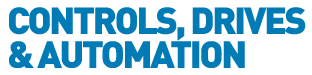
![]() |
Charlotte Stonestreet
Managing Editor |
Home> | AUTOMATION | >Encoders | >Fully-programmable hygienic encoders |
Fully-programmable hygienic encoders
30 January 2018
SICK has launched stainless steel versions of its fully-programmable DFS60 incremental encoders and AFM60 and AFS60 absolute encoders making them available for duties in hygienic and corrosive environments for the first time.
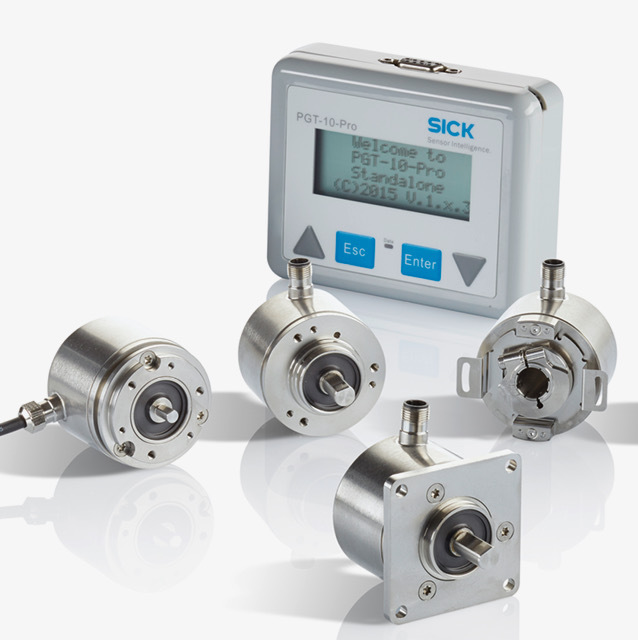
The SICK DFS60 Inox, the AFM60 Inox and the AFS60 Inox programmable encoders feature a rugged stainless steel housing, flange and shaft. They deliver high-resolution, precision performance in aggressive environments such as chemical washdown, salt and high humidity atmospheres with an operating temperature range from -30°C to +85°C.
The SICK DFS60 Inox is a high-resolution, 16-bit incremental encoder, the AFS60 Inox absolute single turn encoder has a high resolution of 18 bits, while the AFM60 Inox absolute multi-turn encoder has an even higher resolution of 30 bits. With a compact housing for easy mounting in tight spaces, each encoder is available with a square or round flange and solid or blind hollow shaft to match the application specifications.
Explains Darren Pratt, SICK’s UK Product Manager for encoders. “High-resolution programmable encoders have revolutionised encoder use and now all the advantages of precision and customisation are available in Inox models where high resistance is needed in aggressive or corrosive environments.
“SICK DFS60 Inox, AFM60 Inox and AFS60 Inox users can program the encoder to match numerous operational parameters instead of having just one specified task per model. As a result, customers can reduce their encoder inventories dramatically. Programmability also enables rapid replacement of legacy fixed-parameter encoders without expensive downtime waiting for exact spares.”
The SICK DFS60 Inox incremental encoders are suitable for high-precision measurement of rotating shaft speed, angle and position for a wide variety of tasks including electric motor feedback, automated pick and place or robotic arm control.
The AFM60 Inox and AFS60 Inox provide highly-accurate absolute positioning, eliminating the need for time consuming and costly axis referencing following a power cycle. Variants of the AFM60 and AFS60 with combined absolute and incremental feedback are also available which enable perfect speed and absolute position-control from the same device.
Configuration, teach-in, programming and reprogramming of the SICK DFS60 Inox incremental encoders, and AFM60 Inox and AFS60 Inox absolute encoders are simple and intuitive, either directly on the device using the SICK handheld PGT-10-Pro tool or using a PC, the free to download SOPAS configuration software and the PGT-08-S (SOPAS interface unit).
The range of options for programming the electrical parameters – such as the output signal level, the number of pulses per revolution, zero pulse width, counting direction and pre-set values enables the user to tailor the encoder perfectly to the application requirements. Each Inox encoder is available with a choice of electrical interfaces and mechanical connections to suit different customer specifications.
- Next generation of safety light curtains
- How SICK robot safety enables machine tending on wheels
- Switch for food & beverage sector
- Bespoke Vision Sensor Packages
- Hygienic sensing systems
- Brings live sensor data to the Cloud
- Compact mid-range safety controller
- 3D LiDAR navigation and collision avoidance
- Motion Control
- Get Your 15 Minutes