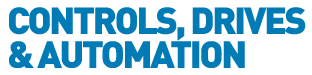
![]() |
Charlotte Stonestreet
Managing Editor |
Editor's Pick
Choosing a precision measurement sensor
14 October 2019
Advice from Turck Banner on the parameters which matter if a precision sensor is going to the job it is designed for
Quality control applications that require precise measurement can be challenging. Very tight tolerance requirements demand the ability to measure parts in microns to detect the smallest variations in part size, thickness, orientation, placement, etc. Ensuring parts meet strict quality standards can help reduce problems downstream and reduce the risk of product recall due to imperfect parts.
Laser measurement sensors are commonly used for precise part inspections. However, real world conditions introduce challenges for laser sensors that perform well in perfect laboratory conditions.
Resolution is traditionally the key specifications: it describes the smallest change in distance a sensor can detect. For precise applications, measurement in microns is essential. For example, in the semiconductor industry, very small IC chips must be fully seated in nests before being delivered to testing stations to ensure the integrity of the tests.
However, resolution does not provide the complete picture and sometimes overstates sensor performance. Typically, resolution is compromised by target conditions, sensor distance to the target, sensor response speed, and other external factors.
In discrete sensing applications, it is also important to consider repeatability (how reliably the sensor can repeat the same measurement in the same conditions) and minimum object separation (the minimum distance a target must be from the background to be reliably detected).
For analogue applications, it is important to consider both resolution and linearity (how closely the analogue output approximates a straight line across the measuring range) to ensure a reliable output across the full range of the sensor.
Objects may be very dark (low reflectivity), glossy (high reflectivity), or contain multiple colour transitions - all of which can significantly impact measurement reliability. To mitigate this, some laser measurement sensors feature automatic gain adjustment, which means the sensor dynamically reduces or increases its power based on the reflectivity of the target. This ensures targets of varying colours and reflectivity are all measured reliably. Another feature to look for in a precision measurement sensor is a small spot size, which minimises measurement variation across colour transitions.
Ambient temperature
Precision measurement can also be greatly affected by changes in ambient temperature. For some sensors, natural temperature fluctuations of even a few degrees can cause the sensor’s measurement error to double. Therefore, it is essential to choose a sensor with high thermal stability.
Another important factor is sensor configuration, because the movement of pushing buttons on a sensor can negate precision. Therefore, a precision measurement sensor must offer remote programming capabilities, such as including an IO‐Link, a remote input wire, and/or a remote sensor display. Some precision measurement sensors forego buttons entirely to ensure that precision cannot be accidentally compromised by maintenance staff.
Many precise quality inspections are also high‐speed applications. For these situations, users should look for a sensor with a fast, sub‐millisecond response speed and sampling rate to reliably identify errors on quickly moving parts, reduce inspection times, and increase machine throughput.
For example, in the automotive industry, engines and motors require many rotating components, such as crankshafts, to function properly. An uneven crankshaft impairs the balance of the motor and creates heat and vibration which can cause equipment to malfunction. To prevent future mechanical failure, a rigid runout tolerance must be set, and parts must be tested frequently for errors. This requires an extremely precise measurement solution of the quickly moving crankshaft. A sensor with a 0.5ms response speed and 0.25ms sampling rate can reliably measure targets at high speeds and rapidly identify problems.
Finally, mounting stability is crucial for a precision measurement sensor. Even with the best specifications, if a precision sensor isn’t mounted securely, measurements will not be reliable. To reduce the risk of measurement error, ensure that the sensor can be securely fastened to the mounting fixture and kept away from excessive vibration.
Key Points
- Real world conditions can introduce challenges for laser sensors that perform well in perfect laboratory conditions
- Resolution can be compromised by target conditions, sensor distance to the target, sensor response speed, and other external factors
- In discrete sensing applications it is important to consider repeatability and minimum object separation
- Sustainability through supply chain management
- Turck & Banner celebrate 50th anniversary
- Orchestrating a modular approach
- Shining a light on flexibility
- Distributor turns manufacturer
- Industrial connectivity - the past, present & future
- Seeing the light
- Thrills without the spills
- Seeing the light
- Immune to magnetic fields
- No related articles listed