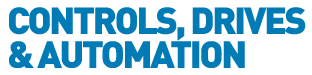
![]() |
Charlotte Stonestreet
Managing Editor |
Home> | MACHINE BUILDING & ENGINEERING | >Materials & Components | >Seeing the light |
Editor's Pick
Seeing the light
08 January 2015
Ground breaking developments attract many companies, quick to recognise a lucrative opportunity, with the result that the market gains rapid momentum. Such is the case with LED lighting, which has seen massive advancement in the last decade
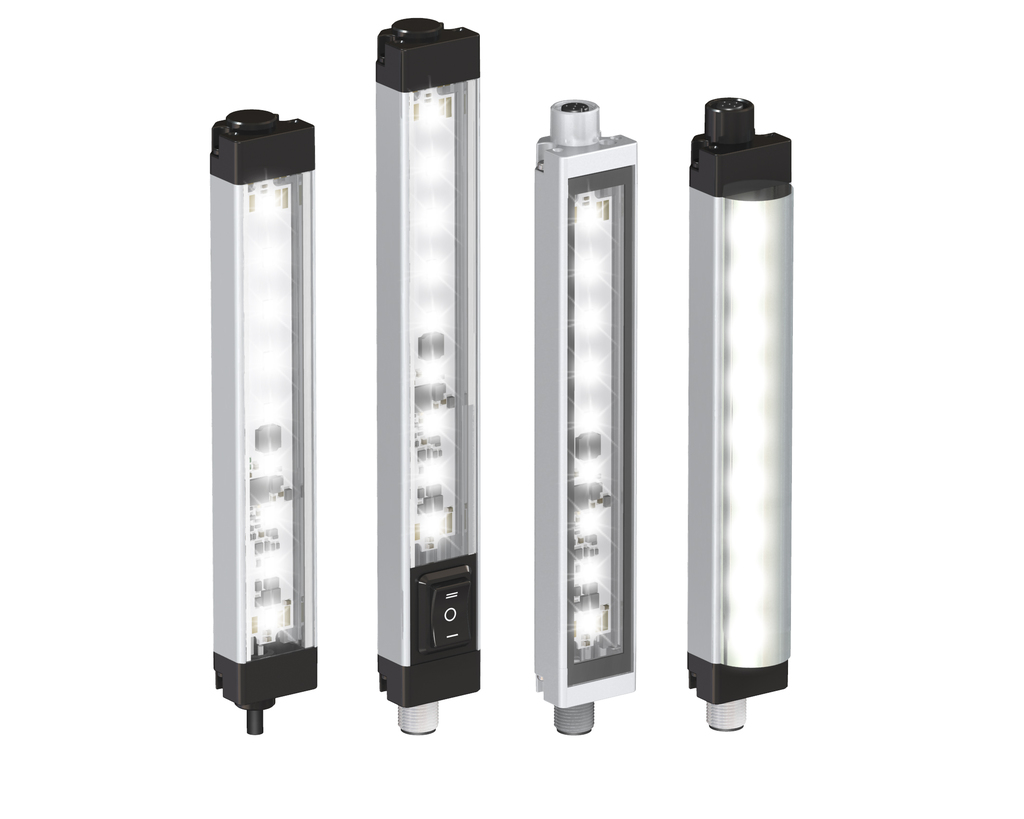
It was in the early 1960s that LEDs were first considered as a practical electronic component, and by 1970 the LED was seen as a real alternative to the incandescent light bulb in the production of photoelectric sensors. However, whilst offering long life and robustness, the main drawback was the extremely low light intensity of about 1% of a conventional bulb.
Throughout its history Turck Banner has worked on circuit development, in partnership with LED component manufacturers, to continually improve light intensity and performance at the same time maintaining reliability. This is perhaps best demonstrated in the production of photoelectric sensors for use in Ex hazardous areas, where the demand is for maximum light intensity using minimum power.
Industrial alternative
Having gained vast experience in the development of LEDs via the demands of photoelectric sensor technology, Turck Banner is well placed to contribute and compete in the ever expanding LED lighting market with its Lighting & Indicators division. Turck Banner offers a comprehensive range of task lights which provide an industrial alternative to fluorescent and halogen bulbs in enclosure, area and machine lighting, including control cabinets and panels. Several key additions to the range will be available shortly, including a twin fluorescent replacement unit designed for low/mid bay applications. The wide range of indicator lights includes signal tower lights, touch buttons and pick-to-light systems.
Energy efficient LEDs use as little as 10% of the energy of conventional lighting to illuminate the same area and, coupled with fittings designed for LEDs to maximise output, are far more efficient in directing light where required.
LED lighting from Turck Banner has a continuous working life in excess of 50,000 hours (that’s more than five and a half years). Beyond that they continue to function with no more than a 30% reduction in light output. Maintenance scheduling is therefore much easier, with no risk of being left in the dark. Compare this to a fluorescent
light with a typical working life of 8000 hours, followed by instant demise, plus the associated cost of disposal/re-cycling, and the purchasing choice is simple.
While many companies today are producing good quality LED lighting products, with some of these acknowledged as key players in the industry, few can boast the pedigree that Turck Banner has in the development of the core component. Such is the development of the LED that it is no longer the weak link in the finished light and where others are now finding weaknesses in circuitry and housing design, these issues have long since been resolved by Turck Banner.
Having been at the forefront of photoelectric sensing for over four decades, Turck Banner is utilising the experience gained to become a key player in the rapidly expanding LED lighting market.
Key Points
- Throughout its history Turck Banner has worked on circuit development, in partnership with LED component manufacturers
- The company's LED lighting has a continuous working life in excess of 50,000 hours
- Energy efficient LEDs use as little as 10% of the energy of conventional lighting to illuminate the same area
- Orchestrating a modular approach
- RFID enables moisture sensing
- Encoder challenges rotary order
- Sustainability germinates at Turck Banner
- Sustainability through supply chain management
- Process monitoring at every level
- RFID solution as a service
- Visual factory comes into focus
- Condition monitoring starter kit
- Control on a roll!