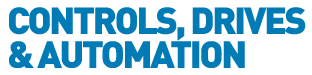
![]() |
Charlotte Stonestreet
Managing Editor |
Bridging the drive-servomotor gap
15 January 2018
Most ways to operate motors without an encoder have a serious disadvantage: in the range from zero to around 100 revolutions per minute, the rotor does not provide signals that can be evaluated. Andy Pye reports on the LeanMotor, which took centre stage for Stöber at the November 2017 SPS IPC Drives show. It is available from the start of 2018.
Over 90% of the motors used in the world are asynchronous motors (aka induction motors) and they have many and diverse applications - centrifugal fans, blowers and pumps; compressors; conveyors; lifts; heavy duty cranes; lathe machines; mills. But, the speed of an asynchronous motor (aka induction motor) reduces with the increase in the load.
Synchronous motors, run at a constant speed at a given frequency irrespective of the load, are usually more expensive and complicated in comparison. Hence they are only used when low or ultra-low speed performance is required by a machine.
Now, German drives specialist Stöber is launching a highly efficient and compact electric drive that has the same output as an asynchronous motor while being significantly lighter, more compact and energy-efficient. It is aimed at engineers looking for a more cost-effective and better performing replacement for an AC motor, yet do not require a high specification servo drive.
While most common synchronous servomotors use surface mount magnets, the LeanMotor has internal permanent magnets. A rotor with interleaved magnetic lamination and non-magnetic spacers will exhibit anisotropy – anisotropy is directional dependency of physical properties – this enables the position of the rotor to be determined without a positioning encoder. With the LeanMotor, the position of the rotor can be determined accurately by exploiting the anisotropy of the rotor, and thus speed and torque can be set to any value from stationary to maximum speed with full torque control. The fluctuation in speed is said to be less than 1% of the nominal speed.
More rugged
The LeanMotor has no electronics installed in the motor, and so is also more rugged and cost-efficient than a servo drive. This means it can be used for dynamic tasks in harsh environments and suitable for exposure to high levels of vibration. Its fanless construction, means it is smaller than comparable drives and with a single power connection, is very easy to fit. Because of its lower flywheel mass, the motor can also be controlled more dynamically and efficiently than a combination of an asynchronous motor and incremental encoder.
Target applications for the new motor include precision positioning as well as packaging, paper-making and pump drives. If the LeanMotor is installed instead of asynchronous motors on applications such as the guide slide of multi-axis machining tools, the movable load is greatly reduced. Engineers are able to design smaller drives in this case and users save energy and reduce the costs for the components. Up to 30% improvement in cost-efficiency is possible in some applications.
The LeanMotor exceeds the IE4 efficiency level with an efficiency of up to 96%. Asynchronous motors usually only achieve similar efficiency by using more or higher quality materials, like copper; as a result, they end up being significantly larger and heavier.
For this concept to work, a drive controller needs to understand the anisotropic properties of the motor. The LeanMotor can therefore be used only with Stöber’s SC6 or SI6 drive controls. It is not suitable for use with third party drives controllers, nor are motors with hollow shafts possible. The LeanMotor can, however, be integrated with a wide range of Stöber gear units and accessories, such as a rugged spring-loaded holding brake.
Key Points
- Stöber LeanMotor is an efficient and compact electric drive that has the same output as an asynchronous motor while being significantly lighter, more compact and energy-efficient
- The LeanMotor has no electronics installed in the motor, and so is also more rugged and cost-efficient than a servo drive
- Target applications include precision positioning as well as packaging, paper-making and pump drives
- Unwind, wind and rewind with precision
- Stober collaborates in drive to make mobile ventilators
- More efficient planetary gear unit design
- More processing power
- STOBER strengthens global presence
- High power supply for multi-axis drive systems
- Energy-saving modular drive
- Enhanced predictive maintenance
- New LeanMotor from STOBER Drives
- STÖBER provides servo ball screw motors
- No related articles listed