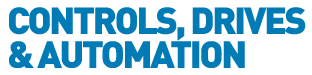
![]() |
Charlotte Stonestreet
Managing Editor |
Home> | AUTOMATION | >Handling & Logistics | >Commercial launch of 'robotic employees' |
Home> | AUTOMATION | >Robots | >Commercial launch of 'robotic employees' |
Home> | AUTOMATION | >Vision Systems | >Commercial launch of 'robotic employees' |
Commercial launch of 'robotic employees'
30 July 2020
MusashiAI, a joint venture between SixAI Ltd. of Israel and Musashi Seimitsu of Japan (a Honda Motor Corporation affiliate company), has announced commercial availability of its autonomous visual quality control inspector, autonomous forklift driver and disruptive mobile robots fleet management system.
Live trials of the technology were announced in December 2019 in Musashi Seimitsu’s factory: a visual quality control inspector for surface defects and an autonomous forklift driver robot coupled with a ground-breaking autonomous fleet management system. In under 6 months, the results of the trials have exceeded expectations and overcome technological barriers known so far in the autonomous industrial robotic market.
In addition to its initial commitment with advance payment of $10 million, Musashi Seimitsu is willing to expand the deployment of MusashiAI’s autonomous quality control inspectors and autonomous forklift drivers in its factories globally, subject to the company meetings certain development milestones.
In a further boost, MusashiAI has also secured a POC for their autonomous Quality Control Inspector with one of the world's largest bearing manufacturers. In addition to this, MusashiAI will also conduct three POCs for the autonomous forklift drivers and central management system with leading Israeli retail and FMCG groups starting Q4 this year. These agreements will be the first times the robots are being tested outside of the Musashi Seimitsu group.
Human workers have been employers’ pick for the visual quality control inspection of final industrial products because robots have not been able to surpass or even match the human ability to detect and identify surface defects quickly and accurately. Existing robotic solutions for visual quality inspection of surface defects in manufacturing lines typically have lower accuracy rates and detection speeds. MusashiAI’s ability to be able to customize the robots to suit the needs of individual customers also make it a unique offering. The completion of the live trials has confirmed that MusashiAI’s unique autonomous robotic visual inspector exceeds the speed, accuracy, and stamina of human workers in a world-first technological advance.
The other robot tested by the company, the autonomous forklift driver is navigating using MusashiAI’s proprietary fleet management system which employs sophisticated perception and decision-making software which in combination with inexpensive industry-standard HD cameras can predict incidents and prevent accidents on the factory floor. The autonomous forklift navigates routes amongst human workers through a unique technology that combines cameras with a ‘birds-eye’, control tower view of the factory floor, and a central processing unit. The trials confirmed that logistics tasks previously limited to human forklift drivers can now be autonomously performed by the robots and that they exceed modelled expectations with their unparalleled efficiency, cost-effectiveness and safety standards.
With the growth of the COVID-19 pandemic and the strong progress seen in the first three months of the trials, testing efforts were accelerated at Musashi Seimitsu’s factory in Japan for the last phase of the trial. The result has been a breakthrough in streamlining in the process of training the robots for their tasks. An advanced form of deep learning which parallels the way the human brain absorbs and assimilates information was developed, making redeploying and switching robots between tasks much easier. These improvements are central to MusashiAI’s latest robotic models, which the company anticipates will be essential in the many socially-distanced industrial settings to come.
Ran Poliakine, co-founder of MusashiAI said: “The goal of the joint venture with Musashi Seimitsu has always been to work towards our vision of Industry 4.0, where human workers do human jobs and are not trapped in manual industrial jobs.
“Globally, nearly 30 million people work in gruelling visual inspection jobs. Many of these people suffer chronic health conditions from this work, such as carpal tunnel syndrome. No doubt a large number of them have been furloughed because many industrial settings are unsafe now due to the coronavirus. These people are not key workers, but what they do is essential. Businesses will need their final products inspected, and we are offering the world a solution which can shield employees from this deadly virus and the chronic health problems associated with their work, and the major economic danger of stalling business for much longer.
“To our knowledge, current market incumbents do not offer visual quality control inspection robots which surpass the skills of human workers. Moreover, the majority of the visual inspectors available on the market inspect full assembly parts or geometric defects. Our visual inspector detects tiny surface defects, which is a far more complicated and labour-intensive task.
“These robots are designed with people in mind – the vision is that they integrate easily onto the production floor where there will still be some human workers, but release other works from this particular drudgery. They are friendly looking and easy to deploy wherever they are needed. Our OPEX model means clients can deploy robots when and where they need them, without extensive CAPEX.
“The interest from Musashi Seimitsu coupled with our latest finalised proof of concept trials with a world-leading manufacturer and three leading Israeli logistics companies is a great sign of confidence in our technology and the gifts it brings to the future of humanity. I am excited about the company’s next steps.”
For info visit: www.musashi.co.jp/en/
- The digital battlefield
- Humanoid resource management
- Next-generation ultracapacitors
- What Wi-Fi 7 means for manufacturing
- SPE Offshore Europe looks to the future
- Unlocking the untapped potential of inverters
- Automated platform for collaborative applications
- Wearable robot
- Pump up the savings
- Ruggedisation and miniaturisation converge in connectors
- Turnkey hovercraft drivetrain guarding
- More Ways of Identifying Objects
- Balls to Gravity
- ROBOTS GIVE FASTER CELL TOOL CHANGE TIMES
- ROBOT FOR DELICATE ASSEMBLY
- FIRST FASTBOX
- NUMBER OF ROBOTS IN UK ON THE RISE
- Tailor Made For Automated Warehouses
- Number of Operators Reduced
- Prevents Potential Material Release