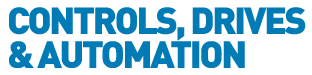
![]() |
Charlotte Stonestreet
Managing Editor |
Home> | INDUSTRY FOCUSES | >Manufacturing | >Sustainability transformation in manufacturing |
Editor's Pick
Sustainability transformation in manufacturing
10 July 2022
A NEW report from Schneider Electric and MIT Technology Review reveals a concerted push towards sustainability within the manufacturing sector, with a long-term goal of total carbon visibility across the entire supply chain.
The joint research, entitled ‘Equipment management and sustainability’, reveals that leading manufacturers are shifting to making sustainability the goal of process improvements rather than merely a by-product of responsible equipment management.
Key takeaways from the report include:
- Product-specific sustainability practices on the rise
Leading firms are modernising processes to enable decarbonisation. This is achieved by improving equipment operations, reducing waste, and making products with less carbon-intensive inputs.
The report suggests that manufacturers are seeking increased access to visibility through data analytics and digitally connected supply chains. Embracing Industry 4.0 principles, manufacturers are using sensors and performance management tools to increase the flow of carbon/sustainability-relevant data across the firm’s entire operations.
- Modular processes enabling better predictions
Technology is also being used to build better predictive processes and reorganise them to be leaner and modular.
It allows producers to adjust assembly lines, processes, and material inputs for more precise calibration. In turn, this allows for better forecasting and ‘on demand’ customised manufacturing.
Organisations can now use virtual designs to stress-test new sustainability production models in virtual reality before committing them to the carbon intensive ‘physical’ reality, such as digital twinning to reduce energy in production design processes.
- Purposeful design aids the circular economy
Leading manufacturing firms are reimagining manufacturing processes in pursuit of ‘circular economy’ goals. This often involves a long-term business plan for managing materials and ‘design for sustainability’ manufacturing principles.
These include building facilities to disassemble existing products to make better use of spare parts and total cost of ownership (TCO) models, which link product design to fewer processes, more sustainable inputs, and even reducing the lifespan of machinery-intensive products to take advantage of iterative innovations in electric efficiency.
Frédéric Godemel, EVP of power systems and services at Schneider Electric, said: “Manufacturing is transitioning from incidental to intentional sustainability, according to this new report. Sustainability is no longer a happy coincidence; now, the illustrious pairing of efficient equipment management and purposeful green principles sees manufacturing set on a course for effective decarbonisation in the long term.
“That being said, the time we have to decarbonise is swiftly dwindling. Manufacturers must accelerate their efforts through optimal use of data and digital technologies if the industry is to make a significant contribution to international climate goals when it matters.”
To discover more about how global businesses use insight and innovation to make their manufacturing processes and assets carbon neutral, please see the report “Equipment management and sustainability: How global businesses use insight and innovation to make their manufacturing processes and assets carbon neutral”, which is available now.
- Industry urged to enhance cybersecurity practices
- Schneider Electric acquires Itris Automation Square SAS
- Innovation in Sustainability win
- Schneider Electric name PWR as first Master Robot Partner
- Industrial automation architecture evolution
- Powering a new breed of building
- Ultra compact SCARA robot
- Merging HMIs & PLCs into a single unit
- Schneider & AVEVA give Flint factory digital upgrade
- Using robotics to drive productivity
- EMC Centre Of Excellence
- Online Customer Support Centre
- INTEGRATING MOTORS INTO MACHINE DESIGNS
- DIAS Drives
- Industry in freefall as Coronavirus hammers manufacturers
- ‘Just in time’ replaced by ‘just in case’
- Clock ticking on energy impact
- NatWest Group to lend additional £1b to support net zero
- Manufacturers enter 2024 with increased optimism
- Drives & Controls joins Smart Manufacturing & Engineering Week