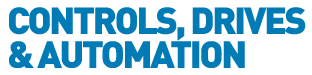
![]() |
Charlotte Stonestreet
Managing Editor |
Home> | CONTROLS | >PLCs | >A landscape of opportunities |
Home> | DRIVES & MOTORS | >Variable Speed Drives | >A landscape of opportunities |
A landscape of opportunities
18 April 2024
Charlotte Stonestreet sits down with Lee Turner, vice president of product and supplier management at Farnell to discuss trends and challenges in the world of industrial automation and control

CHARLOTTE STONESTREET: In the Industrial Automation and Control market, what role do variable speed drives play in optimising energy consumption and cost savings for industrial operations? Are they purely functional, an essential part of operations or a nice-to-have?
Lee Turner: Variable speed drives (VSDs) really are important products. According to the International Energy Agency (IEA), motors and the things they drive account for around 40% of the world’s electricity consumption. VSDs can cut the energy consumption by around a quarter and can deliver even greater savings if conventional motors are replaced by IE5 SynRM motor technology and a matching drive.
Only around a quarter of industrial motors are connected to a VSD according to supplier sources, so there is a huge opportunity to increase energy efficiency.
With energy costs likely to remain high, and the demands for industry to be more sustainable, energy efficiency is a huge concern for businesses and their CEOs. VSDs are just one way to reduce cost and improve an organization’s ESG credentials, but they are very easy to deploy and deliver significant benefits.
CS: What are the emerging trends in the Industrial Automation and Control market, particularly in the context of PLCs? Which trends are most likely to shape the future of manufacturing and industrial processes?
LT: The PLC is not a new technology. Dick Morley invented the first PLC, the Modicon 084, for General Motors way back in 1968. You might think that this is mature technology that doesn’t really change, but this is far from the truth.
The improvement in processor performance has allowed the PLC to develop so that it offers far greater functionality than could have been envisioned at the end of the 1960s. Other technologies, most recently the IoT revolution have made demands for more capabilities within the PLC.
Today the PLC is not a simple replacement for relay-based control as it was in the 1960s. PLCs are complex components that underpin the connected factory. Communications and remote access are increasingly used, which in turn require cybersecurity solutions for protection. Although ladder programming is still used, increasing levels of sophistication are being added to PLCs. For example, we see AI/Machine Learning becoming a key feature, enabling the PLC to run predictive maintenance algorithms and improve plant uptime.
CS: What is the impact of Industry 4.0 on the Industrial Automation and Control market? Is Industry 4.0 a “thing” or, as some have said, more of a handy catchall term? In either case, is its emergence the primary force that is driving the development and adoption of smart technologies, or are there other influences in play?
LT: Without doubt, industry 4.0 is having a huge impact on the automation and control market. In practice, it’s hard to fully adopt industry 4.0 in its entirety, particularly on brownfield sites. The philosophy of industry 4.0, in particular the importance of data and the use of automation, define a trend that is having an impact on the way almost every industrial plant in the world is managed.
CS: What roles do advanced data analytics and predictive maintenance play in enhancing the efficiency and reliability of Industrial Automation and Control systems?
LT: Collecting and analysing data is a crucial part of any modern automation system. Without the advanced analytics, processes can’t be fully optimized. Typically, these analytics require data to be uploaded to the cloud where algorithms look for ways to improve performance.
Predictive maintenance is really a subset of data analytics. However predictive maintenance is increasingly performed locally, with sensor data processed on-site. The advent of AI has made it simpler to deploy processing locally, allowing the plant to take control of predictive maintenance. As companies recognise the benefits of this approach, we are seeing a rapid increase in demand for our sensor products which gather data – particularly vibration data – that can be processed to identify which items of plant are wearing or likely to fail.
CS: Can you provide insights into the evolving regulations and standards that currently govern the Industrial Automation and Control market?
LT: Regulations to promote efficiency in technology change and evolve, regularly requiring products from PLCs to VSDs to be updated. However, industrial automation and control system regulations are not quite as stringent as regulations that promote energy use and sustainability. Companies, particularly heavy industries, are not only being pressured by customers to be more sustainable, they are also compelled to respond to environmental legislation. The EU’s Corporate Sustainability
Reporting Directive (CSRD) regulations will come into force in 2025, requiring over 11,000 companies to report their greenhouse gas emissions, and other legislation will inevitably follow around the world.
As requirements for reporting the environmental impact of the business increase, companies’ reputations will be impacted by their energy efficiency. It’s almost inevitable that these regulations will drive a greater use of automation and energy-efficient technologies such as VSDs as companies scramble to protect their reputations and demonstrate a commitment to sustainability.
CS: What key challenges do companies face when implementing Industrial Automation and Control solutions?
LT: There are a huge number of challenges in implementing modern automation and control solutions because of the complexity. You need to have systems to gather and process huge volumes of data, as well as deploying complex automation solutions. This requires experts to design and build these systems.
Once the systems are deployed, companies rely on them. Although automation and IoT products are very reliable, the number of sensors, controllers, drives and other products means that failures do happen. Being able to source replacement parts quickly is vital to minimise downtime, and this is where a partner like Farnell comes in. We are able to deliver spares and replacements quickly and efficiently, something that is going to be ever-more important as automation becomes even more complex.
- Simple & reliable USB connectivity
- Supporting engineers in their IIoT journey
- Farnell launches fourth global IoT survey
- Farnell to exhibit with Festo & Omega at Manufacturing Expo
- Farnell releases results from inaugural Buyer Survey
- CTS products available for same day dispatch from Farnell
- Single Pair Ethernet campaign
- Arduino UNO R4 available from Farnell
- Smart sensors whitepaper
- Farnell boosts e-mobility power portfolio
- PUMPED UP PERFORMANCE
- FANLESS COMPACT PC CONTROL
- TOO MUCH CONTROL PANEL HARD WIRING
- SOFT STARTER OR VARIABLE SPEED DRIVE?
- Jeans With Less Energy
- Shop Floor To Top Floor Connectivity
- MID-RANGE PLC BRIDGES THE PERFORMANCE GAP
- Enhanced to Withstand Tough Environments
- Low Cost, multi-Function PLC
- Smartwire-DT Gets Smarter