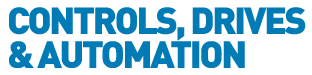
![]() |
Charlotte Stonestreet
Managing Editor |
Home> | AUTOMATION | >Systems | >Realising the potential of transformative technology |
Realising the potential of transformative technology
23 June 2025
Controls, Drives & Automation talks to Ben Lloyd, product manager - electric automation at Festo

Controls, Drives & Automation: What are the key trends in electric automation shaping the market and Festo's product development?
Ben Lloyd: For manufacturers, the ability to respond quickly and effectively to changes in market demand is more important than ever. Delivering effective automation solutions increasingly requires true openness, modularity, and flexibility. In addition, the old delineations between pneumatic and electric drives are becoming blurred, as developments in one field influence the other and customers seek optimised solutions that deliver the best of both worlds.
The advent of multi-protocol technology is a direct result. Hardware is becoming increasingly technology-neutral, allowing users to choose the software that best fits their needs. In an industrial automation context, this trend simplifies the implementation, alteration, and modification of processes without significant capital investment, providing new opportunities to gain a competitive advantage.
Festo offers a comprehensive portfolio of linear and rotary mechanical systems, servo drives and motors, controller solutions, and I/O systems, complemented by a diverse and open range of communication options, enabling machine builders to deliver seamless automation solutions. We are also combining our pneumatic and electric automation expertise to develop hybrid solutions that integrate multiple technologies, giving machine builders and end-users the best of both worlds.
CDA: What role do digital twins and simulation tools play in Festo’s electric automation offering?
BL: Ensuring that you have the right choice and size of automation component for the task is vital for optimising system performance. Online selection and simulation tools provide fast, reliable results and save so much time. For example, Festo’s Electric Motion Sizing tool quickly calculates the most cost-effective solution based on your performance requirements by using a small number of application parameters. Uniquely, it is suitable for both linear applications, where motors and mechanics must be sized together, or purely rotary scenarios. The solutions this tool identifies can be seamlessly connected to ProfiNet, EtherCat, or EtherNet IP networks without further work or complex calculations, such as mass moment of inertia.
The seamless journey continues with commissioning. The Festo Automation Suite (FAS) allows commissioning engineers to configure all products – from remote I/O to pneumatic valve terminals, PLCs and servo drives – in a single free tool. The commissioning files can be directly imported from the Electric Motion Sizing tool and FAS automatically connects to the Festo cloud to download project-specific documentation and updates within the software. It even incorporates Codesys code for programming PLCs and Motion controllers.
Our aim is that all this data will be fed into a Digital Twin to enable faster machine and system development, reduce errors, and improve predictive maintenance, but implementation is still a little way off. The main barrier has been the multitude of data in different formats, such as CAD, PDF or paper manuals, which makes data management problematic over the product’s entire lifecycle. This lack of digital continuity also makes it difficult to fully network all objects. Festo is therefore working hard with other international automation partners and the Industrial Digital Twin Association on seamless and consistent communication technology, such as OPC-UA, that will fully realise the potential of digital twins for our electric automation customers.
CDA: How is Festo incorporating AI or machine learning into its electric automation systems?
BL: AI has massive potential in the context of industrial automation, particularly in predictive maintenance. It allows anomalies in process data to be easily combined with machinery data and evaluated to detect deviations from a normal state earlier than traditional condition monitoring approaches. This means manufacturers can reduce unplanned downtime and increase overall equipment efficiency.
Transformative technologies such as the Festo Automation Experience (Festo AX) are helping to accelerate AI adoption. Festo AX uses AI based on machine learning, allowing users to extract genuine value from their machine data and enabling them to make prompt and well-informed decisions. It can be integrated flexibly into customers’ systems on premise, in the cloud, or programs can run on edge components directly by the machine. This addresses one of the main challenges between IT and OT, of complying with ever stricter cybersecurity policies. Festo AX can be applied to improve productivity, reduce energy costs, prevent quality losses, optimise shop floors, and facilitate the creation of new business models through data analysis and understanding.
CDA: What sustainability considerations are being built into Festo’s electric automation technologies?
BL: Sustainability has many facets. Reducing energy consumption — and thereby carbon footprint and operating costs — is a key focus for Festo. For example, our range of selection tools ensures the ‘right’ products are selected as a key to energy efficiency. Our servo drives recover and reuse surplus energy using DC linking technology, so energy recovered during deacceleration cycles can be used in other servo drives.
