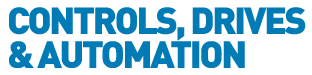
![]() |
Charlotte Stonestreet
Managing Editor |
Marginal gains in machinery safety
19 June 2018
At SICK, the approach has always been that safety and productivity are two sides of the same coin: If you can protect employees whilst enabling them to work faster, with less downtime and in more effective collaboration with the machines they are operating, then you are on to a winner. Senior product manager for machinery safety, Seb Strutt, reports
In the world of sports science, winning through the aggregation of ‘marginal gains’ is a well-established formula that has propelled elite teams to the top of their game. It’s even turned into a management theory enthusiastically adopted for continuous improvement.
Famously pioneered by Sir Dave Brailsford, general manager for Team Sky and one-time head coach at British Cycling, it goes like this: Hunting down opportunities to make a 1% improvement across a wide range of parameters can add up to a cumulative effect that helps you beat your opponents decisively.
In factory automation, the holy grail of a digital revolution – Industry 4.0 – has appealed to our human desire for sea change – a magical something that leapfrogs us right over the competition. That’s the I4.0 mindset that’s trending currently.
In British Cycling, lots of small, seemingly prosaic improvements like using antiseptic hand gel regularly, taking the athlete’s mattresses with them to each hotel so they were guaranteed a good night’s sleep, and working on some clever performance algorithms, added up to success that brought home unprecedented Olympic medal hauls.
Hunting down those tiny improvements might seem, almost boringly, prosaic, but together they could add up to uninterrupted operation at greater throughput.
Take SICK’s new ReLY safety relay. Not, you might think, a product to set the world on fire – just one of those utility devices many safety systems need. However, we’ve developed the ReLY to achieve half the response time of comparable safety relays. A 10ms gain may not be much by itself but multiply that across a number of uses and it could add up to 160/170 ms – that’s about 300mm reduction in the safety distance and a productivity improvement worth having. So, a machine builder can achieve a more compact design, and operators can interact more quickly with their machine, whether it’s a press or a cobot.
The use of safety laser scanners in Automated Guided Vehicles and Carts (AGVs and AGCs) is another example, where it’s tempting to follow the trend that suggests the technology leaps that have achieved longer detection fields represent a magic formula for success.
No Magic Formula
However, smaller protective fields are actually better suited to high output efficiency and space utilisation in a modern production environment. Rapid system safety response times in an integrated safety system enhanced by devices such as safety encoders to control acceleration and braking, can achieve the required safety in AGV operation in a smaller footprint.
So, it’s more important that field sizes are are kept to a minimum, by optimising the total response time of the safety devices and associated control system and using scanners, like SICK’s MicroScan3, with the highest possible detection reliability to enable multiple field evaluation without compromising performance.
Take another simple example: one of our customers recently invested in an integrated safety control system, using SICK’s Flexi Soft software, on a large paper corrugating machine. The upgrade eliminated the tedious job of testing a large number of E-Stops on the machine manually during maintenance downtime, because the E-Stop system is now globally controlled and monitored.
The additional diagnostics capability afforded by an integrated safety system, using the SICK Flexi Soft controller, can be one way of identifying all those 1% improvements that can add up to make a difference.
In machinery safety, hunting down multiple marginal gains can ensure safe, compliant operation whilst enabling greater efficiency. Finding those improvements comes down to choosing the right safety device and control system with the right performance capabilities and consulting with qualified experts to do the number crunching.
Key Points
- In industry, like sport, lots of small, seemingly prosaic improvements can together add up to uninterrupted operation at greater throughput
- With SICK’s new ReLY safety relay 10ms gain may not be much by itself, but multiply that across a number of uses and it could add up to 160/170ms
- Flexi Soft software has eliminated the tedious job of testing a large number of E-Stops on a machine manually during maintenance downtime
- Hygienic sensing systems
- Non-contact linear encoders
- Fully-automatic smart vision inspection
- SICK's advanced IO-Link encoders streamline machine controls
- I4.0-ready functional safety
- Localisation sets AGVs free from reflectors
- Up For A Challenge
- Speed, precision & accuracy
- Smart Factory doors open
- Vision of a software-driven future
- No related articles listed