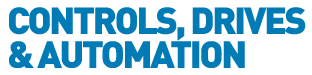
![]() |
Charlotte Stonestreet
Managing Editor |
Robotic paradigm for increased production
02 February 2018
To meet demand on labour-intensive products, speaker manufacturer, Paradigm has implemented Universal Robots (UR) in polishing applications, resulting in significantly increased production throughput and eliminating bottle necks while improving the work environment
When Paradigm Electronics launched the “Midnight Cherry” finish on a line of new speakers, the market quickly embraced the new product made entirely in-house.
The director of operations said: “In order to produce that finish, you have to apply multiple layers of lacquer and between each layered application, you have to sand and buff, sand and buff. There’s a lot of manual labour involved in that. The problem is to find people who can do that, we just couldn’t find enough skilled people.”
Paradigm looked to robotics as a solution as the company had already implemented one robotic cell with a cartesian type robot. The cartesian robot required a lot of protective devices around it for the safety of the worker. It really didn’t allow for an employee to work in conjunction with the robot at all. The application of buffing is one that requires a lot of observation and collaboration by the operator, so having the work being done in a remote cell just didn’t seem to be a workable solution.
An industry expert introduced Universal Robots as an ideal solution. UR robots are a new type of robot classified as collaborative due to their interactive design making it easy to set them up for a new task as well as their built-in safety system enabling the robot arm to automatically stop operating if it encounters objects or people in its path. At Paradigm, the UR10 handles the most strenuous part of the polishing, using the coarsest buffing compounds where after the last phases, if needed, are manually applied using a higher grit compound.
Safe interaction
“Collaborative robots was a new technology. This kind of robot allowed us to have a human and a robot working in the same workspace. They’re now working in a pendulum type of operation where they can safely interact, allowing the human to check whether the robot has done an adequate amount of work before the final polishing is handed over to the human. It’s a very hand-in-hand kind of operation between the two,” continued the company representative.
The implementation solved Paradigm’s back log on the popular cabinets by increasing throughput by 50%. “Once we realised that a collaborative robot was a viable alternative for us, we did our homework and checked around the rest of the opportunities that were out there from different manufacturers and we found that for our application, the UR robot was not only the best robot for the application, but it was also the most cost-efficient and a return of investment estimated to be about 14 months.”
For the loudspeaker manufacturer, it was also imperative that the robot would be able to perform the polishing applying a specific force.
“The robot has taken over a really delicate job, you just make one wrong move with the sandpaper and you leave a mark on the cabinet that cannot be repaired. So a robot has to be as delicate and as sensitive as a human, pressure has to be applied properly.” The UR robots have a built-in, adjustable force mode feature that is easily pre-programmed for specific applications.
“If too much force is applied, the surface heats and the results go the opposite direction. Having the ability for the robot to work to a specific force was a huge advantage. We were aware of technologies that allowed for a force feedback system but they were actually as expensive as the entire UR robot was to us. So it was quite exciting to find that it had capabilities of force feedback within its inherent structure.” the company representative concluded.
Key Points
- UR collaborative robots have a built-in safety system so the robot arm automatically stops upon encountering an object or person
- Using a UR robot, speaker manufacturer, Paradigm eliminated a back log on its popular cabinets by increasing throughput by 50%
- The UR robots have a built-in, adjustable force mode feature that is easily pre-programmed for specific applications
- Cobots go from apps to caps
- Demystifying cobot safety
- Universal Robots sells 50,000th cobot
- Universal Robots launches new webinars
- “Man vs. Machine?” – A plea for rethinking their collaboration
- Teradyne to acquire Universal Robots
- Certified for cleanroom environments
- High double-digit growth at Universal Robots
- Universal Robots powers robotic kitchen
- A status report on the physical AI revolution
- No related articles listed