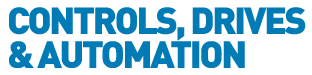
![]() |
Charlotte Stonestreet
Managing Editor |
Home> | MACHINE BUILDING & ENGINEERING | >3D Printing & Prototyping | >FDM STREAMLINES MANUFACTURING |
FDM STREAMLINES MANUFACTURING
25 September 2012
Investing in Fused Deposition Modelling systems has enabled Thogus Products to focus on small-volume moulding with highly engineered materials and help position the company to compete with high-cost fabrication shops
Established as Master Mold & Die in 1950, Thogus Products is a company rooted in injection moulding. In 1997, 56% of sales came from automotive clients. A decade later, feeling the pressure of a poor economy and recognising the threat of limited diversification, Thogus started to search for new sources of revenue.
Company president,Matt Hlavin, decided to shift Thogus’ focus to small-volume moulding and highly engineered materials using Stratasys Fused Deposition Modelling (FDM) systems. Moving to small-volume production positioned Thogus to compete with high-cost fabrication shops due to its new lean, nimble manufacturing process.
"One of my first major decisions as president was to purchase two Fortus 400mc machines to aid in product development and provide more value to our clients,” recalls Hlavin. "Stratasys technology uses the same thermoplastic materials we use in injection moulding, and we can produce product parts in small volumes until our clients justify the production tooling, which is very expensive.”
Quickly realising a return on the initial investment, Hlavin went on to invest in advanced technology, capital equipment and automation, including two Dimension SST 1200es 3D Printers, a smoothing station and a Fortus 900mc 3D Production System. "We were so confident in Stratasys, we purchased every material that Stratasys offers – ABSplus, ABSi, ABS-M30, PCABS, PC, Ultem 9085 and PPSF/PPSU – in order to handle the concept ideation, functional prototyping, prototype tooling, filtering, end of arm tooling and final production demanded by our clients,” says Hlavin.
UNCONVENTIONAL WISDOM
In a typical example of how the Stratasys quipment has opened up new business opportunities for Thogus,Vitamix, maker of commercial blending machines, was purchasing SLA prototype parts from local service bureaus when Thogus introduced prototype parts made with real thermoplastics. "We showed them what our machines could save them in terms of time and cost,” says Hlavin. "They loved it because the parts were much more robust, and they could do functional testing with our parts.”
Hlavin even encouraged Vitamix to buy its own Stratasys FDM machine. And they did. "Every project is urgent at Vitamix, so now we handle all overflow orders the company doesn’t have capacity to fulfil in-house. Since the machines speed up the manufacturing process, we’re actually getting more work from them than before.”
STREAMLINING MANUFACTURING
In addition to revolutionising his injection moulding business, Hlavin has found FDM to be invaluable on the manufacturing floor. "A lot of our work is in prototype development: short run, fast turn over. Stratasys FDM Technology can take a CAD file and build a part in hours.We want to provide our clients functional parts they can use for testing and validation,” says Hlavin."But what we’ve found after bringing in the machine is that there’s a far greater purpose to
FDM. And it’s in our manufacturing process on our floor.” FDM touches every aspect of business at Thogus. "We have automation, robots on our machines. Rather than using a steel plate or aluminum frame for big, heavy end of arm tools that are expensive and take long time to build, we can take 3D geometry and print an end of arm tool that weighs 70-90% less. And we can do it in less than 24 hours.”
Hlavin has found that this advantage has taken direct labour cost off of the manufacturing floor. "I don’t care what industry you’re in,” he says. "FDM will impact it. I don’t know another technology that can do what FDM can do.” Stratasys equipment is available in the UK through Laser Lines.