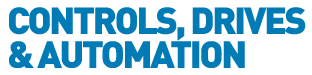
![]() |
Charlotte Stonestreet
Managing Editor |
Home> | AUTOMATION | >Controls | >The value of continuous development |
Home> | INDUSTRY FOCUSES | >Food & Beverage | >The value of continuous development |
Home> | AUTOMATION | >Systems | >The value of continuous development |
Editor's Pick
The value of continuous development
23 December 2013
The food and beverage processing industries develop and evolve at a pace that some manufacturers would find astonishing. Where its continuous development techniques lead, others often follow. For Simon Garbett of Gemba Solutions and John Rowley of Mitsubishi Electric this is an area of expertise.
Perhaps, more than any other sector, the food and beverage industry faces the most intense pressures to meet the demands of changing customer needs, strict governmental regulation and incredible competition.
Changing market conditions also affect this industry far quicker than many others, for example the availability of raw materials such as wheat crops which are impacted by weather conditions, or a sudden health scare or the vulnerability of parts supply due to world events. All have an impact on the costs and availability of the goods being produced.
So how do food manufacturers cope with these uncontrollable influences? John Rowley of Mitsubishi Electric identifies ‘speed of reaction’ and increased ‘flexibility’ as key factors.
"Having these business levers means the impact can be minimised in times of trouble and maximised in times of growth. Product and ingredient freshness and shelf life make production methods highly critical if a product is not to be scrapped as waste, this factor sets the tone for all other production management strategies.
"Dealing with these issues requires a data management system that drives a lean manufacturing strategy and delivers visibility, analysis and control of the end-to-end manufacturing process. Such a system would ensure improved yield, consistent quality and increased profitability.”
This sort of solution is often described as a Manufacturing Execution System (MES). Crucially, it provides plant level visibility to help the business make steady improvements to plant, materials handling, labour and operating procedures. Over time, this will deliver the following capabilities and benefits:
- Improved process visualisation
- Quality management
- Integration into business applications
- Reporting and analysis, track and trace
- Regulatory compliance
- Energy saving and optimisation
- Generate manufacturing intelligence
Critical to achieving continuous improvement is a holistic approach that looks at the whole plant, the supply chain and all the people involved. It is a big undertaking but essentially, just data collection and analysis. Not surprisingly, Mitsubishi has a solution designed specifically for this. Called MX4 Business, it is a data management solution that provides a cost-effective system for tracking and reporting asset-level production data such as overall equipment effectiveness (OEE) and key performance indicators (KPIs). This provides concise and easy-to-use real time and historic reports for all personnel from the plant level to the boardroom.
MX4 Business has been used in many food and drink plants, so there is a track record to explore. One of Mitsubishi’s alliance partners is Gemba Solutions, which specialises in delivering innovative production management solutions and is the manufacturer of MX4 Business."Depending on the client's requirements, our systems can reduce costs whilst increasing production capacity using the existing assets,” says Simon Garbett. "Alternatively, where production output does not need to be increased, they can maintain current capacity levels using less labour, energy and fewer machines.”
He explains that MX4 Business does not work in isolation but integrates with the backbone of the production system – the servers, PCs, PLCs and networks to collect and analyse data. "Its role is to identify pinch points, critical data and trends that indicate developing issues.” he says. "For success, it is critical to get people to interact with the data, to buy into the idea of continuous improvement through continuous vigilance.”
Not surprisingly, Simon has looked at the human interaction aspect of this work in some depth: "First you need to enthuse the management about the potential of continuous improvement. Then you install the operating systems and design them in such a way that the operational people get excited too – and if necessary change their working practices to maximise the gains.”
"We make sure that there are display screens near the machines they are controlling and that their graphics are easily understood. It is vital that there are regular meetings around the displays and that each meeting produces the next set of actions and targets.”
Simon’s people management techniques also go deeper; for instance, he knows that people work best in small teams, when there are clear goals, a no-blame culture, rewards and recognition.
"Part of the procedure is to get the shop floor people spotting waste, quick fixes, long term developments and training needs. In short, home grown solutions to problems are always better than edicts from management.”
With good data management and metrics and a positive attitude permeating a plant, improvement projects of all sizes become achievable. An advantage of working with a major controls and automation company like Mitsubishi is the depth and breadth of their capabilities.
For instance, saving energy is often a key goal and Mitsubishi can help with monitoring and reporting on existing equipment and then assist with suggestions for energy saving control solutions.
Rowley again: "In food and bev, unplanned downtime can wreak havoc. Mitsubishi technology,service and support will maximise machine reliability and minimise production losses. Our full service contract, providing 24/7 engineering cover, will typically cost less than a couple of hours of lost production.”
"In summary, it is almost a truism that where F&B leads, in terms of continuous improvement, other industries will follow – sometimes several years later.”- Powerful new advanced drive solution
- Icing on the cake
- Smart condition monitoring
- To CNC or to PLC is no longer the question
- Data reveals gap in addressing energy price volatility
- Secure data handling process
- Safety local IO modules
- Energy efficiency - it's a journey, not a destination
- Cobots maximise return on investment
- Pick of the show