties.
Any good preventive maintenance contract should include a quality repair/overhaul with dependable warranty on all gearboxes serviced and, or repaired. As important to any warranty is the proper installation and setup of a gearbox, which can promise years of trouble-free operation, if adequate preventive maintenance procedures are performed.
While identifying the cause of gearbox failure is only the first step in establishing an overall preventive maintenance program, it is an important step. The information gathered will ultimately serve as the foundation for planning future preventive maintenance programmes - a particular necessity when working with critical equipment. Such information will help service technicians avoid making common same mistakes, which can promise years of trouble-free operation.
Key Points
- An important first step in any preventive maintenance program is learning to identify the causes of equipment failure
- Effective lubrication is extremely critical to all gearboxes and will help prevent gear and bearing failures
- By analysing vibration, engineers are able to determine the cause of the machine fault
- ERIKS welcomes first apprentices
- Top tips to keep your belts in business
- Conditioning monitoring tactics risk hampering industry warning
- HEALTH & RECOVERY
- Controlling the Pitch and Yaw of the gearbox landscape
- £5000 Engineering Challenge competition
- Servicing the invisible customer
- COOL, CALCULATED EFFICIENCY
- Hose Technology Centre gets upgrade
- Reduced belt elongation
- GEARBOX IS CHEAPER TO REPLACE THAN REPAIR
- PLANETARY/SPUR GEARBOXES
- PLANETARY GEARS WELL SUITED FOR RETROFIT
- AGEING WORM GEARS REPLACED BY PLANETARY GEARS IN SEWAGE PLANT
- REHFUSS BRINGS QUALITY AND VERSATILITY TO GEARBOX DESIGN AND SELECTION
- FLEXIBLE COUPLINGS
- GETTING THE BEST OUT OF GEARBOXES
- A Guide to the Selection
- Greater Corrosion Resistance
- Fits existing parameters