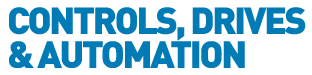
![]() |
Charlotte Stonestreet
Managing Editor |
Home> | IIot & Smart Technology | >Cyber Security | >Helping SME food factories be cyber-smart |
Home> | INDUSTRY FOCUSES | >Food & Beverage | >Helping SME food factories be cyber-smart |
Home> | IIot & Smart Technology | >IIoT | >Helping SME food factories be cyber-smart |
Helping SME food factories be cyber-smart
04 May 2021
Phil Brown explains the benefits of switching to smart equipment, and how you can protect your organisation’s digital framework
While the digital transformation known as Industry 4.0 began on the factory floor, not all of today’s manufacturers are ‘smart’. In fact, according to a recent study by Deloitte, just 20.7% of manufacturers surveyed rated themselves as ‘highly prepared’ for the Fourth Industrial Revolution. Yet the benefits to food and beverage producers of incorporating connected technology into their processes are well documented. Smart technology can help organisations to make informed decisions that can turn a business into a predictor rather than a reactor.
One reason, which still deters some food manufacturers – in particular SMEs – from taking the digital plunge, is the risk of a cybersecurity breach. Indeed, as more food processing equipment gains coveted Industry 4.0 status, so the threat of data breaches grows.
Fortunately, there are steps that companies can take to protect their connected devices from hackers and other unwanted interference.
Dynamic data
Digital fear is still prevalent in the food industry, particularly among SMEs. Yet, the benefits of transitioning from on-premises, hard copy data to a digital, cloud-based Food Quality Management system are multiple – not least increased accessibility and the ability to manage and use data in a more sophisticated way.
Phil explains: “Today’s ‘smart’, connected metal detectors allow immediate and remote access, enabling food manufacturers to view current equipment status and take any necessary action to ensure continued, smooth production. Production managers can review and compare operational data, helping them to spot trends and patterns, such as when and where the most rejects are occurring. This can enable them to increase productivity and improve their operational efficiency.”
Fortress has responded by developing remote management solutions. This technology allows multi-site food production plants to manage operations from anywhere in the world using smart phones, tablets and laptops.
An unlimited number of Fortress metal detectors can be connected wirelessly using a powerful back-end SQL to monitor activity and generate reports in either PDF or Excel format. Reports can be selected for a specific production line and/or time period. For record keeping, event and performance information is stored securely and remotely for a minimum of 10 years, with the option to extend storage capability to 20+ years.
Supporting HACCP compliance
Despite fears of cybersecurity breaches, the risks of using paper records can actually be higher than digital data. Not only can manually collated information be incorrectly recorded, forgotten or lost, results can also be deliberately falsified. If a food producer cannot prove when and where inspection of their products took place, they may then be unable to demonstrate HACCP compliance and could be forced to re-inspect an entire batch. This not only slows down production, at worst it could trigger a product recall.
However, with today’s smart detectors, Cloud-based records are instantly available to demonstrate when and where testing took place. Some models even comprise automatic testing functions, such as Fortress’ Halo auto system. This ensures the reliability and efficiency of the inspection equipment with minimal operator intervention.
Producers can feel confident that their product is good to distribute, thanks to indisputable evidence that their machines are working correctly and that an inspection has been carried out. Furthermore, if a contamination is found, these comprehensive digital records also help to limit the incident and streamline the investigation by eliminating locations and timeframes.
Network separation
The threat of a cybersecurity breach is ever-present in today’s connected world and food manufacturers of any size would be naïve to think their company is not at risk. In order to ensure their smart equipment does not leave them vulnerable to an attack from either external or internal threats, regular consultation with an IT specialist is essential. However, there are some simple steps to help mitigate the risks.
The most important line of defence is to keep your networks separate. This could involve setting up a corporate network, for areas such as finance and HR functions, and an industrial network, which governs the operational side of the business that keeps the factory running.
Since the advent of the Internet of Things, there has been a rise in outside companies (such as connected equipment manufacturers) requiring access to a firm’s internal networks. This could be to collect the data that’s being recorded, in order to improve systems and processes, or to open the control of whatever that appliance does. For example, if a metal detector has a fault, the supplier may request remote access to the machine to rapidly fix it and reduce downtime.
Create a DMZ
To protect against unwanted threats either to the corporate network (such as accessing confidential personal or financial records) or to the industrial network (such as changing recipe mixes or overriding smart freezer temperatures), it is advisable that food producers apply the principal of least privilege. “This means never giving a user more access than they need to perform their task,” explains Phil.
One way to do this is to create a third network. Known as a DMZ, this third network acts as a secure path between an organisation’s internal networks and the external network, and protects the internal networks from outside interference. By only opening the particular ports needed to communicate on one network at a time, it ring-fences the rest of an organisation’s data and operational controls, and alleviates much of the risk.
Increase traceability
Separating networks and limiting third-party access should cut the threat of an outside body infiltrating digital framework by approximately 90%. Yet, while the risk from ransomware, phishers and hackers should not be underestimated, the greatest risk to SMEs regarding their connected equipment is actually more likely to come internally.
In order to mitigate this, it’s important to design any system with traceability in mind. Some of the latest metal detectors come with unique user-specific login details. If an operator wants to make a change to the operational status or machine settings, they must first input their username and password, which is recorded onto a database and stored locally or in the Cloud.
Being able to recall information regarding the person that actioned any changes, what they did and when they did it provides complete traceability. It also reduces the likelihood of internal cybersecurity breaches occurring in the first place.
The road ahead
As more and more of the equipment in food factories becomes connected, increasing volumes of data will afford operators and suppliers ever greater control, improving efficiency, ensuring food safety and providing full traceability.
Phil comments: “Increased cybersecurity measures will need to go hand in hand with this and become more sophisticated as connectivity grows. One tool that is already showing great potential is blockchain.”
Resistant to modification, a blockchain is a growing list of encrypted data (known as a block) containing a timestamp and transaction information, which can be distributed with new entries added as they occur, to form a chain. The data is recorded and stored securely, providing complete traceability throughout the entire supply chain.
“For now, SME food producers would do well to remember that the greatest threat to their cybersecurity is most likely to come from inside their organisation, and ensure traceability wherever possible,” cautions Phil “This, combined with creating separate networks and investing in robust IT support, should ensure that your company enjoys all the benefits that come from being part of today’s connected world, with none of the risks.”
Phil Brown is managing director, Fortress Technology Europe
http://www.fortresstechnology.co.uk
Key Points
- Despite fears of cybersecurity breaches, the risks of using paper records can actually be higher than digital data
- With today’s metal smart detectors, Cloud-based records are instantly available to demonstrate when and where testing took place
- A third network acts as a secure path between an internal and external networks, protecting from outside interference
- DEEPER INTEGRATION IN THE FOOD INDUSTRY
- Offering benefits to the food & beverage industry
- Reliable Feeding
- Food & beverage sector benefits
- High hygiene
- Extra reach for high speed applications
- Cut the cost of bearing downtime
- The value of continuous development
- Keeping the milk flowing
- Food handling robots