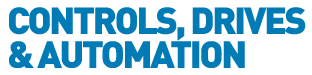
![]() |
Charlotte Stonestreet
Managing Editor |
Home> | IIot & Smart Technology | >Industry 4.0 | >Looking to a virtual future |
Editor's Pick
Looking to a virtual future
13 June 2024
Mike Loughran delves into the transformative impact of cutting-edge technologies on industrial processes

AUGMENTED REALITY enhances communication by overlaying digital information onto physical environments, facilitating remote access to instructions and data, thereby improving productivity and safety while addressing skills shortages through risk-free simulations. For instance, GE Healthcare delivered instructions to workers using augmented reality to enhance batch execution, operations, equipment setup, and training in collaboration with Rockwell Automation.
The collaboration will enable drug manufacturers to enhance efficiencies, expedite market entry, and deliver personalized medicines through innovative solutions. This joint effort marks a pivotal step in transforming biopharmaceutical manufacturing to meet the demands of the Biopharma 4.0 era. Together, they will assist biopharmaceutical companies in creating flexible and scalable facilities of the future designed to respond to market demands rapidly, streamline production technologies, and adapt to varying manufacturing environments.
Augmented and virtual reality (VR) is revolutionising training in manufacturing by offering immersive, interactive learning experiences. VR simulations allow workers to practice complex tasks in risk-free environments, enhancing skill development and safety. Trainees can virtually navigate manufacturing plants, operate machinery, and perform maintenance procedures without real-world consequences. This hands-on approach helps in understanding intricate processes and mastering technical skills.
It also supports remote training, allowing geographically dispersed teams to receive consistent instruction. By providing realistic, repeatable training scenarios, VR reduces training time, lowers costs, and increases productivity. Ultimately, VR equips manufacturing workers with the confidence and competence to handle real-world challenges effectively, driving operational excellence and safety in the industry.
Engaging users
Virtual reality takes innovation further by immersing users in entirely digital environments, enabling advanced training, simulation, and remote collaboration. Rockwell Automation's Emulate3D digital twin software exemplifies this, allowing workers to visualise and interact with virtual replicas of manufacturing environments, expediting design phases and ensuring adaptability to changing market dynamics.
When commissioning a project, virtual reality and digital twin technology can ensure the project scope is fulfilled on budget and on time. As the commissioning date approaches, performance stakes rise with potential complications such as unexpected stoppages, missing sensors, or HMI sequence issues. Correcting these issues during commissioning can be 100 times more expensive than during the design phase. Additionally, rework delaying the customer's production start date can have significant ramifications.
To mitigate these risks, machine designers increasingly turn to virtual commissioning using digital twins and simulation for control testing before machine construction. This strategy's benefits are clear: identifying and resolving design issues early in the cycle saves costs and keeps the project on schedule.
The dynamic digital twin used for this purpose is more than a 3D model; it includes physics to simulate how the design operates and interacts with people or other machines. This review can occur as soon as the design is complete before purchasing or manufacturing begins.
Daifuku Webb, a material handling systems maker, has successfully used virtual commissioning. For an airport project, virtual control testing reduced field time from several months to three weeks. System installations went smoother as PLC code functions had already been tested, allowing Daifuku to demonstrate system functions thoroughly before field deployment.
Creating a digital twin involves three steps: starting with CAD files, adding a mock-up of the machine's movements and sensors, and integrating the CAD with the controller and its tags. This setup allows for comprehensive digital testing of the machine and its logic.
A system subjected to virtual testing and commissioning benefits everyone. Production workers receive a more thoroughly tested system that performs according to specifications. System integrators can predict commissioning times more accurately and plan accordingly. All stakeholders win when projects are completed on time and within budget. Virtual commissioning produces tangible returns and raises confidence in implementing industrial automation systems.
Removing risk
A manufacturer of dry pet food has faced challenges in commissioning automation systems and often experiences costly overruns. The plant cannot operate unless the PLC codes are commissioned, and performing this task in a live environment can lead to incomplete software layers and unmet performance expectations.
To mitigate these risks, the company has turned to Emulate3D for virtual commissioning, utilising digital twins and simulations to test controls before installation. This approach identifies potential design issues early, allowing for timely rectifications that save costs and keep projects on schedule.
Emulate3D's dynamic digital twin goes beyond a simple 3D model by incorporating physics to simulate operations and interactions with people or other machines. This enables thorough reviews as soon as the design is complete, long before any manufacturing begins.
The manufacturers latest project automates the dosing of small raw material inclusions. The containers, each holding up to 50 kg products, are stored in an automated warehouse with a capacity for around 2000 containers. Raw materials are delivered into these containers at infeed stations and dosed at three stations as needed for manufacturing orders.
The containers are then conveyed to a small storage warehouse linked to tipping stations, where they are retrieved, emptied, and cleaned before reuse. This system replaces the manual process, significantly increasing production volumes and reducing waste and contamination.
Virtual commissioning shifts control testing away from the critical path, allowing it to be conducted offline. This approach ensures thorough testing without hardware constraints and enables reliable testing of proposed control system changes while maintaining current system production.
Integrating augmented and virtual reality in industrial automation transforms training, project commissioning, and overall efficiency. By enhancing communication, enabling risk-free simulations, and streamlining processes, these technologies are poised to drive significant advancements, ensuring a future-ready, agile, and innovative industrial landscape.
Mike Loughran is director, intelligent devices, software and control business - EMEA North Region at Rockwell Automation
- Connects manufacturers and safety system integrators
- Faster & more secure data access
- Ethical accolade for Rockwell
- Rockwell launches new open architecture industrial computers & thin clients
- Easing entry to smart manufacturing
- A modular approach in manufacturing
- Registration open for Automation Fair 2025
- Device support expanded
- GE Healthcare & Rockwell Automation collaborate
- Seamless AI integration
- Industry 4.0 ready
- Intelligent interlocks
- The digital future has begun
- The smart future of manufacturing
- Partnership integrates freight & warehouse management
- When & where will Industry 4.0 actually happen?
- Education key to unlocking I4.0
- How well is your smart farm running?
- Digitalisation, automation & electrification
- Industry 4.0 guidance platform