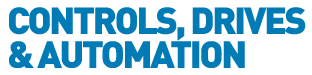
![]() |
Charlotte Stonestreet
Managing Editor |
Home> | AUTOMATION | >Handling & Logistics | >AMR offers increased safety & efficiency |
AMR offers increased safety & efficiency
05 July 2022
BOACH REXROTH'S new autonomous mobile robot, ActiveShuttle with Advanced Interaction brings more movement into intralogistics while increasing safety, efficiency and flexibility.

The camera-based 3D obstacle detection system even recognises objects protruding into the vehicle’s path and thus offers improved object protection. The new integrated touchscreen display allows individual configuration and quick fault management on the mobile robot itself. The updated AMS (ActiveShuttle Management System) control software communicates seamlessly with the shopfloor infrastructure and allows individual transport jobs with configurable job templates.
With the ActiveShuttle, intralogistics processes can be made highly flexible without having to change the factory infrastructure. The robust, plug & go ActiveShuttle transports dollies with small load carriers and a total load of up to 260 kg through factories in a fully automatic manner.
3D obstacle detection
The integrated personal protection system meets Performance Level (PL) d requirements as specified in EN ISO 13849-1. As a result, the new ActiveShuttle with Advanced Interaction can move freely around factories. In addition to the safety laser scanners, stereo depth cameras survey the room three-dimensionally. As a result, even objects protruding into the vehicle’s path either above or below the scan level are recognised. Consequently, the mobile robot can brake and avoid obstacles in real time. The improved recognition capabilities not only increase site protection – they also allow the system to be used in tight spaces, environments with obstructions or non-standardised environments with no defined floor areas.
Touchscreen display
The ActiveShuttle is geared to conventional supply principles such as cyclical transport or the consumption-based supply of materials. The new touchscreen display which is integrated into the vehicle console makes the system even more efficient. After all, the operating personnel can now interact directly and intuitively with the mobile robot. This ensures greater transparency thanks to job and status information, saves time when diagnosing and rectifying faults and makes boarding easier.
Thanks to the integrated VDA 5050-compatible communication interface, ActiveShuttles can be used anywhere. In practice, users already utilise them in conjunction with various VDA 5050-compatible management systems in intralogistics. With the ActiveShuttle Management System (AMS), Bosch Rexroth also offers a comprehensive piece of software for fleet and job management which now offers even greater degrees of freedom. In addition to simple transport movements from the source to the sink, complex work sequences too can now be created. For example, users can define reference trips or use advanced functions. When it comes to machine-to-machine communication, the ActiveShuttle can send signals to specific route points or only set off in response to a relevant signal.
Jobs are transferred to the ActiveShuttle either fully automatically from higher-level IT systems (MES, ERP etc.) or manually via the web-based operating interface with the help of a PC or tablet. The connection to the shopfloor infrastructure is being continuously improved with a view to connecting assembly and logistics seamlessly. Machines, robots and sensors (e.g. dash buttons) can communicate directly with the AMS via various standard interfaces and request replenishments if materials are running low for example.
- Report highlights maintenance failings
- Bosch Rexroth to acquire Elmo Motion Control
- Freedom & openness for everyone
- Failure to conduct oil checks 'major cause' of hydraulic failure
- Re-imagining machine configuration
- British engineers receive just five days training a year
- Industry 4.0 guidance platform
- Why Industry 4.0 is an evolution, not a revolution
- Cabinet-free drive technology
- Bosch Rexroth to take centre stage at Industry 4.0 conference