Another aspect of sustainability is ensuring that products operate efficiently for as long as possible. Festo’s AX software provides monitoring of electrical devices and provides insight into the health of a mechanical system. This helps prolong longevity and can often prevent the premature replacement of components that have not yet reached the end of their serviceable life. Unlike many conventional preventative maintenance regimes, this approach prevents unnecessary purchases and wasteful disposal of perfectly serviceable components. We also offer sets of wearing parts and consumables, or the ability to repair many of our products, further reducing waste and promoting service life extension.
In our manufacturing operations, the selection of non-critical raw materials, the use of lightweight construction methods to limit the amount of material used, and production in ISO 14001-certified plants contribute to resource conservation and a low carbon footprint. Our use of photovoltaic (PV) systems to generate our own energy further contributes to lowering our greenhouse gas emissions. Indeed, Festo UK operates as a carbon-neutral organisation and uses the ISO 14064-1 standard, externally audited by NQA, to validate this claim.
CDA: What are the most common challenges customers face when transitioning from pneumatic to electric automation?
BL: The most obvious challenge is the sheer range of products available! Let’s take linear motion as an example. It used to be a straightforward choice between pneumatic or electric drives. However, recent technological advancements have expanded the available options. For instance, point-to-point electric drives can replace some movements that were typically performed by pneumatic cylinders, resulting in cost reductions. Similarly, the latest pneumatic technologies now include features that were once exclusive to electric drives. New servo and digital pneumatic technologies add even more choice. So, finding an optimal linear motion solution that balances performance, cost, and energy efficiency has become more complex.
To streamline this decision-making process, Festo offers a software tool called the ‘CO2 & TCO Guide.’ This tool compares the electric and pneumatic drives from Festo’s product portfolio, providing a clear comparison of energy consumption, CO2 emissions, initial purchasing costs (tailored to application conditions), and total cost of ownership. Users simply enter the key application criteria and receive a graphical, illustrated cost calculation for periods of up to 10 years. Because we offer electric and pneumatic automation solutions, the advice is entirely technology-neutral.
When it comes to electric automation, customers can be daunted by the thought of complex programming or software issues, combined with the shortage of skills, involved in implementing electrical solutions. Festo offers a range of products that can help customers transition from air to electric. Our Simplified Motion Series (SMS) comprises motors and controllers integrated into a linear or rotary actuator that can be programmed directly from a simple interface on the device. All they need is a 24V DC power supply and a simple logic signal.
CDA: Can you give an example of a recent customer application where Festo’s electric automation products significantly improved process efficiency or flexibility?
BL: We’ve recently worked with Lumico, RH Electrical Engineering, and DPB Automation to deliver a unique modular automated storage and retrieval system (ASRS) featuring Festo robotic handling technology for a major manufacturer of hard disk drives (HDDs).
The HDD factory makes around 400 million pieces per year. The production lifecycle of each piece is about 22 days, representing a significant quantity of work-in-progress at any one time. The objective was to reduce human interaction by automating the transfer of product between production cells before packing and shipping. This demanded an ASRS with a capacity of 8,500 drives that could achieve rapid cycle times of 3.3–3.6 seconds from ‘product in’ to ‘product out.’ These speeds made it impractical to have one monolithic system, so DPB Automation designed a modular system using a four-grid or six-grid configuration to optimise footprint and make use of the vertical space in the factory. There are six systems in all, each running on a cycle time of 19.8 seconds.
Festo CMMT-AS multi-protocol servo motor controllers and Festo CMMT-ST multi-protocol 24 V DC servo controllers are used to achieve the necessary speed and precision for pick-and-place. Due to the unusual configuration, the actuators in the Cartesian handling system couldn’t be connected using a mechanical link. Instead, the designers elected to have independent motors on each Z axis and run them in a master-slave control combination using a communication link. This involved modifying our software to enable the CMMT controllers to deliver the desired levels of performance.
The ASRS has increased manufacturing capacity and supports ‘lights out’ operation. The barcoded products also improve traceability, which is crucial for gaining the environmental, sustainability, and quality certifications that are vital to securing future contracts.
- Solve machine setting issues
- Pneumatic robotics meets artificial intelligence
- The smart way to milk
- Connectivity and flexibility
- Integrated positioning drive
- Accelerating technological developments
- A question of application
- Simplicity & efficiency with selection & assembly
- Save costs when selecting process valve solutions
- A real Industry 4.0 solution
- SWISSLOG SECURES MAJOR ORDER
- IMPROVED PERFORMANCE & RELIABILITY
- Engine Facility
- BULK AUTOMATION
- Integrated Packaging Solutions
- INTEGRATING ELECTRIC AND PNEUMATIC CONTROLS
- Rockwell Automation expands Midrange system portfolio
- Yokogawa joins Friends of the Supergrid
- Festo extends reach of VTUG and MPA-L valve terminals
- Siemens extends TIA Portal engineering framework