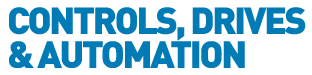
![]() |
Charlotte Stonestreet
Managing Editor |
Home> | AUTOMATION | >Handling & Logistics | >Advanced dynamics |
Advanced dynamics
01 January 2017
Festo’s new handling system, the EXCT handler, delivers 30% higher performance than traditional gantry systems. It provides advanced dynamic positioning and motion control in pick and place and assembly applications.
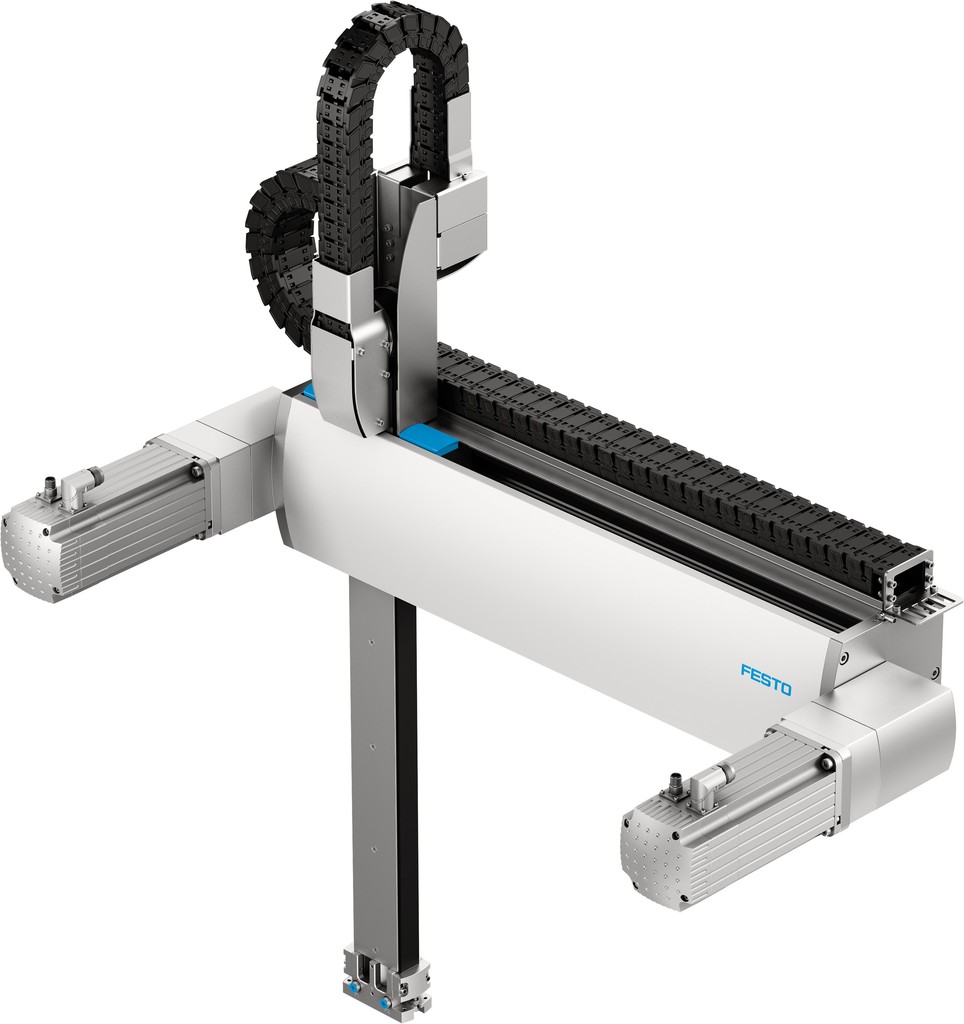
The EXCT handler is a 2-axis linear gantry that uses parallel kinematic principles to deliver excellent dynamic movement in the vertical and horizontal axis. A single belt, which is driven by two motors runs throughout the system, making it more efficient than typical T-shaped gantries that have two separately operated axis, one each on the y-axis and z-axis. Higher loads can be transported with a high dynamic response, as the two motors are stationary and not transported as part of the system. As a result it can deliver precision positioning with higher acceleration and torque, as well as minimal vibration.
There are three standard load variants covering loads of up to 10 kg on the z-axis. On average the EXCT handler achieves 90 picks per minute traveling at a velocity of 5m/s with an acceleration of 50 m/s2. The EXCT is constructed from tried and tested standard Festo parts and linear axis to deliver high quality performance, fit for price. As such it can be assembled easily with parts being ordered ‘off-the-shelf’ which reduces time to machine design and installation.
“At Festo we are constantly looking at how we can better support our customers and identified a need for a handling system which had a higher load capacity than tripod systems, but that could carry loads faster than H-gantries,” says Warren Harvard, product manager at Festo. “The EXCT fits this gap perfectly. It is a flexible compact design solution with an excellent dynamic response and cycle times.”
“In minimising the cable chain and in turn reducing the head moving mass, 30% higher performance then standard gantry systems can be achieved.”
The system is suitable for use in a variety of applications including pick and place, packing and filling as well as orientation tasks. It features common Festo drive technology and can be controlled using a multi axes controller in combination with either a conventional sensor or vision systems to identify the products. It can also connect with a range of grippers and attachments.
- Festo extends reach of VTUG and MPA-L valve terminals
- Food safe valve terminal
- Servo drive developer kit
- Future perfect form
- Festo celebrates centenary
- Cost effective quality
- Save costs when selecting process valve solutions
- Supporting the workforce of the future
- Handling solutions in 20 minutes
- Festo tech aids Notre-Dame restoration