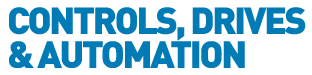
![]() |
Charlotte Stonestreet
Managing Editor |
Ensuring automated machinery meets safety standards
15 May 2017
The combination of social developments and technological progress has had a profound impact on legislation and regulations for automated machinery. David Barrett-Hague, product marketing manager, industry business at Schneider Electric, reports
Safety has become a key issue for businesses and there’s a renewed onus on plant operators and manufacturers to take preventative action to preserve and protect the quality of industrial environments and the safety of staff, in line with European Directives.
However, doing so creates two challenges: selecting machinery that meets an adequate level of safety for compliance and ensuring teams have sufficient safety application knowledge. For machine builders to become more confident in their ability to construct safe, compliant and efficient machines, they must consider several steps.
Remember to risk assess
Risk assessments are a critical piece of the puzzle for meeting the necessary standards. While National, European and International directives offer guidance in the subject and specify general principles, they don’t always give a framework for what steps should be taken in every case. For example, the risks that might be reasonable in a plant employing skilled workers might be unacceptable in an environment where members of the public might be present. If safety approved equipment is bought but is then placed into a new process or a new setting, it may not be secure any more. A new safety assessment must be carried out. When undertaking this, organisations must understand these nuances and:
- Identify the limits and potential hazards of the machinery
- Ascertain who is at risk of harm by the hazards identified
- Prioritise the risks in order of severity and potential for harm
Engineers must seek support from dedicated risk managers to build a customised strategy based on assessments of the organisation’s unique risk tolerance. These strategies can then be executed using best practices, strong governance and sound reporting strategies.
In addition to developing internal expertise, it is often beneficial to engage third party risk accessors, not just for their industry wide experience but to provide an independent and holistic perspective.
Eliminate risks in the design phase
Beyond risk reduction, elimination can sometimes be achieved by removing hazards as part of an inherently safer design. Automating tasks such as machine loading can eliminate some risks. However, businesses should also make sure that they don’t end up substituting one hazard for another. For example, air-powered tools may provide a safer environment than dealing with electricity, but they can introduce other hazards from the use of compressed air.
Where inherently safe design is not practicable, safeguarding is the next best step to prevent people encountering hazards. This can include fixed guarding, interlocked guarding, and presence sensing to prevent unexpected machine start-up. This helps facilitate an industrial environment where safety is at the centre of all operations.
Create a safety culture
While the issue of machine and plant safety continues to evolve, OEMs and end users alike face several big decisions as they juggle the need to keep people safe, with the pressure to create an optimal and productive operating environment.
In fact, there is still work to be done in establishing a culture where safety and risk management are at the core of day-today operations. Industry the world over must invest not only in practical safety measures but also in education, to ensure employees are aware of the risks. Safety is largely seen by organisations as bolt-on and something that is reactive, rather than proactive. At a product level, safety components are starting to be built in but this should apply to employee mentality too.
Combining thorough risk assessments and safeguarding practices with employee training and the latest technology, goes a long way to ensure better performance and protection of the industrial environment and those that work in it.
Key Points
- Directives offer guidance in the subject and specify general principles, but don’t always give a framework for what steps should be taken
- If safety approved equipment is bought but is then placed into a new process or a new setting, it may not be secure any more
- Where inherently safe design is not practicable, safeguarding is the next best step to prevent people encountering hazards
- Powering a new breed of building
- Schneider & Cisco partner to bridge OT/IT in building management systems
- Primary Engineer programme in partnership with Schneider Electric
- Schneider Electric acquires Itris Automation Square SAS
- Scoring sustainability goals
- Digital transformation brings productivity gains
- Corporate Knights names Schneider Electric most sustainable corporation in Europe
- Joint initiative to drive industrial digital transformation
- Scaling up for success
- Ultra compact SCARA robot
- No related articles listed