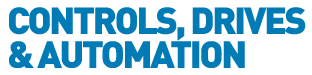
![]() |
Charlotte Stonestreet
Managing Editor |
Preparing AM parts for factory floor production
29 November 2023
The availability of more advanced additive manufacturing (AM) technologies and the increasing need for complex parts and geometries means that improving the design process is more important than ever. Colin Cater explains how manufacturers can prepare their designs for production-scale builds.

ACCORDING TO a report by AMPOWER, the AM market, including metal and polymer systems, is expected to have a compound annual growth rate (CAGR) of 17.7 per cent until 2027. The introduction of innovative, more practical materials and technology has expanded the capabilities of additive in full-scale production, making it easier than ever to integrate an AM system on the factory floor.
The value of automation
When preparing designs for end-use part production, automated software can help manufacturers improve traceability, giving the user significant freedom over their computed aided design (CAD) models.
Once the CAD file is ready, the two most important factors for build preparation are part orientation and support. The system operator must orientate the part on the build plate using the best strategy for the type of machine. Technologies with in-built automation, such as the Stratasys F370CR FDM printer, will suggest appropriate orientation options based on the part and its requirements. The software in these machines can accommodate designs from almost any production technology and provide intuitive prompts so that manufacturers can select the best build strategy.
Supporting the build
Building supportive internal structures into the CAD file is often a design necessity when moving from designing parts for subtractive to designing for additive. To strengthen the part, engineers can design structures using different techniques, including hatching for FDM and polymer and lattice structures for lightweight metal components.
Manufacturers are sometimes concerned about how these internal structures will impact the final part. We work with several templates, including those for both strong and lightweight parts. There are also other options, such as dental-specific templates to support labs in producing models and implants. Manufacturers using metal AM systems, for instance, may want to minimise the lattice structure’s thickness so that the support resembles a thin scaffold to reduce the weight of the overall part. For example, lightweight is a desired property in electric vehicle production not least because it reduces demand on the battery.
Recently, UK-based manufacturer of ultra-lightweight, low-pressure air distribution systems, Senior Aerospace BWT, installed two industrial-grade fused deposition modelling (FDM) printers at its facility. Already, the company has seen significant weight, cost and lead time savings compared with traditional manufacturing processes.
Looking ahead
The manufacturing world is facing several challenges – the legacy effects of Brexit, supply chain disruptions and long lead times on imports from overseas. The increasing skills shortage – 36% of vacancies in manufacturing are proving hard-to-fill, according to Make UK – is also a concern. Going forward, what we need is a sensible balance of skills and advancing technology so that manufacturers can maintain a competitive edge and keep their production processes on track – and using AM for mass production may be integral to this.
In some instances, the traditional skills needed for fabrication, welding and machining are moving overseas. However, for those keeping production on site, AM can help manufacturers overcome these hurdles while optimising part manufacture – from design to the factory floor. Those that have in-house printing capability have the freedom to test their designs and determine which one offers the greatest strength and other desirable properties. On the other hand, those still receiving parts from overseas don’t have the option of printing multiple parts instantly, causing much delay and frustration.
Demand for AM-built end use parts is increasing, and manufacturers must adapt their design strategy to suit. Automation can help create a robust CAD file with the necessary support structures and prepare a strong build. From this, they can gain a competitive edge over businesses still reliant on increasingly stretched traditional manufacturing skills.
Colin Cater is metal specialist at Tri-Tech 3D
Key Points
- Moe innovative, practical materials and technology has expanded the capabilities of AM in full-scale production
- When preparing designs for end-use part production, automated software can help manufacturers improve traceability
- Building supportive internal structures into the CAD file is often a necessity when designing for additive
- Bearings for wind turbine upgrade
- Ultra-energy efficient parcel sortation robots
- GOLDEN OPPORTUNITY TO OVERCOME UNCERTAINTY IN SPECIALITY METALS SUPPLY
- Six months to comply with new Batteries Regulation
- UK manufacturers face historic need for automation
- Automate to remain competitive
- Ultrasound condition monitoring webinar
- Professor Robert Richardson elected new Chair of ESPRC UK-Robotics & Autonomous Systems Network
- Successful field tests for astronaut smart glove
- Pioneering start-ups selected for AI accelerator