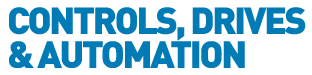
![]() |
Charlotte Stonestreet
Managing Editor |
Home> | DRIVES & MOTORS | >Variable Speed Drives | >SOFT STARTER OR VARIABLE SPEED DRIVE? |
SOFT STARTER OR VARIABLE SPEED DRIVE?
12 October 2012
Energy optimising soft starters have received mixed reviews, partly due to a lack of understanding of their capabilities, coupled with some over-selling on the part of a few commercial suppliers. But in the right circumstances, is it time to take another look?
When working at or near full load, the typical three-phase induction motor is relatively efficient, achieving efficiencies of 80% to 95%. However, efficiency falls dramatically when the load falls to less than 50% of rated output. Very few motors actually experience consistent fully rated operation and most operate at much lower loads either due to over-sizing (a very frequent situation), or natural load variations.
In fan and pumping, power is proportional to the cube of the shaft speed. Therefore an inverter drive will produce considerable energy savings over virtually all other methods of control through varying the speed of the motor in response to changes in load. However, inverter drives are expensive and complex and will consume 5 to 8% of the power consumption of the motor being controlled.
Where varying the speed is not required, an inverter drive is effectively an expensive soft starter. Inverter drives also generate potentially disruptive harmonics which require suppression.
The majority of electric motors are running fixed-speed applications, and an alternative is a voltage optimising version of semiconductor motor controller – an enhanced electronic soft starter. These units can save energy where the loading is less than 50%. Less sophisticated soft start systems will remain at full conduction, and the motor then behaves as if it were connected directly to the mains supply. However, at light loads and mains voltages, induction motors always have excess magnetic flux and suffer efficiency loss and power factor degradation as a result. By detecting the load at any instant and adjusting the motor terminal voltage accordingly, it is possible to save some of the excitation energy and load loss and improve motor power factor when the motor is running inefficiently at loading levels below 50%.
NO INRUSH CURRENTS
The voltage optimising soft starters manufactured by Fairford Electronics are all microprocessor controlled. All calculations necessary to find the best degree of phase-back of the thyristors for any load condition are made by the integral microcomputer. Secondly, the start always synchronises with the supply voltage and a special sequence of turn-on pulses virtually eliminates inrush currents normally associated with motor start-up.
With the introduction of the energy optimising XFE Soft Starter, the Fairford System has gone a step further. These units incorporate an LCD display and keypad, programmable relays and various input/output options for control and diagnostics.
In reality there are only two algorithms for calculating the correct voltage, one which uses the motor power factor and the other which monitors the back EMF. Both of these techniques are covered by various patents and those held by Fairford Electronics relate to the power factor method.
The energy optimising mode is the default operating condition for a Fairford System XFE Soft Starter.While accelerating the motor in the ramp-up phase, the system software computes a reference value for the power factor of the motor being controlled and updates the firing points of the power thyristors so that the total energy delivered to the motor corresponds to that required by the load. By eliminating the waste of energy in over-fluxing the air gap the motor efficiency is improved and, simultaneously, the power factor of the motor is maintained at the best value possible for all load conditions.
The management of power factor by the Fairford System of control has absolutely no effect on the ability of the motor to respond to a fluctuating load demand.
Applications where energy optimising is beneficial are those where the motors are running for periods at below 50% loading or have been oversized for the load. Typical examples are injection moulding machines, large saws, crushers and grinders. For high inertia applications, care must be taken in the selection of the soft starter to ensure that it is capable of supporting extended starts. Further information: Report on Energy Optimising Soft Start Bench Trials – A RenewNet Project Conducted at the University of Edinburgh’s Institute of Energy Systems. Dr George B Grant, Optimal Energies, May 2011.
Key Points
- Three-phase induction motor efficiency falls when the load is less than 50% of rated output
- In fixed speed applications, an enhanced electronic soft starter can save energy
- PUMPED UP PERFORMANCE
- Jeans With Less Energy
- Enhanced to Withstand Tough Environments
- Savings From Improved Torque Ratio & Efficiency
- Modular VSD
- ENERGY SAVING: AN OLD MESSAGE WITH NEW PROMISE
- Updated installation guide for power drive systems
- UK drives manufacturer seals global automation deal
- WEG motors & drives power high-efficiency air blowers
- Powerful Savings