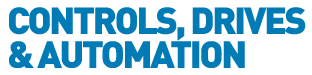
![]() |
Charlotte Stonestreet
Managing Editor |
Home> | IIot & Smart Technology | >IIoT | >IIoT and the digital twin |
IIoT and the digital twin
28 July 2022
Most manufacturing lines depend on human supervision. However, this is changing as processes become smarter, heralding the arrival of Industry 4.0 (I4.0) or the Industrial Internet of Things (IIoT), says Joe Lomako

I4.0 AND IIoT can be described, in the simplest terms, as “industrial processes and manufacturing connecting directly with the latest IoT technology”. The new technologies being deployed are almost endless, but include sensor technologies, intelligent programmable logic controllers (PLCs), machine learning, artificial intelligence, predictive analytics and edge computing. This is just the first step as many designers and innovators are now also producing a digital copy of their systems at the same time as they build the physical system. This is known as the ‘digital twin’.
The digital twin is an exciting move forward. It uses innovative technologies such as artificial intelligence (AI), IoT, virtual reality (VR/AR), and sensor technologies to create digital models (twins) of real devices, systems, or processes such as a manufacturing or production line – the so-called ‘smart factory’. These models can then be used to monitor the real system to improve production processes, for example, to help predict breakdowns. This will help manufacturers to optimise performance and more accurately predict business obstacles.
However, any digital twin needs sensors to provide the data. Advanced new sensors are finding their way into modern manufacturing lines to facilitate informed decision-making. However, this is just the beginning as it goes beyond the smart factory concept. It is believed that everything can be modelled using digital twin technology and its application can be quite varied.
Consequently, this ongoing digital transformation is driving innovation across a wide range of areas, including aerospace, mobility, agriculture, energy, healthcare and transportation. It’s unlikely that any sector is untouched by these new technologies. Some other excellent examples of digital twinning include the human body, the city of Shanghai or Tesla electric cars. These are essentially big “data sets” which replicate the physical examples to a high degree of accuracy, improving the correlation between measured and simulated performance, which then contributes to an accelerated development of improved systems and products.
Smart factory challenges
The benefits for industrial manufacturing are potentially endless. However, we will face massive disruption as development moves towards fully connected, self-organising intelligent factories. For example, this will trigger significant potential for efficiency improvements, such as reducing energy consumption and preventing downtime.
In theory, sensors and physical components can be combined to form a smart factory. It sounds simple. However, many of these “sensor devices” may employ different technologies and protocols which need to communicate, and which could potentially cause interoperability issues.
The solution to this challenge could be the ‘digital twin’, as AI could be used to learn how to make the physical constituents work better together. This is the whole ethos of the digital twin: “monitor to make better”.
A typical manufacturing environment is usually made up of several systems that are interconnected, often running the risk of a breakdown, which could cause a ripple effect throughout the entire production line. For example, if a robot, which performs an important serial function upon which the rest of the production relies, breaks down it can have serious consequences. Production could be slowed, interrupted or even drastically halted, leading to a loss of revenue or even discontinuity of the business.
Manufacturers are continually looking at ways of optimising efficiency to minimise cost and boost profitability. In today’s I4.0 domain, digital twins operating in parallel to the physical factory, where thousands of sensors constantly collect, process locally (edge computing) or send back data for processing on a larger scale, are becoming more commonplace.
Specific benefits of the digital twin approach include:
- Constant monitoring – to determine if a machine is about to fail, so any potential issue can be mitigated without interrupting function, but it can be modelled on the digital twin in real-time to assess the size of any problem.
- Data monitoring and analysis - to make iterative improvements to operations, increase efficiency and reduce costs in real-time. For example, a programmed robot which is operated in a specific sequence could be constantly modelled in parallel to reduce cycle time of that sequence.
- Ability to plan - probably one of the greatest uses of the digital twin, as an entire factory can be simulated before the first brick is laid.
Of course, challenges to reaping the benefits of deploying a digital twin also exist. For example, many technologies are vying for a place in the IIoT and, as mentioned earlier, multiple technologies introduce the problem of interoperability. This means that any digital twin may have to cope with processing data from many different protocols and legacy systems. As this requires decoding and recoding activity, extra latency and a greater margin for error is introduced. There is also the cost associated with replacing existing equipment to interoperate and dock effectively with the digital twin.
Cybersecurity concerns
However, a far greater threat now lurks. As the convergence of enterprise IT and operational technology sees systems and devices exchanging and interpreting shared data, cybersecurity becomes a threat to the smart factory. Digitisation and the increasing connectivity offered by the IoT bring enormous opportunities, but also unforeseeable risks and serious vulnerabilities that can be exploited by new forms of cybercrime.
As I4.0 uses more complex technology and connectivity, these systems present a greater number of attack surfaces and have the potential to cause a much more severe impact than a mechanical breakdown. A connected manufacturing plant now becomes a target for nefarious attacks and, if not adequately protected, could have disastrous consequences. This means that robust information and digital security is a major priority factor which must be considered. Unfortunately, in many companies this is not always on the list of priorities. This connectivity is set to further increase in abundance and complexity as we get more sophisticated communication technology such as 5G and 6G
It is essential to deal with cybersecurity measures at the early planning stage of any system, be it a product or a production plant. While there are defined cybersecurity standards available globally, some may not be complete and ratified or mandatory. However, they do represent a first line of defence, and as a first step any ‘connected’ stakeholder must:
- Think “secure by design” and take a proactive approach to cybersecurity by recognising that attacks are “when” and not “if”.
- Ensure up to date compliance with all standards.
- Constantly review the “cyber resistance” status of all systems.
Many manufacturers, whilst having internal security knowledge, will nevertheless benefit from working with external advisors who have wider exposure to assessing various types of product or infrastructure, and will be better equipped to help manage threats. Building a network of trusted partners is therefore a strong first step towards planning cost-effective end-to-end security. Tackling the problems of cybersecurity risks can, after all, only be realised by comprehensive planning, periodic evaluation, updates and monitoring - from design through to obsolescence. While it is clear that the digital twin is changing industry, there remain many challenges which must still be resolved.
Joe Lomako is business development manager (IoT) at TÜV SÜD
Key Points
- The digital twin uses innovative technologies to create digital models (twins) of real devices, systems, or processes
- Many 'sensor devices' employ different technologies and protocols, potentially causing interoperability issues
- As IT/OT convergence sees systems and devices exchanging and interpreting shared data, cybersecurity becomes a risk
- Industry 4.0 ready
- What operators need to know about IIoT adoption
- Predictive maintenance leader
- The digital future has begun
- The smart future of manufacturing
- Partnership integrates freight & warehouse management
- Secure data handling
- Makes IoT available in practice
- When & where will Industry 4.0 actually happen?
- Simplifying IIoT & product suite understanding